Three leaders look into future of additive manufacturing
By Bruce Geiselman
Additive manufacturing (AM) has been around for decades, but until recently it was primarily used for R&D and making prototypes.
The technology increasingly is being adopted for end-use parts and products. Improvements — including faster printing technologies, materials with better properties and declining prices for printers and materials — have contributed to the trend.
The Biden administration gave additive manufacturing a boost on May 6, announcing the AM Forward program to promote the adoption of additive manufacturing.
Parts manufacturers also are beginning to understand the importance of designing for 3D printing to reduce costs while boosting part performance. 3D printer makers are helping by improving software.
Plastics Machinery & Manufacturing recently spoke with executives of three 3D printer companies — Carbon, Stratasys and BCN3D — to discuss where 3D printing of production parts is headed.
Carbon founder sees opportunities for end-use parts
Philip DeSimone, co-founder and chief product and business development officer at Carbon, said that 3D printing of end-use parts at production scale has been growing in recent years and shows no signs of slowing down.
“I think it is going to continue to be a larger and larger piece of the puzzle,” DeSimone said. “It’s not going to replace injection molding, but it’s going to augment manufacturing at a broad scale like nobody had ever imagined. For me, it’s not a matter of if, it’s a matter of when it will happen.”
AM was introduced about 30 years ago, and from the beginning, people have wanted to use it to make production parts. However, a combination of stumbling blocks — including slow print speeds, a lack of materials with adequate physical properties, poor surface-finish quality and a lack of design tools — held it back, DeSimone said.
However, faster printing speeds, more materials with better and varied physical properties, improved surface finishes and better design tools are tearing down those barriers, he said.
In addition, the pandemic, coupled with supply chain disruptions, helped fuel interest in AM. Customers who had been reluctant to 3D print production parts decided to give it a shot when traditional supplies were disrupted, DeSimone said.
In recent months, Carbon announced three major initiatives to make 3D printing of end-use parts easier.
In January, it began offering the latest generation of Carbon Design Engine software that, for the first time, is available for license by anyone, not just users of its printers. The software allows designers to generate parts with advanced lattices quickly and easily from a solid-part stereolithography (STL) file and output STL files for printing on most common 3D printers.
Also in January, Carbon introduced a new generation of Carbon Digital Light Synthesis (DLS) printers with faster print speeds and new capabilities. The M3 and the M3 Max printers offer an “idea-to-production platform” that helps companies design, prototype and then print production parts.
Carbon in February unveiled its all-new EPX 86FR, a flame-retardant photopolymer epoxy resin that works with Carbon’s patented dual-cure process. The new material is ideal for use in the automotive industry for housings, brackets and connectors where toughness and flame retardancy are required, the company said.
Carbon in recent years has partnered with numerous manufacturers, including Adidas, Riddell, Rawlings, Specialized and Ford, to print parts for shoes, sporting goods and cars. Many of these parts employ lattices that can reduce weight and offer customization, such as support in certain areas and cushioning in others, that can be difficult to obtain using traditional foam structures. Printing lattices to replace foam is one area in which Carbon has proven highly successful.
“Every time we release a production application in the field it sort of turns into three to four additional folks showing interest,” DeSimone said. “Nobody wants to be first.”
But now that Carbon has collaborated to produce hundreds of different end-use products, many of which have not been publicly announced, manufacturers are seeing that 3D printing repeatedly can be used to solve problems like those that they are experiencing, DeSimone said.
3D printing also can improve part quality and enable the creation of complex parts that might be impossible to produce with injection molding.
“It gets down to education,” DeSimone said. “A lot of folks come and say, here’s this injection molded part. How much does it cost to print? For me, if you are printing injection moldable designs, then you’ve probably already lost because injection molding is really good. What we try to get people to focus on is, how do you make a better part? How do you solve a problem that you wouldn’t have been able to solve with injection molding? That’s where the magic happens. That’s where we see success.”
Carbon urges customers to consider ways in which 3D printing might improve a part.
“I think the Vitamix part is a prime example of this,” DeSimone said, referring to a case study from 2018.
Carbon, Vitamix and The Technology House (a contract manufacturer based in Ohio) redesigned a pressurized nozzle used by coffee shops around the country. The nozzle is a critical part of a system used to rinse and clean Vitamix blenders. The nozzle previously had six different injection molded pieces and needed to be made of materials that could withstand high pressures and temperatures as well as regular exposure to bleach, detergents and sanitizers.
Vitamix came to Carbon asking what it would cost to 3D print each of the injection molded pieces. Carbon did a cost analysis and found the price would have been competitive, DeSimone said. However, he went one step further.
“Then what I showed them was a single part that had all of those parts already printed so you didn’t have to assemble it,” DeSimone said. “Then it became a slam dunk because it’s better performing, it’s more cost-effective, and it has a better environmental impact as it’s a 30 percent reduction in material used to produce the part.”
Another growth area is production parts for electric vehicles (EVs), according to Carbon officials.
The company hosted a webinar devoted to the topic on April 12 and in an email promoting the webinar proclaimed that “the widespread adoption of electric vehicles is no longer a futuristic, far-off concept.” Car companies are pledging to produce increasing numbers of EVs. To improve their range, they need to be as lightweight as possible, and that means switching from metal to lightweight plastic wherever possible.
An anticipated rise in demand for both EVs and autonomous vehicles will create huge opportunities for AM, DeSimone said. It can play a role in creating complicated parts, ranging from cooling systems around EV batteries to high-end connection systems to support all the sensors in fully autonomous vehicles.
The amount of wiring required for the sensors in autonomous vehicles is substantial. A Tesla traveling down the road in autonomous mode is carrying out an incredible number of calculations. That means more polymer-based connection systems for wiring are needed; 3D printers are ideal for making those high-end, lightweight parts, DeSimone said.
Carbon’s DLS (digital light synthesis) technology uses digital light projection, oxygen-permeable optics and engineering-grade materials to produce polymeric parts with exceptional mechanical properties, resolution and surface finish, the company said.
That has helped drive Carbon’s success in working with manufacturers on printing end-use production parts, DeSimone said.
“We give you the thermoplastic properties you’d expect out of SLS [selective laser sintering] or FDM [fused deposition modeling], but with the surface finishing resolution of SLA and PolyJet at great speed,” DeSimone said. “This is the reason we’ve had the success that we’ve had with all those production applications that you’ve seen.”
Stratasys promotes production-scale AM
Stratasys sees affordability driving demand for 3D printed production parts.
“It’s definitely increasing,” said Pat Carey, senior VP for strategic growth at Stratasys. “The No. 1 reason it is increasing is the economics are getting better. Economics drive everything … People are able to 3D print tools cheaper than they can make them through traditional means as well as end-use parts. We’re seeing that as well, where people actually make an end-use part cheaper than they would through a traditional means.”
“There are some newer technologies that are driving it to be cheaper, as well as the printers are cheaper,” Carey said. “The two main technologies driving it are powder-bed-fusion technologies and DLP [digital light processing] technologies … Those are the two fastest-growing technologies in polymer 3D printing, and we’ve invested in both of those. Those technologies are getting cheaper, as well as you’re able to print more parts [in the same amount of time]. So, you’re able to print more parts quickly with cheaper materials. That is what drives the economics.”
The price of resins is dropping in part because of the increased use of 3D printers.
“Like anything, you go to higher volumes and raw materials get cheaper,” Carey said. “As additive grows to a certain level, the large materials companies are becoming more interested in being part of this market. In the past, the market was too small for them to be interested. Before, we were a proprietary materials company. We formulated and manufactured pretty much our own materials. Now, for example, we’re partnering with third-party materials companies.”
Large chemical companies are helping develop new materials that can be printed faster and cheaper, Carey said.
In addition, accuracy and repeatability are getting better.
“The quality of the part is getting better, and that’s just through the maturity of the industry,” Carey said.
“Thinking about making a product, if I am making 1,000, I want them all to look the same,” Carey said. “I don’t want them all to be a little different. As the industry matures, the processes are getting better, more repeatable, and that is helping. The quality of the output is getting much better and consistent.”
Powder-bed-fusion printers, which include SLS and Multi Jet Fusion technologies, are popular for printing nylon 11, nylon 12 and PP, Carey said.
DLP printers are popular for end-use parts because the technology employs traditional resins, which means there is a wide variety of resins that will work in the printers, Carey said. That means injection molded parts can often be printed using the same material.
“That helps a lot,” Carey said. For example, if a manufacturer is injection molding a car part from TPU or TPE and knows how it is affected by heat, it can switch to 3D printing and continue using the same material.
Stratasys has undertaken several strategies to encourage the adoption of 3D printing for production parts.
“One thing is we’ve acquired three new technologies,” Carey said. “We traditionally had two — FDM and PolyJet. We’ve acquired another three, and we’ve plugged them into our infrastructure.”
The new technologies are powder-bed fusion, which Stratasys calls Selective Absorption Fusion, sold as H Series printers; Programmable PhotoPolymerization P3 [based on DLP technology] and sold as Origin One printers; and stereolithography, which Stratasys calls its NEO printer.
“The other thing we’re doing is we’re starting to build software ecosystems,” Carey said.
Late last year it introduced software that helps manufacturers transition from prototyping to production-scale manufacturing.
The GrabCAD Additive Manufacturing Platform is an open and enterprise-ready platform that allows manufacturers to manage production-scale operations on both Stratasys and non-Stratasys 3D printers.
New BCN3D technology targets mass production
Barcelona, Spain-based BCN3D in March announced it is developing a new 3D printing technology it calls Viscous Lithography Manufacturing (VLM) designed for mass manufacturing and producing functional parts.
VLM uses high-viscosity thermoset resins that can produce high-performance functional parts, the company said.
BCN3D officials said the new technology came from three years of research from the company’s R&D team to encourage 3D printing of end-use products.
“If 3D printing is to be the future of manufacturing and what leads us toward local production, customization, control of supply chains and sustainability, all the players in the industry should be pushing in this direction,” said Xavier M. Faneca, CEO.
VLM is a patented lithography-based process that laminates thin layers of high-viscosity resins onto a transparent transfer film, producing high-performance parts rapidly. The printer can process resins 50 times more viscous than is typical in the industry, the company said. A UV light source using LCDs cures each layer of resin as the parts are built up. The mechanical system allows the resin to be laminated onto the transfer film from tanks on both sides of the build plate, making it possible to speed up printing times or even to combine different resins to get multi-material parts and easy-to-remove support structures. A BCN3D video demonstrates the process.
The company has not announced a timeline for widespread retail availability of a VLM printer, but it has been inviting companies to apply to its VLM Technology Adoption program aimed at businesses of all shapes and sizes that want to become early adopters of the technology.
BCN3D decided to develop a new printer technology aimed at mass manufacturing parts to meet growing customer demand, company CTO Eric Pallarés said in an email interview with Plastics Machinery & Manufacturing.
“The interest in printing final parts is growing day after day, but existing commercial 3D printing solutions most of the time are not able to solve customer needs in terms of performance, accessibility or productivity,” Pallarés said. “VLM is the best balance between accuracy (thanks to the benefits of resin-based technologies), accessibility (simple hardware and process), part performance (thanks to the usage of high viscosity resins), and productivity (thanks to scalability potential of LCDs).”
AM can play a role in meeting sustainability goals and overcoming supply chain disruptions, he added.
3D printing could enable local manufacturing, which could lower companies’ carbon footprints, Pallarés said, as well as make them more resilient against global supply chain disruptions from events like pandemics and wars. Also, 3D printing allows reduced investment in capital expenditures, reduces time-to-market and enables a much higher degree of customization, he said.
BCN3D’s previous printers have been fused-filament-fabrication (FFF) units. The VLM technology will be better suited for printing production parts, Pallarés said.
“FFF is slow due to its printing strategy, inefficient to scale up due to low productivity, with limited surface quality, and with mechanical inconsistencies due to anisotropy,” Pallarés said.
VLM can produce high-performance parts more accurately and 10 times faster than FFF, he said.
While injection molding often is less expensive than AM, 3D printing has advantages.
“The cost per part is strongly conditioned by the batch number,” Pallarés said. “For big batches, injection molding will always deliver a lower cost per part. But 3D printing has multiple advantages: no minimum investment in tooling is needed so lead times are greatly reduced, and, since there are no amortization costs, continuous improvement and customization are possible.”
What types of parts are the best candidates for 3D printing?
“It will depend on the final application, but parts for structural components, under-the-hood automotive parts, electronics cases, rubber-like components, etc., are a few examples of candidates,” Pallarés said. “I see more and more companies embracing 3D printing, relying on it for small and medium batches of non-critical components in a first stage, and then, gradually migrating to it as a real productive technology, a good alternative of traditional manufacturing processes like sheet metal, CNC machining or injection molding.”
Future developments likely will include higher throughputs, more multiple-material parts and more post-processing automation, he said.
Bruce Geisleman, senior staff reporter
Contact:
BCN3D Technologies Inc., Barcelona, Spain, 34 935 95 43 43, www.bcn3d.com
Carbon Inc., Redwood City, Calif., 650-285-6307, www.carbon3d.com
Stratasys, Eden Prairie, Minn., 952-937-3000, www.stratasys.com
Bruce Geiselman
Senior Staff Reporter Bruce Geiselman covers extrusion, blow molding, additive manufacturing, automation and end markets including automotive and packaging. He also writes features, including In Other Words and Problem Solved, for Plastics Machinery & Manufacturing, Plastics Recycling and The Journal of Blow Molding. He has extensive experience in daily and magazine journalism.
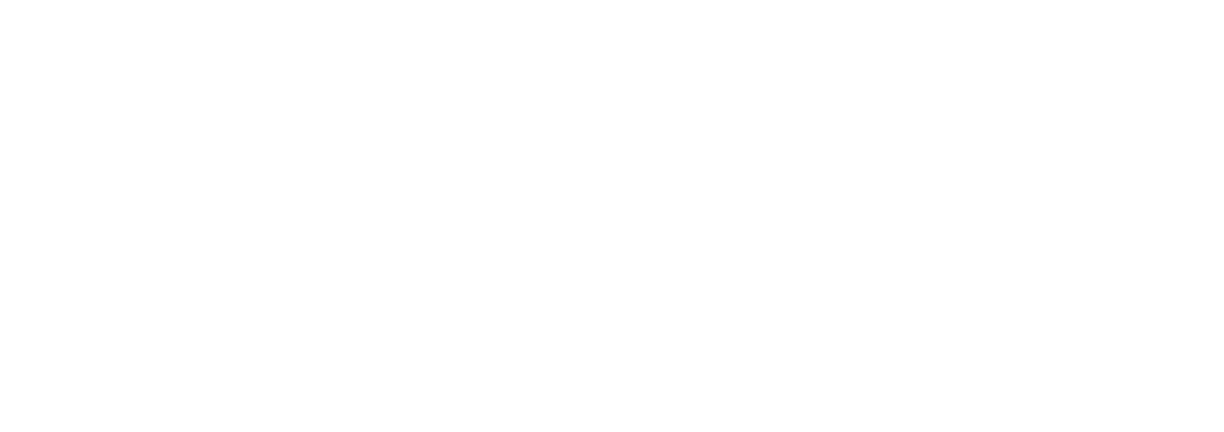