Change-up: Carbon partners with Rawlings on baseball glove with 3-D-printed features
By Bruce Geiselman
3-D printer maker Carbon has entered a new field in sporting gear. Rawlings has teamed up with Carbon and Fast Radius Inc., a digital manufacturing company, to produce baseball gloves with 3-D-printed lattice inserts that boost glove performance.
Rawlings, a supplier of gloves to Major League Baseball and creator of the Rawlings Gold Glove Award, has launched its REV1X line of baseball gloves with inserts produced using Carbon’s Digital Light Synthesis (DLS) 3-D printer technology.
REV1X gloves incorporate an intricate lattice in the pinky and thumb inserts. The lattice, produced by Fast Radius on Carbon printers, is lightweight and flexible without sacrificing protection or durability, the companies said. The inserts replace leather and the padding normally found inside gloves, and don’t wear out as easily as those traditional materials.“The glove itself — the skin of it — is still made with traditional composites and leather material,” said Phil DeSimone, chief product and business development officer at Carbon. “What we worked on with them was actually the internal components of the glove. They’re the parts you can’t actually see from the outside.”
The lattice structure helps create stability and a more secure pocket for the players to catch the ball, he said. The design also makes it easier for fielders to get the ball out of the glove to throw it, he said. The optimized lattice structure provides variable stiffness in the thumb and pinky, which significantly reduces weight without sacrificing protection, durability or performance. The lattice adds stiffness in the regions where it is necessary and softens regions where flexure is needed. DeSimone called it a major innovation in glove design.
“It’s already being used in Major League Baseball by some of the major players,” DeSimone said. “They’ve been using it since the early part of this year.”
Rawlings on July 15 announced the launch of consumer sales. Four REV1X models are available, in infield and outfield patterns ranging from 11.5 inches to 12.75 inches, at a price of $399.95.
Gold Glove Award winner and four-time All-Star shortstop Francisco Lindor, currently with the New York Mets, is one of the major league players who adopted the glove and provided feedback on the design, the companies said. Lindor is featured on the advertising images for the new glove.
“From the famous Bill Doak glove developed in the early 1920s that was the first to include a pocket and web, to the creation of the Trap-Eze web in the late ’50s, to the newly released REV1X, Rawlings has always been at the forefront of glove technology and innovation,” Ryan Farrar, Rawlings senior director of ball gloves, said in a press release. “Rawlings continues to work alongside the pros, the best in the game, to ensure our gloves are worthy of the highest level of performance, and the feedback we’ve received from Francisco Lindor validates our believe that the REV1X will forever revolutionize defense.”
The REV1X lattices are tuned with variable stiffness that conforms to the player’s hand, improving ball control. They are made using Carbon's FPU 50 material.
“People know us as a printing company, but really, we’re helping customers with the product development cycle bring products to market faster than they ever had done it before with the product at the end being better performing than what they’ve historically been able to do,” DeSimone said.
Carbon and its production partners can work with manufacturers like Rawlings by providing the hardware, software and materials to improve the performance of products via 3-D printed parts, DeSimone said.
Carbon has previously partnered with other high-profile companies developing 3-D printed components for their products, including Adidas on athletic shoe midsoles, Riddell on football helmet liners, and Specialized Bicycle Components and Fizik on bicycle saddles.
Carbon DLS is a rapid 3D-printing process that uses digital light projection, oxygen permeable optics and programmable liquid resins to produce polymeric parts with exceptional mechanical properties, resolution, and surface finish, the company said.
Fast Radius is headquartered in Chicago with offices in Atlanta, Louisville, and Singapore.
Carbon Inc., Redwood City, Calif., 650-285-6307, www.carbon3d.com
Bruce Geiselman
Senior Staff Reporter Bruce Geiselman covers extrusion, blow molding, additive manufacturing, automation and end markets including automotive and packaging. He also writes features, including In Other Words and Problem Solved, for Plastics Machinery & Manufacturing, Plastics Recycling and The Journal of Blow Molding. He has extensive experience in daily and magazine journalism.
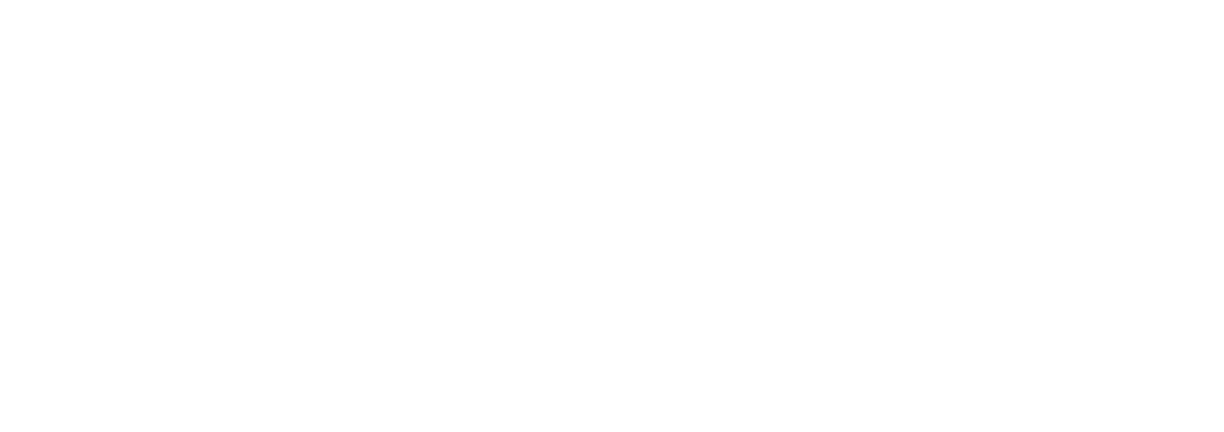