Barcelona-based 3D printer manufacturer BCN3D held a press conference today to announce the new, patented lithography-based 3D printing process that it calls Viscous Lithography Manufacturing (VLM).
VLM relies on monocomponent resins with a viscosity up to 50 times higher than those used in traditional lithography-based processes. BCN3D has a joint development agreement with specialty materials company Arkema to co-develop materials. According to a BCN3D press release, higher-viscosity resins are compatible with ingredients and modifiers that can impart a range of thermal and mechanical advantages, such as tripling the impact resistance for rigid materials, and a 200 percent increase in tear strength. Prior to today’s announcement, all of BCN3D’s printers have been fused-filament-fabrication (FFF) units.
The printing process described by BCN3D inverts the standard configuration of a lithography 3D printer’s components. With VLM, the LCD screen is near the top of the machine, facing down, and the build platform is underneath. Rather than having the build platform submerged inside a tank of resin, BCN3D’s VLM concept has two resin reservoirs, one on each side of the LCD screen, with the dry build platform in between them.
A roller in a reservoir picks up resin and laminates it to the underside of a transparent film, which transfers it into the printing area. The top side of the film rests in contact with the LCD screen, and the build plate rises to come into contact with the resin-coated underside of the film. The UV light engine cures the initial layer of the part, the build plate retreats, pulling the cured resin from the film. The film is rolled back to the reservoir, where unused resin is removed to recirculate in the reservoir. While the film is a consumable of the process, it is expected to last for hundreds of hours of printing time before needing to be replaced.
The reservoirs can contain the same resin, in which case their use can alternate for each layer. The reservoirs can also contain different resins, for example a print resin and a support resin.
BCN3D said VLM overcomes several challenges of traditional lithography-based printers. Because VLM prints are made with the resin at room temperature and unused resin is recirculated, almost no resin is wasted, and it doesn’t suffer the pot life constraints of traditional resins. Also, the potential print layer size is limited only by the size of the LCD screen, which could translate into more parts or much larger individual parts per print run.
While today’s announcement did not include news of a timeline for retail availability of a VLM printer, BCN3D said companies can begin to experiment with VLM technology soon.
“What we want with such a new technology is to get information from the market,” said CEO Xavier Martínez Faneca. “Until now, I would say that we have been able to adapt this technology to all the applications that we have been trying internally. But now the important thing is to get information from the actual users of 3D printing.”
In that spirit, the company is getting input from automotive glass manufacturer Saint Gobain and motorsport technology company Prodrive through its VLM Technology Adoption Program. Saint Gobain used VLM to fabricate 7,000 positioning fixtures in seven days, which provided annual savings of almost $78,000. Prodrive used the VLM technology to produce end-use parts, replacing parts it had previously made using BCN3D’s FFF printers.
BCN3D is now opening its VLM Technology Adoption Program to more members. Interested companies are invited to apply on BCN3D’s website. “We are super open to learn from the market,” he said.
BCN3D will display its VLM technology at the Rapid + TCT additive manufacturing event, which will be in Detroit May 17-19.
David Tillett, associate editor
Contact:
BCN3D Technologies Inc., Barcelona, Spain, 34-935-95-43-43, www.bcn3d.com
David Tillett
Associate Editor David Tillett writes and edits for Plastics Machinery & Manufacturing, Plastics Recycling and The Journal of Blow Molding. He covers new products, industry news, patents and consumer and business equipment. He has more than 20 years of experience in daily newspaper, online and magazine journalism.
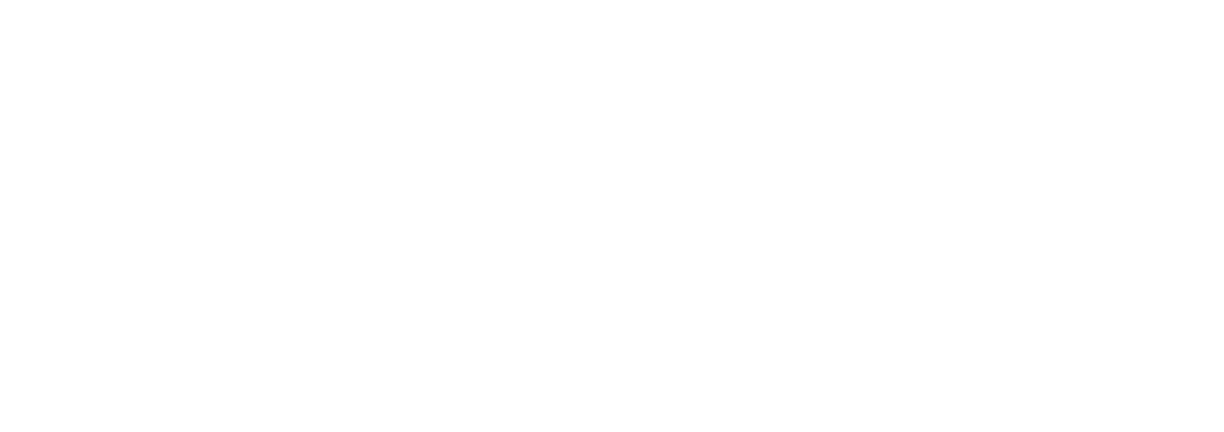