Carbon, a 3D printer manufacturer, on Wednesday introduced a new generation of Carbon Digital Light Synthesis (DLS) printers with faster print speeds and new capabilities designed to make it easier for manufacturers to print production-quality parts.
“The next generation of DLS is smarter, smoother, faster and simpler,” Phil DeSimone, chief product and business development officer, said during an online news conference. “In short, it really is the next generation, enabling customers to create more types of parts with a simpler printing experience.”
The next generation of Carbon printers comes in two models — the M3 and the M3 Max. These new printers offer an “idea-to-production platform” that helps companies design, prototype and then print production parts, according to Carbon officials.
The M3 is designed for faster printing, a simpler print experience and a more consistent surface finish, according to the company. The M3 Max offers the same benefits as the M3 as well as a true 4K light engine that doubles the build volume with the same pixel size and density.
The M3 has a build volume of 7.4 inches by 4.6 inches by 12.8 inches, while the M3 Max has a build volume of 12 inches by 6.4 inches by 12.8 inches. The M3 Max’s 4K light engine means it can print at a resolution of 3,840 horizontal pixels by 2,160 vertical pixels, according to the company.
The larger build volume makes the M3 Max printer ideal for larger parts or producing many smaller parts with high quality.
Both printers can make use of a wide range of high-performance materials tailored for applications across industries including automotive, life sciences, dental, consumer products and industrial.
“With this next generation of industry-leading printers — combined with our Design Engine software and Carbon DLS materials — design teams across business verticals can create incredibly high-quality prototypes with end-use performance quicker and more efficiently than ever before,” DeSimone said. “And once the product development is complete, Carbon’s platform enables companies to move to production quickly and efficiently anywhere in the world. We believe this new generation of Carbon DLS technology will empower more collaboration and help to revolutionize how products are designed and made.”
Other key features of the new generation of printers include:
- Substantially lower forces on the part during printing and the introduction of closed-loop control of force and temperature, reducing failure modes that would require additional printing.
- The ability to create parts that prior generations of printers could not by unlocking more geometries with the next generation of DLS technology.
- Faster printing thanks to better heat management, which allows the printers to deliver more throughput per square foot in thermally limited scenarios. As an example, the company said the next generation of DLS printers has resulted in throughput improvements for dental models up to 2.5 times over the M2 printer. The speed improvement will vary depending on the geometry of a printed part and the material used for printing.
- The newest generation of DLS technology produces parts that are smoother than prior generations with early testing showing about a 1.4 micrometer reduction in surface.
- The new printing technology reduces the variation in parts across a single build by 50 percent, translating to less variation in general accuracy and more production repeatability in engineering resins.
“Manufacturers are looking for an integrated platform to support taking ideas to production much faster, while taking advantage of the greater design freedom not possible through traditional manufacturing methods,” Rob L’Heureux, director of product marketing, said during the press conference.
“Pushing the boundaries of additive manufacturing requires first a simpler print experience, and that means getting started printing the parts that you want to make faster,” he said. “So, whether you're trying new part geometries or trying to staff a production line, that simpler print experience can help reduce active labor time and the skill needed to deliver great parts.”
Carbon uses a subscription pricing model with its customers. It also recently announced that it would be making its Design Engine software available to all, not just users of its 3D printers.
Contact:
Carbon Inc., Redwood City, Calif., 650-285-6307, www.carbon3d.com
Bruce Geiselman
Senior Staff Reporter Bruce Geiselman covers extrusion, blow molding, additive manufacturing, automation and end markets including automotive and packaging. He also writes features, including In Other Words and Problem Solved, for Plastics Machinery & Manufacturing, Plastics Recycling and The Journal of Blow Molding. He has extensive experience in daily and magazine journalism.
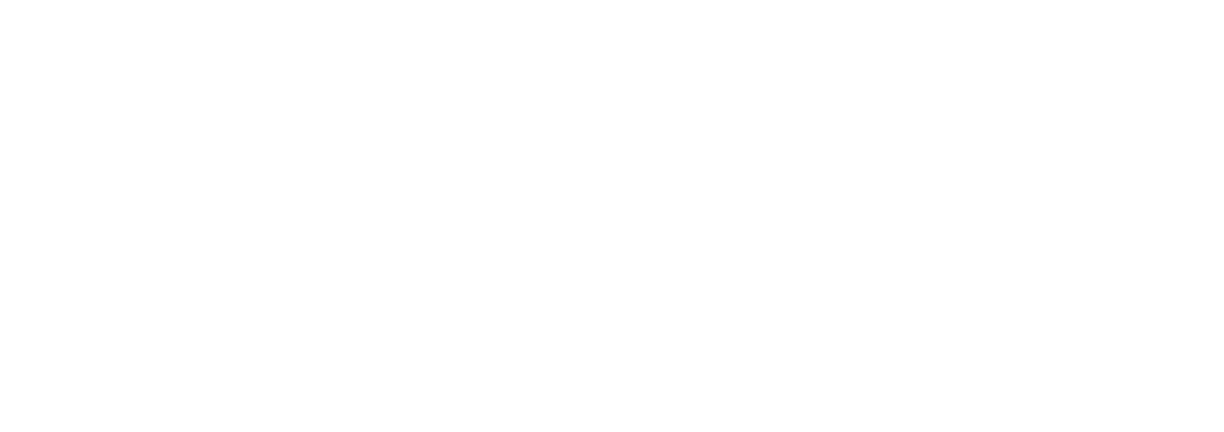