Robots put unattended operations within reach for mold makers
What you'll learn:
- Automation is transforming mold making as companies push toward lights-out manufacturing.
- Ongoing labor shortages are driving the need for automation, as finding and retaining skilled machinists and toolmakers is increasingly difficult, especially as older workers retire.
- Tougher tasks like pathing, fixturing and cutting strategy still require human expertise.
- Some companies are expanding beyond mold making to offer automation systems, in-mold labeling, service and repair work.
By Karen Hanna
At Decatur Mold Tool & Engineering Inc., a phrase familiar to the molding side of operations is entering the lexicon of the folks who make the tooling: Lights-out.
An industry so reliant on human expertise and human hands is undergoing a transformation, and Rhonda Lustenberger, majority owner and president of the mold making plant, wants to be part of it. Automation — long a solution for molders — is drawing attention upstream, as mold makers try to squeeze more profits from thin margins.
To improve its efficiency and offset challenges with finding labor, the North Vernon, Ind., shop is identifying opportunities for unmanned machining, along with strategizing ways to reduce setup, optimize fixturing approaches and standardize the tool library.
“We started last year a real drive for productivity and efficiency beyond anything we’ve ever tried before,” Lustenberger said.
As the company says in a January blog post, “In today's competitive manufacturing landscape, companies are continuously exploring ways to boost productivity, reduce costs and uphold rigorous quality standards. One of the most transformative strategies to achieve these objectives is Lights-Out Manufacturing.”
Filling in the gaps
Established in 1966, Decatur Mold takes no offense when its customers call it a shop of “control freaks.”
But those high-tolerance-minded employees are hard to find. It’s a dilemma facing both Lustenberger and her competitors across the industry.
“The thing that mold makers desperately need is a system to make it so that they can basically draw their mold, click a button, and the mold comes out the back. ... With the manufacturing labor shortage, it is very difficult to find skilled machinists and many of them are retiring, creating a knowledge gap,” said Rick Schultz, an aerospace program manager for automation provider FANUC America.
That’s a challenge at a lot of shops, including Decatur Mold, which is considering a formal training program for new engineers or high school grads. But newbies take years to level up, Lustenberger said.
Overall, the plant currently employs about 140 people, serving customers across an array of industries. Annual revenues stand at about $30 million. Lustenberger estimated that about one-quarter of the shop’s machinists, tool makers, designers and project managers are younger than 35, and many of them are still learning on the job.
“We are trying to train a new generation to replace a lot of these folks that have been here for 30, 40 years that are finally able to retire,” she said. “Training adds significant cost to our business that is not always offset by government grants or whatever. It’s a real balancing act that we’re facing right now, because our intent is to be here 50 years from now. I think some other shops are kind of winding down. But we are making that investment very heavily right now.”
Running unattended
The blog post on Decatur Mold's website highlights how the shop is navigating the labor challenges. It touts "a fully automated system featuring three advanced automation cells, ushering in a new era of efficiency and precision.”
Lustenberger acknowledged it’s still a work in progress, as employees learn which cutting paths and strategies work best for unattended machine time, but some jobs are taking place when no one’s around.
“We're having great success with that, with being able to get more unmanned time, through the weekend, through the night. We're trying to take some of those same concepts over on our service side and helping people understand what [cutting] paths make sense to run when no one's here, or what paths can you walk away from,” she said.
That’s been a work in progress.
“Our thought was that we could run through the Labor Day weekend, the three-day weekend, without anyone having to come in. That’s our goal. ... We’re not 100 percent there,” she said.
The process starts when the shop’s design department designs the mold and plots out the arrangement of electrodes, or trodes, that will shape it. A machinist then loads raw, uncut carbon blocks into a carousel. A technician programs the CNC mill’s trodes. After that, the machining cell’s robot takes over. It automatically loads and unloads the trodes into the CNC machine, then loads and unloads each trode as needed for EDM burning.
“The robots are the easiest part of the whole process,” Lustenberger said. “The hardest part is the fixturing, the pathing and then making sure we have good cutting techniques.”
To reduce the time needed to load workpieces, the shop uses the Wow Workholding pallet system from Rian Solutions, Brantford, Ontario, which places workpieces on a pallet, so the next part setup is teed up.
Setup — which Lustenberger estimated previously took 1.5 hours — is now down to 30 minutes.
Schultz said modern technologies streamline the process.
“Because of what’s happened in technology in general, industry and everybody’s daily life, you don’t want to buy a phone and spend three weeks getting it to work. ... When you buy a printer for your desk at home to print pictures, you don’t want to have to dial in settings. You want to buy a printer, plug it in and print stuff. The generation coming into the workforce, that is all they’ve done. ... They want to be able to draw their part and have the system set up such that basically they hit print and the mold comes out the back,” he said.
Decatur Mold’s process not only boosts productivity and saves time and labor for the company, it improves consistency, accuracy and repeatability, while maintaining tighter tolerances. With vision systems on each cell, quality control also is better. Among other advantages, the blog post says, “The modular nature of the automation cells allows Decatur Mold to adjust production levels according to demand without incurring significant reconfiguration costs.”
The technologies also offer new opportunities for career growth, and allow for more accurate job quotes to customers and prospective customers.
In addition, Lustenberger said, the Tech Center provides a physical demarcation between the shop’s new-mold manufacturing work and the repair services it offers.
Making space for both was important, she said.
“Service work is, I think, more of a market differentiator than new work, potentially, in that service work takes a different skill set that I think a lot of people don't have. The new-mold manufacturing can be more scientific. It's more predictable; if you have the right capital and the right people, you can do that. Service, you have to really nurture that talent be able to repair a mold, in my opinion. Our service work is about two-thirds of our total revenue.”
Automation catches on
Across the industry, the need for automation is becoming apparent.
Injection mold making shop Dynamic Tool Corp., for example has three automation cells, each with distinct machining processes, CMM validation and a rail-mounted robot. According to a statement provided by John Berg, director of marketing, and Greg Gierach, VP of sales, to Plastics Machinery & Manufacturing, the shop’s engineers and toolmakers designed and built each of the cells — a hard-cutter, sinker EDM and graphite machine station.
The Menomonee Falls, Wis., plant, is moving forward with Phase 4 of its automation project — upgrades to wire EDM operations.
“Dynamic has made significant investments in grouping, integrating, and automating machine processes with in-line inspection. ... We always seek to improve efficiency and capacity on our shop floor. Our expanded sampling and systems qualification capabilities have now created the need for additional investment considerations in expanding our usage of scanning technologies, additive manufacturing, ancillary equipment, and automated visual inspection,” Berg and Gierach wrote.
For StackTeck, Brampton, Ontario, other shops’ interest in such capabilities represented an opportunity — over the last few years, it’s branched out from its mold making roots to offer automation solutions.
The company has experienced growth, but finding people is difficult, said Mike Gould, who in June took over as the company’s CEO.
“A business like ours, one of our major challenges is finding qualified people to join the team. We all go through retirements and people moving and things like that. So, we're constantly onboarding new people. As a result, even this year, we've had over 27 new people come on board since Jan. 1 this year. That's over 10 percent of our workforce,” Gould said.
Just as Decatur Mold is turning to robots, so are StackTeck’s customers, he said. The company touts systems for applications including in-mold labeling and inspection.
“That’s been a challenge that a lot of our customers face, is finding skilled labor to do the task of owning and operating more advanced equipment, more complex equipment, and you’re looking for that higher-level individual. So, instead of doing repeated tasks, you’re now hiring and recruiting people to program and set up robots and automation,” Gould said.
“If you have a time-consuming, complicated process with limited resources, you might need to figure out more efficient processes,” Schultz said. FANUC's portfolio includes CNC and motion control systems, as well as five-axis machining centers.
Bright future
The science and art of mold making are evolving, but that doesn’t dim the expertise that’s involved. Instead, for Lustenberger, the technologies just promise more opportunities.
While going on autopilot remains a dream, at Decatur Mold, it's getting closer.
“I have optimism for our shop, because I feel that we have a kind of a rare combination of talent and capital that’s hard to find in the U.S.," Lustenberger said.
With the shop at about 80 percent capacity, she said she knows much more is possible.
The blog post looks beyond automation. It says, “Decatur Mold's Tech Center success with lights-out manufacturing is just one example of how automation is transforming the industry. As technology continues to evolve, it is likely that more manufacturers will adopt similar systems to boost productivity and reduce operational costs. The integration of artificial intelligence, machine learning, and next-generation robotics will only increase the potential of lights-out manufacturing, leading to even more autonomous and efficient production environments.”
“We’re always keeping our eyes open,” Lustenberger said. “I would anticipate that our next larger investment will be in software of some kind that will help us either in the design process or the pathing process or both. You’re starting to see AI really take hold in those areas. I feel like we’re on the edge of that. I’m not a first-in kind of business owner, but I don’t want to be far behind that.”
With one employee spending time actively scouting other technologies, Lustenberger indicated that the Tech Center isn’t the final word on her company’s investments.
“We’re not where we want to finish," Lustenberger said.
Contact:
FANUC America, Auburn Hills, Mich., 888-326-8287, www.fanucamerica.com
StackTeck Systems, Brampton, Ontario, 888-700-8555, https://stackteck.com
Karen Hanna | Senior Staff Reporter
Senior Staff Reporter Karen Hanna covers injection molding, molds and tooling, processors, workforce and other topics, and writes features including In Other Words and Problem Solved for Plastics Machinery & Manufacturing, Plastics Recycling and The Journal of Blow Molding. She has more than 15 years of experience in daily and magazine journalism.
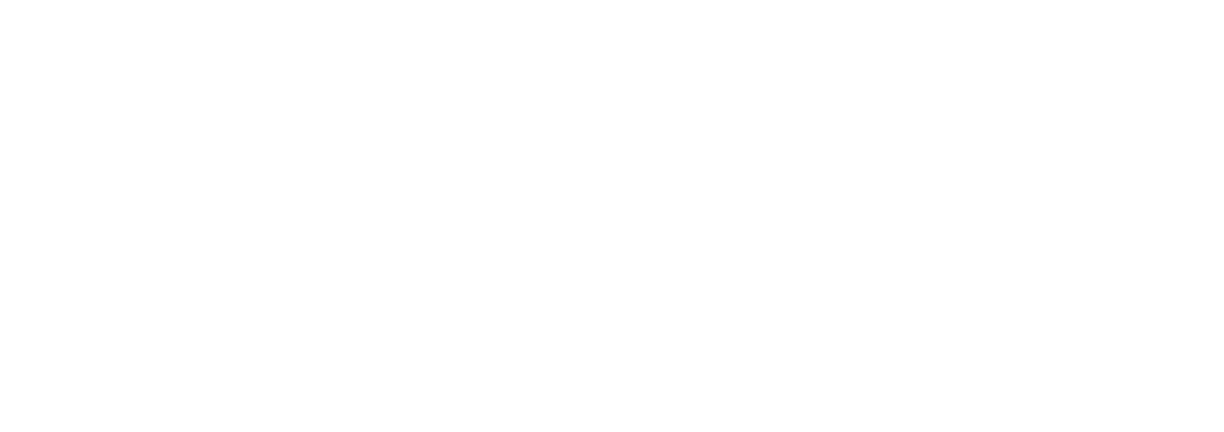