By Bruce Geiselman
Blenders, feeders, dryers, conveyors, temperature control units and other auxiliary equipment increasingly can analyze process data, issue alerts, automatically make process adjustments and predict when maintenance should be done.
Some manufacturers say the COVID-19 pandemic and skilled labor shortage have fueled interest in smart auxiliary equipment, but costs for such equipment remain a challenge for smaller manufacturers. Other equipment manufacturers say the demand for smart equipment existed long before the pandemic.
“It all comes down to a skilled workforce and the fact it's hard to find and retain skilled employees,” said Douglas Brownfield, commercial director of LIAD Smart, a business unit within Ampacet Corp. “That shortage of skilled employees is prohibiting companies from growing.”
Q&A with Conair: Smart auxiliaries help bridge skills gap.
To support his argument that interest in smart technology is growing, Brownfield pointed to the eighth annual “State of Smart Manufacturing Report” by Rockwell Automation, which identifies trends based on a survey of 1,353 manufacturers.
Among the report’s findings:
- Manufacturers citied concerns about a lack of a skilled workforce as the No. 1 reason they can’t outpace the competition.
- 97 percent of participants reported plans to use smart manufacturing technology.
- 45 percent of respondents said a push for higher quality is creating the need to accelerate digital transformation within their organizations.
People have different definitions of smart auxiliary equipment, but Brownfield said smart auxiliary equipment increasingly can learn and make adjustments in real time. The result can be the correction of problems, like color variations, before they hurt quality.
“That’s the ultimate in smart equipment, as well as smart auxiliary equipment,” Brownfield said. “It all plays a role in this whole smart factory of the future, which they refer to as lights-out automation or a lights-out factory.”
While most manufacturers today lack the funding to implement total automation, it may become more common in the future.
“I can’t say that everyone’s got the capital to invest in a total lights-out plant today, but companies are talking about it; they’re starting to make minor investments,” Brownfield said. “It’s happening. It’s just going to take time.”
Historically, when processors considered automation, they thought of installing robots and automating primary processing equipment. However, processors are increasingly thinking about automation of auxiliary equipment including cooling and temperature control units, said Al Fosco, marketing manager for Frigel North America.
The latest technologies monitor not only core processes, such as injection molding and extrusion, but also the critical parameters that affect auxiliary equipment, such as conveyors, dryers and blenders, said Gene Flockerzi, GM of Moretto North America.
Smart auxiliary equipment goes beyond the equipment’s essential functions, for example conveying material to the right location, to offer automation that decreases the need for human intervention, said Piovan UnaDyn President William Goldfarb.
Representatives of several of the world’s largest auxiliary equipment manufacturers recently spoke with Plastics Machinery & Manufacturing about the growing trend of smart auxiliaries.
Wittmann: Communication is key
“We are seeing a push for smart auxiliary equipment, more of a push for OPC-UA communication protocols between our auxiliary equipment and a customer's molding machine and then to their MES [manufacturing execution system],” said Steve Mussman, division manager for Wittmann’s material handling and auxiliary equipment.
One of the reasons customers want a standard communications language for their various pieces of equipment and their MES is to enable material traceability through information gained from machine controllers, Mussman said. Communication between equipment and the MES also aids in diagnosing malfunctions and predicting future equipment failures, which decreases unplanned downtime.
Mussman outlined three characteristics that he said encompass smart auxiliary equipment: inclusion of a touch screen that gives operators more intuitive operation than more manual controls, the incorporation of sensors on auxiliary equipment and the ability to communicate information about equipment operation to an MES or process monitoring software.
The future for smart auxiliary equipment will be “full-on predictive maintenance,” Mussman said. Right now, smart technology offers health indicators, which can serve as a warning or an alert to a machine operator that something appears to be wrong with a process. For example, if the pump pressure on a temperature control unit is operating outside expected parameters, the operator might receive an alert or warning that something is wrong with the TCU, the mold, or somewhere in between. However, the operator might not know exactly where the problem lies.
In the future, smart technology could evolve to the point where operators can learn exactly where the problem has arisen, Mussman said.
“This is why being able to gather different pieces of information from a work cell across an OPC communication protocol, we can start to look at different points of information and really start to fine-tune where that issue may be,” Mussman said.
Wittmann auxiliary equipment is available with basic or plus control offerings. The plus models feature touchscreen HMIs and are compatible with the OPC-UA communication protocol, Mussman said. The plus models also are Wittmann 4.0 compatible. Wittmann 4.0 is smart factory technology that connects all equipment in a work cell and enables process and production data exchanges.
Wittmann’s customers frequently rely on the company’s smart blenders to keep track of material inventory, Mussman said.
“A lot of our customers will use our blenders and they’ll use an OPC-UA protocol to output the consumption data to their ERP [enterprise resource planning] system to know when they need to reorder material,” Mussman said. “Since our blenders are known for being very accurate, they can rely solely on the blender to plan their material reordering.”
Ampacet: Controlling color
Ampacet, long known for its global masterbatch and additives business, has been a supplier of smart feeders and blenders since its 2019 purchase of LIAD, an equipment manufacturer based in Israel.
As an example of LIAD’s existing smart technology, Brownfield pointed to the company’s ColorSave 1000 gravimetric feeder, which can be controlled by an employee anywhere with internet access.
“What’s unique about the cloud-based concept is that you can monitor the performance of the feeders and make changes to the feeders remotely,” Brownfield said.
The machines also have a self-cleaning function in which a vacuum pulls all the colorant out of the feeder, enabling remote color changes without on-site labor intervention.
At NPE, LIAD will unveil its SpectroMetric 6.0 automatic color correction system, an upgraded version of its SpectroMetric color management system.
SpectroMetric combines a color measurement sensor with Ampacet LIAD’s color feeder technology. It can detect color variations and, if it detects problems, issue alerts that require operators to take corrective action.
The newest SpectroMetric version, an inline color correction system, automates the correction process and eliminates the need for human interaction. It feeds a customer’s base color masterbatch at the desired letdown ratio and then adjusts the color using five Flux mono pigments, rather than an earlier method that relied on adjusting the amount of masterbatch. The new system should be of particular interest to companies using post-consumer recycled (PCR) content, Brownfield said. Maintaining a consistent color using PCR can be challenging.
Instead of utilizing one masterbatch to correct a color, you'll be able to incorporate multiple pigments, Brownfield said. It will reduce the amount of color required and thus reduce costs, he said. The corrections will be accomplished automatically without operator involvement.
Also at NPE, Ampacet will launch its new BlendSave Compact technology, a smaller, more compact version of the company’s BlendSave automated resin blending and management system.
BlendSave is a centralized batch blending system that allows a plastics processor to blend formulations for multiple machines and recipes. For example, if a company has 10 injection molding machines or 10 extruders and each machine is running a different formulation, the BlendSave system, which is fully computerized and automated, can deliver a unique formulation of resins and additives to each machine.
“It will weigh each ingredient, create a batch, deliver it to that machine, mix it and drop it right into the throat of the extruder,” Brownfield said. “The operation can be run via an iPad.”
The computerized system allows for easy tracking of raw materials and consumption, he said.
Both the BlendSave and new BlendSave Compact can blend up to 40 raw materials. The BlendSave can serve up to 50 machines. The compact version can serve up to 10 machines. The original BlendSave requires floor space of 16 feet by 16 feet, while the compact version requires only 6 feet by 6 feet. The required ceiling height for the original version is 21-30 feet, while the required ceiling height for the compact version is only 17 feet.
“We found that a lot of plants don’t have high ceiling heights,” Brownfield said. “The new compact version will be easier to fit in existing facilities. The large BlendSave is nice if you’re going to build a new plant because you can build the ceiling height accordingly.”
The BlendSave Compact will be available immediately after NPE, and a full system will be on display at the company’s booth. The SpectroMatic 6.0 will be available commercially about three to four months after the show, Brownfield said.
Frigel: Keep the ‘lifeblood’ circulating
Frigel, a manufacturer of cooling and temperature control systems, is placing an emphasis on advanced and remote monitoring of its equipment.
“Temperature control and cooling systems in general are the lifeblood of injection molding, extrusion and blow molding,” Fosco said. “Quite often, those pieces are in central systems. For example, they're often in a utility room or outside, and out of sight, out of mind.”
It’s important for processors to be able to monitor what's going on with the cooling system and troubleshoot it remotely, whether it's from a PC, an iPhone or a tablet, Fosco said. If an alarm goes off, processors need to be able to access those alarms remotely. In addition, Frigel’s service technicians can diagnose and correct problems via remote monitoring.
“People are just now getting into this Industry 4.0 IoT thing,” Fosco said. “They are getting more and more interested because of labor shortages, etc., and automating plants as much as they can. That interest is perking a little bit compared to years ago.”
The company will display Industry 4.0 solutions at NPE. Its 3PR 4.0 control platform provides complete monitoring and control of the company’s central cooling systems, Ecodry adiabatic coolers, central chillers, and pumping and filtration systems. Its MiND [Machine iNteractive Database] system collects information from 3PR-connected equipment and combines it with information from machine-side components, including portable chillers and temperature control units. MiND then allows for management of all Frigel auxiliary equipment in a plant.
MiND provides real-time information locally or remotely with access through a web browser. No additional apps are necessary, and the system is compatible with all operating systems, including Windows, Mac, Android and Linux.
MiND is cloud-based, but all its data is stored locally inside the MiND PC at the customer’s site, Fosco said. The system includes a heavy-duty industrial PC. The updated MiND system at NPE will include two hard drives for backup purposes. The latest version of the 3PR system has new internet capabilities that, when combined with MiND, allow for remote monitoring of machine-side equipment.
“The 3PR 4.0 is new,” Fosco said. “The 4.0 now has new internet capabilities that it did not have before.”
Moretto: Automatic adjustments
Comprehensive monitoring capability of auxiliary equipment ensures automatic adjustments in throughput, temperature, material flow and mold temperature controls, among other variables, thereby enhancing production efficiency and product quality, Flockerzi said.
Real-time monitoring and automatic adjustment of operational parameters to maintain predefined settings ensures optimal performance of each piece of equipment without requiring direct feedback from primary processing units, he said. Autonomous adjustments are crucial for maintaining consistent processing conditions, a cornerstone for achieving uniform material quality at the extruder or injection molding machine's throat.
Moretto dryers are equipped with variable frequency drive (VFD) technology and precise temperature monitoring, and dynamically adjust to meet specific processing conditions. This prevents material overprocessing or underprocessing.
Moretto incorporates smart technology into its range of dryers, which can handle between 0.5 pound and 20,000 pounds per hour. In offering smart technology in smaller dryers, the company provides a feature not commonly available from its competitors. That ability stems from Moretto’s in-house manufacturing capabilities, according to the company. Moretto manufactures nearly every component of its auxiliary equipment, including fans and blowers. The approach allows Moretto to offer competitively priced, feature-rich products, Flockerzi said.
Moretto's conveying systems and blenders also use smart technology, ensuring optimal material velocity to prevent degradation and ensure precise material mixing ratios.
Moretto's MOWIS plant monitoring and management system offers plastics processors an integrated platform for real-time control and comprehensive data visualization. The system assists with data-driven decision-making and satisfies plastics processors’ growing demands for traceability and detailed production documentation.
ACS Group: Data-driven decision-making
“Smart refers to data — equipment cannot be smart without effective data capture, specifically data that’s useful to the manufacturing facility for making daily real-time decisions,” said Mark Johansen, VP of marketing for ACS Group, which is the parent company for the AEC, Cumberland, Sterling and MiVue brands.
“The data in and of itself does not make your equipment smart; you have to have that foundation. But then the IoT solution, and for ACS that’s MiVue, needs to use that data to facilitate those decisions,” he said. “It provides the ability to foresee and avoid expensive situations such as [unexpected] downtime or poor quality or excess material usage that would increase costs. It allows the factory to make adjustments before those have a significant adverse impact on the factory.”
MiVue technology collects data from auxiliary equipment. Using cellular technology, the encrypted data is sent to and secured in the cloud with Microsoft Azure. Using MiVue software on any web-enabled device, those with authorization can see the data and receive text and email alerts whenever a piece of equipment begins operating outside of specified parameters. The MiVue system also can monitor injection molding machines and extruders.
Because MiVue uses cellular technology to connect to the internet, there are no security concerns about connecting to a user’s computer network. In addition, it is basically plug-and-play technology that does not require extensive involvement of an IT staff, according to the company.
In addition to its process monitoring and predictive maintenance features, MiVue is a great tool for conducting a postmortem on any type of unplanned downtime, Johansen said. It allows plastics processors to look at what was happening with a particular piece of equipment in the days, hours and minutes leading up to a malfunction.
The plastics industry in North America has been slow in adopting smart technologies, but once plastics processors experience the benefits of MiVue on one or two pieces of equipment, they typically want to expand its use, Johansen said. Those benefits include higher productivity, higher quality and lower costs, he said.
In the future, MiVue and other IoT software could be used to seamlessly integrate with a factory’s MES. Ultimately, IoT solutions are going to be able to manage inventories and replenish raw materials, he said.
Piovan UnaDyn: Recipes for success
Easylink+, the latest version of Piovan UnaDyn’s automated coupling station, automatically delivers the right resins and additives to the correct machine, which decreases the need for worker involvement, Goldfarb said.
Easylink+ features include a purging port. After every conveying cycle, the system can automatically purge its line through a filtered inlet port to ensure that no materials remain in the conveying system.
A recipe for a specific order could be loaded from a company’s enterprise system into the Easylink+ system, which then automatically routes the right materials from drying hoppers to a processing machine in the right quantities. When combined with Piovan’s WinFactory 4.0 supervisory software, Easylink+ can ensure materials have been properly processed before they are delivered, Goldfarb said. Winfactory 4.0 supervisory software monitors a variety of equipment, including dryers, loaders and blenders, each of which has its own controller.
The Easylink+ coupling unit eliminates the need for users to manually enter each recipe and perform manual hose changes. Easylink+ and WinFactory 4.0 can track materials every step along the way. By scanning bar codes prior to conveying, users ensure that material goes to the proper destination, Goldfarb said.
The Easylink+ automatic coupling station can manage up to 60 inlets and 60 outlets with pipe sizes from 40mm to 76mm.
Piovan Unadyn also offers a less-expensive and less-automated option called Handilink+, which uses manually connected flex hoses to a connection tree. Although manual, the system allows the same level of proofing, Goldfarb said. Handilink+ uses “smart” quick-change fittings.
“ 'Smart’ means the proper source is illuminated, directing the user to make the connection,” he said. “When they put the fitting on, [Handilink+] understands whether it is the right connection or not. ... The Handilink is similar to the Easylink but done in a manual fashion.”
Handilink+ also works with WinFactory 4.0, which validates each connection. If a mistake occurs, conveying will be halted, and an alarm will be triggered.
In the future, as smart technology becomes more prevalent, it should become easier for users to install without the involvement of IT specialists, Goldfarb said.
Dri-Air: Info at your fingertips
Dri-Air Industries offers SmartTouch controls for its resin dryers. The controls display trending information for temperatures and dew points and can communicate with connected molding machines.
The SmartTouch technology also can communicate with SCADA (Supervisory Control and Data Acquisition) systems that monitor, control and analyze industrial processes and devices, Sears said.
Contact:
ACS Group, New Berlin, Wis., 262-641-8600, www.acscorporate.com, (NPE Booth W3921)
Ampacet Corp., Tarrytown, N.Y., 914-631-6600, www.ampacet.com, (NPE Booth S22097)
Dri-Air Industries Inc., East Windsor, Conn., 860-627-5110, www.dri-air.com, (NPE Booth W909)
Frigel North America Inc., East Dundee, Ill., 847-540-0160, www.frigel.com (NPE Booths W3989 and W4089)
Moretto USA LLC, Jackson Center, Pa., 724-269-7600, www.moretto.com/en/ (NPE Booth W1743)
Piovan UnaDyn, Fredericksburg, Va., 703-490-7000, www.piovan.com/una-dyn/ (NPE Booth 2729)
Wittmann Group, Torrington, Conn., 860-496-9603, www.wittmann-group.com/en/usa (NPE Booth W3043)
Bruce Geiselman
Senior Staff Reporter Bruce Geiselman covers extrusion, blow molding, additive manufacturing, automation and end markets including automotive and packaging. He also writes features, including In Other Words and Problem Solved, for Plastics Machinery & Manufacturing, Plastics Recycling and The Journal of Blow Molding. He has extensive experience in daily and magazine journalism.
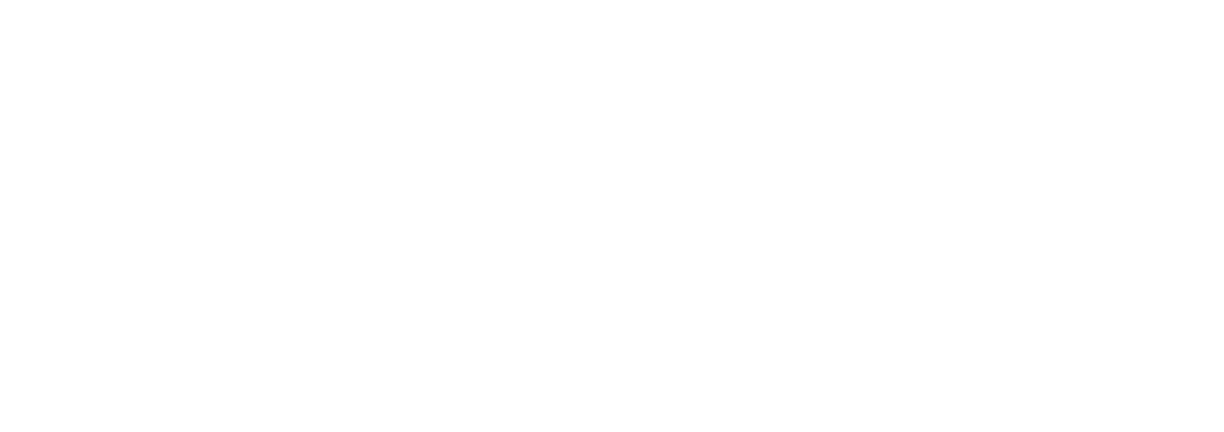