Piovan SpA, Santa Maria di Sala, Italy, has added features to its Winfactory 4.0 management and process-control software and released new versions of it to meet the needs of specific types of plastics manufacturers.
"We have added many, many features to the software," said Giorgio Santella, corporate VP of service and sales in North America. "Today, Winfactory 4.0 has developed into preconfigured versions."
In addition to the software's basic supervisory package, Piovan now offers versions designed for:• PET preform and bottle producers,• medical equipment and component producers,• automotive market manufacturers,• film manufacturers,• sheet manufacturers• and pipe manufacturers.
"Each of these Winfactory 4.0 [versions] has specific configurations built into it," Santella said. "Each has a unique display and interface between user and system. The configuration is designed for the specific user's environment. A solution for a PET preform and bottle customer is different from a solution for a pipe, profile and cable customer."
In addition to the new configurations, Piovan has released energy-management software that works with all versions of Winfactory 4.0. The energy-management software can calculate the energy costs for producing each part and operating each piece of machinery, as well as determine which parts are most profitable.
"It's very, very important information for the producer to help them understand their profits," Santella said.
Since it was unveiled in late 2016, Piovan reports its Winfactory 4.0 software has been installed at about 200 locations. It is used in all areas of plastics manufacturing, including injection molding, extrusion and thermoforming.
Piovan developed Winfactory 4.0 to help the plastics industry transition from a traditional factory setup to one in which computers and automation provide comprehensive control and monitoring. This fills the needs of some manufacturers who have equipment — some of it purchased recently — that is not Industry 4.0-compliant.
"What happens is that the machinery they buy tomorrow will be Industry 4.0-compliant and it will not have any capability of communicating with the non-Industry 4.0-compliant equipment and machinery," Santella said. "So, I may end up with a manufacturing plant where the legacy equipment is left on the side, silent and not capable of communicating anything, and the new equipment will be the only equipment with the capabilities of exchanging data and optimizing my production means."
Winfactory 4.0 bridges the communications barrier between new and old equipment.
"When we say old, it sounds like equipment that was purchased and installed 20 years ago. It sounds like that, right? From the Industry 4.0 standpoint, old equipment is all equipment that is not Industry 4.0-compliant. So, it might be a week old. If you buy a new machine that is not Industry 4.0-compliant, that machine, from the perspective of Industry 4.0, is an old machine. It's a machine with which Industry 4.0-compliant equipment cannot exchange data. It cannot communicate."
Industry 4.0, a concept born in Germany, relies on Open Platform Communications-Unified Architecture (OPC-UA) as the protocol for machines and equipment to communicate and share data. However, older machines use different communications protocols for conveying information and that stymies efforts to share information among various pieces of equipment and optimize efficiency. Winfactory 4.0 can interpret the different communications protocols and instantly share the information with various pieces of equipment.
Piovan realizes Winfactory 4.0 does not represent Industry 4.0 in full. Instead, it is a bridge that will allow companies to transition to Industry 4.0.
"Winfactory 4.0 is not the future of Piovan in the Industry 4.0 environment," Santella said. "It is the passage. It is the bridge between current conditions and the future. The future will be all equipment and machinery with communication capabilities through OPC-UA. In the future — far or near, we don't know —the dryer will speak with the injection molding machine, and the blender will speak with the extruder because both will have in their controls a unified communication protocol, which is OPC-UA, but not yet."
Winfactory 4.0 uses a combination of software and hardware to exchange data among machines and equipment that allows one machine to see how another machine is working and coordinate operations for efficiency. The system can improve production efficiency and energy use. The information not only is collected and shared locally, but it can be uploaded to the cloud and shared globally with a plastics processor's other operating sites.
When an order comes in for a new part to produce, the software can analyze data from plants and production lines around the world and decide which production line is best equipped to handle the new order efficiently and at the lowest cost. Winfactory 4.0 also can help determine when pieces of equipment need maintenance.
"If your plant has 100 injection molding machines, it can be complex to manage maintenance without the help of a system to assist the production manager handling this," Santella said.
Winfactory 4.0 also can connect with a plant's manufacturing resource planning (MRP) and enterprise-resource planning (ERP) software to help manage production, purchasing and procurement of parts and materials. Working together, the software not only can assign an order to the best-suited production line, but also can consider complex solutions such as splitting an order between two or more production lines, possibly in two or more locations. The combined software also can determine how long it will take to fulfill an order and how much material will be required.
Winfactory 4.0 can connect equipment using only cables, as well as Wi-Fi for equipment that cannot be reached using cables, according to Piovan.
Piovan will demonstrate Winfactory 4.0 at NPE2018 from May 7 to May 11 in Orlando, Fla. The software will be used with operating machines to show how it can be integrated with Piovan equipment and equipment from other manufacturers.
Winfactory 4.0 is sold in the U.S. by Universal Dynamics, the U.S. arm of Piovan.
Bruce Geiselman, senior staff reporter
Contact:
Universal Dynamics Inc.Woodbridge, Va., 703-490-7000, http://unadyn.piovan.com
Bruce Geiselman
Senior Staff Reporter Bruce Geiselman covers extrusion, blow molding, additive manufacturing, automation and end markets including automotive and packaging. He also writes features, including In Other Words and Problem Solved, for Plastics Machinery & Manufacturing, Plastics Recycling and The Journal of Blow Molding. He has extensive experience in daily and magazine journalism.
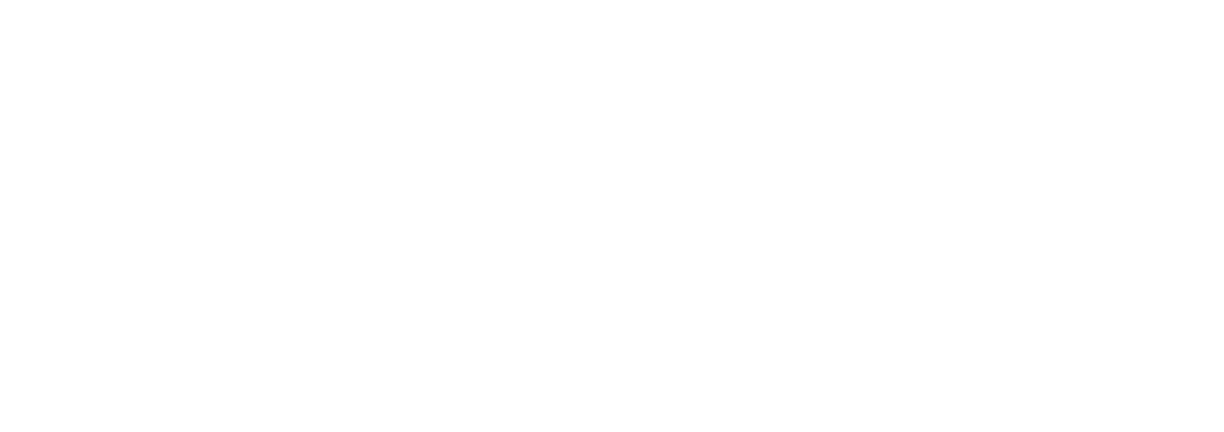