Precision, ease of use give 3D printer users freedom of design
By Karen Hanna
Producing tooling to test out new designs for the bats Chicago-based Wilson Sporting Goods Co. makes is expensive and time-consuming. Relying on an asset — skilled labor — that many manufacturers are finding hard to fill, the process is a crimp on development of equipment for summer’s pastime.
To address these issues, over about the last 18 months, Wilson Sporting Goods’ DeMarini brand has been 3D printing thermoset tooling for the prototypes it wants to test — a Nexa3D process called Freeform Injection Molding. Along with fast turnarounds, easy access and plug-and-play capabilities, 3D printing’s freedom of design is allowing manufacturers like Mason to see ideas take shape more quickly and at lower cost than ever before.
Since adopting Nexa3D's brand-new Xip Pro technology — an evolution over earlier Digital Light Processing (DLP) printers — DeMarini has refined its process.
Experts say that, whether the end goal is bats or tools that take a swing at more serious issues, like disease, 3D printing’s potential to condense the design and manufacturing process to the touch of a button is game-changing.
“Anyone with a laptop and access to the requisite software will be able to design products, send those designs to a printer and create their own prototypes,” said Phil DeSimone, a member of the CEO's office and co-founder at Carbon. “Good ideas will come from anyone, anywhere and can be turned into viable products that might help curb climate change, or solve medical problems.”
Unlike manufacturers interested in full-scale 3D printing production, Mason has different expectations for the 3D printers he uses: “The whole point of additive is to simplify the workflow; it’s not to get a part.”
In pursuit of bats suitable for young players at the Little League though college levels, Mason is focused on design.
The prototyping process using Nexa3D's Xip Pro technology centers on the polymer end caps and knobs of the bats, but Mason provided no specifics about the materials, simply calling them “advanced materials." He said the company uses conventional plastic injection molding machines (IMMs) to process thermoplastic parts.
Related: See innovative parts produced using 3D printing technology
The injection molded knobs and end caps can affect the swing, but even something as seemingly trivial as color can affect how materials in the bat are processed — and whether the end product is a hit or a miss.
“Ideally, what we would do is hit all the ideas, test them all quickly, and then really be informed by that. Not just what we think is the best idea or we’re looking at the past. Let’s just test the future. Let’s open up the floodgates, so all the ideas can happen,” Mason said during a Nexa3D webinar promoting the Xip Pro.
But waiting — and paying — for all the tooling to try out every idea presents huge challenges.
To get the results it’s seeking, Wilson Sporting Goods has to overcome a lot of roadblocks.
“There’s these people that are standing in the way of creativity because they have to vet the ideas, to say this is worth spending time and money on,” Mason said.
3D comes up clutch
“The conventional cost model misses five additional cost elements associated with injection molding: tooling amortization, prototyping/tooling change, design for injection molding, set-up fees and minimum order quantity (MOQ) inventory waste,” DeSimone said.
With the proliferation of 3D printing technologies, manufacturers have new options to take those costs out of the equation. As Francois Minec, global head of 3D polymers for HP’s Personalization and 3D Printing business, puts it, 3D printing is “providing innovative solutions to old manufacturing challenges.”
“We’re finding people are rethinking their whole design and production philosophy as an opportunity to be more robust and more flexible using additive manufacturing,” said Brent Stucker, an independent consultant who co-authored a textbook on the subject called “Additive Manufacturing Technologies.”
Manufacturers will increasingly find ways to integrate 3D printing into their processes, experts predict. Together, traditional manufacturing and 3D printing can be complementary.
Leveling the playing field
For Wilson Sporting Goods, Nexa3D’s new Xip Pro technology has provided a work-around to avoid costs and logistical challenges.
Having almost immediate access to new, one-off tooling — and being able to run it on the same IMMs the company uses to make production parts — means there’s no difference in the processes prototypes undergo, or how they’ll perform.
Once it’s run through an IMM, a Freeform mold can be dissolved away from the resulting part using either Nexa3D’s Desktop or Industrial Demolding Station — the equipment that Wilson Sporting Goods uses.
“We typically print six-10 molds before molding the next round of prototype parts because the molds are single-use, and it’s important to have a few different cycles on the molding machine to make sure we capture more data on the molding process.” Mason said.
The company can even iterate ways of designing the mold, placing mold gates in various places, for example, to see how a part would be affected, and to get a sense of how the metal-mold-design process will go.
In the end, the molds are sacrificed. But part integrity isn’t.
“Everybody would say, ‘Why would you make a mold that makes one part? That’s crazy,’ ” Mason said. “But when you can do it for $100, all of a sudden, it’s not crazy.”
Because the company 3D prints the molds, Wilson Sporting Goods doesn’t have to rely on mold makers at each step of the way to consider painstaking issues such as where to put parting lines, or how to handle cooling or undercuts. Relegating those concerns to later in the process saves time and money from being invested in prototypes that might strike out, anyway.
Instead of designing for manufacturing, Mason said the company’s now free to manufacture for design.
“We’re not replacing a metal mold. That’s never going to happen at scale because the cost of the additive technology with a sacrificial tool is just too high,” he explained. “But what we’re doing is we’re informing ourselves about not only does the part work — that’s what additive is focused on, a new part — but I’m also prototyping the process I will be using. In the injection molding world, you can’t separate the part from the process that creates it; they're intertwined, so in this case, I can actually build my prototype using the same system I would use in production.”
He added, “What I really I like about additive is it can change the workflow just as much as you can change the geometry.”
Driving out complexity
With 3D printers, manufacturers can make parts once thought too tricky for mass production — and they can do so sometimes without coaching by outside experts.
“Complexity comes at a nearly free cost for additive manufacturing, meaning you could produce a five-sided box and it would cost the same amount as if you added undercuts to that, or maybe some complex lattice structures and things like that, that are either difficult or impossible to mold, and it can take the same amount of time, as well,” said Lewis Simms, Nexa3D’s head of industrial product marketing.
That opens possibilities for bringing to market all kinds of parts that previously could exist only as ideas. It also offers new financial and logistical benefits.
“Often, we see 50 percent weight/material savings, two or three parts consolidated to one, or completely new concept design (such as a 3D lattice). There are also benefits such as no draft angle (saves 5 percent [of] material), no flash lines, no tolerance stacks on consolidated parts, etc.,” said James Reeves in submitted written responses about the new beta version of the VX1000 HSS 3D printer from Voxeljet, where he’s global director of polymer sintering.
The significance of being able to take on complexity will only grow, Mason predicted in an email elaborating on how his company is using its 3D printers.
“With additive tooling, the design complexity only has a minor impact on design and build time — generally, complex geometry is at the same cost/mold insert as simple geometry. A lattice is a great example of an incredibly complex (or ‘impossible’) shape that would require massive design and build efforts while the printed version is extremely easy. In my experience over the last 30 years as machines and software have improved, we are not making simple parts faster; we are making much more complex parts using the same resources that require even more experts to participate.
“I don’t see a future that is less complex than the present,” Mason wrote.
Freedom in 3D
To meet the challenge, the OEMs of additive manufacturing (AM) technologies tout their accuracy and the high-quality performance characteristics of the parts they produce. EOS’ Fabian Krauss, head of the company’s polymer systems, for example, gave a description that highlighted the versatility of its printers.
Size is no longer a limiting factor, he said. According to him, all but 5 percent of applications involve parts that fit into the build frames of EOS printers.
“We have a variety of printers — small, medium, large, more flexible, more automated — and most or all of these machines can make anything,” he said.
EOS printers have accuracies to within 30 microns — “that’s something 3D printing was incapable of doing, but that’s something injection molding can do,” Krauss said.
The ExAM 255 can process almost all injection molding pellets and achieves accuracies to within 25 microns. In addition, the parts it produces exhibit good tensile strength, the release says. “Another significant advantage is the ‘one-shot technology’: a component is created successively without any assembly.“
Like other makers of 3D printers, Arburg touts its AM technologies’ appropriateness for producing hard-to-make parts. In a press release, it says it recently released its largest AM machine, the Freeformer 750-3X “is also the right solution for complex geometries, integrated functions and work in clean rooms.”
Among other applications, the machine has proved a fit for making flexible connecting hoses for car cooling systems from TPU that exhibit impermeability, resilience and the appropriate black color, said Victor Roman, managing director of Arburgadditive.
Meanwhile, DeSimone said Carbon’s digital light-synthesis technology offers “agile part production” and “is particularly useful for complex geometries, differentiated functional performance” and consolidating parts.
Among other benefits, Carbon’s 3D printers boast the ability to consolidate parts or produce impossible-to-mold geometries, such as intricate channels, holes and recesses. Manufacturers also can use them to make tunable lattices, textures or foam replacement.
The technologies “can collapse the production process to two to three weeks with much lower variability compared to the six to 23 weeks typical with injection molding development time,” DeSimone said.
In baseball, a speedy runner who wants a faster route around the diamond can challenge the pitcher and catcher by attempting to steal the next base.
With 3D printers, Mason is taking a slightly different route — but it’s paying off, as R&D time has been slashed by a factor of between four and six, he estimates.
Mason says the ability to quickly and efficiently produce tooling for prototyping has proved transformational.
“You can really jump forward from just part design to molded parts,” he said.
Being able to make molds in-house that can make prototypes with the exact performance characteristics later large-volume production runs would produce has him looking at molds differently.
Thanks to 3D printers, the design and prototyping process could change for a lot of manufacturers, 3D printing experts say.
“Every single customer I have, if you ask them, ‘Do you want the mold?’ they would say no,” Mason said. “They want the part that comes out of the mold. That’s what they care about. The mold is just a necessary evil.”
Mold makers won’t be an easy out, though. Competition could help them, too, EOS’ Krauss said.
“I actually believe that just as there is very much activities going on in 3D printing, there [are] huge activities going on in moldmaking. The injection molding industry won’t just say, ‘Well, then you take the market;’ they will fight back and say, ‘Then, we’ll improve the moldmaking,” Krauss said.
Whether moldmaking makes a comeback in his department isn’t Mason’s biggest focus.
Instead, he’s getting a handle on how bats produced by Wilson Sporting Goods are going to perform when their hitters take the field.
“This is a win for everybody. It’s better for me as an R&D designer, better for our manufacturing team. It’s better for our customers, being less expensive, faster, and really with much, much larger build capacity in our legacy DLP system,” he said during the Nexa3D webinar. “There is really an untapped potential here that we’re unlocking.”
Karen Hanna, senior staff reporter
Contact:
3DX Consulting LLC, Park City, Utah, 435-363-5197, brent.stucker@outlook.com
AIM3D, Rostock, Germany, 49-381-367-66090, www.aim3d.de
Arburg Inc., Rocky Hill, Conn., 860-667-6500, www.arburg.com
Carbon Inc., Redwood City, Calif., 650-285-6307, www.carbon3d.com
EOS, Pflugerville, Texas, 512-388-7916; Novi, Mich., 248-306-0143, www.eos.info/en
Formlabs Inc., Somerville, Mass., 617-702-8476, www.formlabs.com
HP Inc., Palo Alto, Calif., 650-857-1501, www.hp.com
Nexa3D, Ventura, Calif., 800-797-0633, www.nexa3d.com
Voxeljet America Inc., Canton, Mich., 734-808-0025, www.voxeljet.com
Karen Hanna | Senior Staff Reporter
Senior Staff Reporter Karen Hanna covers injection molding, molds and tooling, processors, workforce and other topics, and writes features including In Other Words and Problem Solved for Plastics Machinery & Manufacturing, Plastics Recycling and The Journal of Blow Molding. She has more than 15 years of experience in daily and magazine journalism.
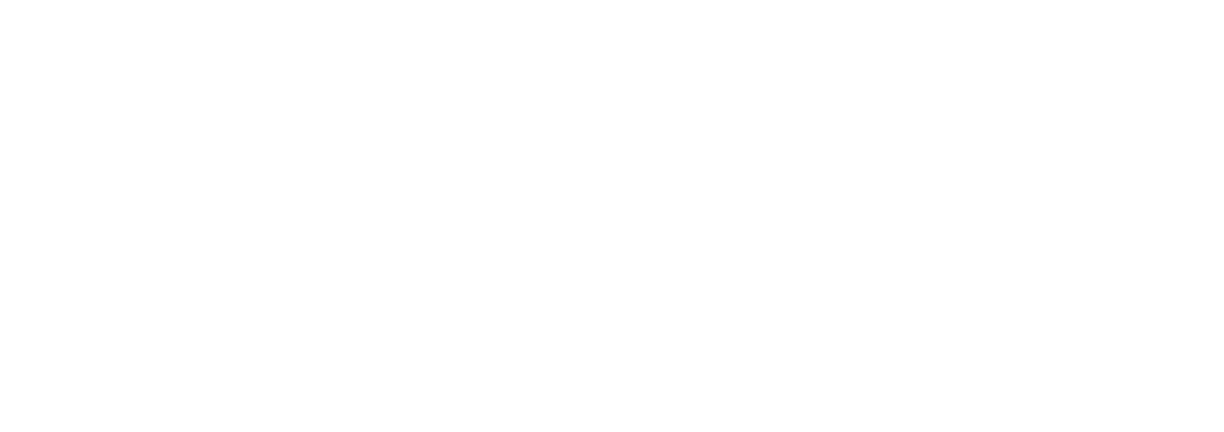