Hybrid manufacturing approach breaks down barriers for 'Bionic Kids'
By Karen Hanna
For a girl born with a partially developed right arm, meeting a dolphin with a silicone and plastic prosthetic tail had all the makings of an amazing experience.
But it was the moment she reached her left hand into a cooler to grab a fish for her new friend that 10-year-old Annika realized just how much her life would change.
Inside the cooler was a bionic right arm, designed and built for her by a research team at the University of Central Florida (UCF) in Orlando. Employing scientific precision and an artist’s panache, the UCF nonprofit — known as Limbitless Solutions — is combining old and new technologies in an effort to make prosthetics more accessible.
It recently added a new Tormach milling machine to its portfolio of equipment — which includes a thermoforming machine, 3D printers and a desktop injection molding machine — and it is always on the lookout for new partners and sponsors.
In a video about the project, a beaming Annika shows off her prosthetic, which is emblazoned with a floral pattern she chose.
“I can wear it outside, and a lot of people will stare at me, and they won’t be like, ‘What is that?’ They’ll be like, ‘Oh, my gosh, it’s so pretty!’ and, ‘Where’d you get it?’ and ‘Where can I get one?’ ” Annika said.
To Albert Manero, the president and CEO of Limbitless, Annika’s reaction means everything.
“I think if you asked the kids, they’d probably tell you it was never about being able to pick things up. It was much more about changing the conversation around them. When you see the kids smile, and they realize this is theirs and they’re taking it home and it’s going to bring them that level of function and that competence, that’s the moment,” he said.
Wrapped with love
The signature of Limbitless’ arms is their sleeves — personalized designs selected by their users and hand-painted by artists using donated automotive paints. Each child gets at least two sleeves, thermoformed from sheets measuring about 100 square inches on a desktop Formech device.
To make the arm his or her own, each user chooses the designs on the thermoformed sleeves that cover his or her prosthetic — everything from logos and Marvel characters to an homage to the Blue Man Group.
“Each of our patients, when they receive the arm, they’ve already participated in some of those design decisions, and they already feel like it’s a part of their expression or a part of themselves, that there’s a reflection of their own personal identity, even before they receive the arm,” said Dominique Courbin, who along with Manero and a third engineer, John Sparkman, co-founded Limbitless.
In a testimonial on the Limbitless website, Zachary said he can now ride his bike with two hands, so his back doesn’t get sore.
“I also noticed that people stopped asking me ‘What happened to your arm?’ and started asking me, ‘Where did I get my cool arm?’ I'm so thankful for this gift.”
“He really gets how it’s supposed to work,” Annika said of Manero, who received his doctorate in mechanical engineering from UCF.
Getting started
Manero’s life-changing moment happened in his car around the spring of 2014, while listening to the radio.
A journalist’s report broke down the problem: So many kids with limb differences, so few prosthetics. In that moment, the former Fulbright scholar found his calling.
Currently in the U.S., prosthetic arms can range in price from $40,000 to about $100,000, and unlike legs, which insurance companies usually consider medically necessary, arms quite often aren’t covered. Children, who can grow out of a prosthetic in about 18 months — or about as quickly as they do shoes — often are shut out, Manero said.
Even when insurance policies cover a prosthetic limb, families can find that the devices are beyond their resources.
"Oftentimes, even at like 80 percent coverage for that device, 20 percent will easily be outside of what most American families can support,” he said. “And this is definitely different in different countries, and insurance rates and reimbursement are totally different in Europe, and so we try to specify where those different problems lie.
“In the United States, there may be access to things, but there’s not the financial reimbursement, and then overseas, there might be financial reimbursement but not as equitable of access, and so it is a global challenge with nuances that we’re trying to work towards.”
Inspired by the National Public Radio report, Manero turned to fellow students and researchers in UCF’s manufacturing lab to find a way to help.
Eight weeks later, they had built their first limb, for a 6-year-old boy named Alex.
Making a difference
Since it started, Limbitless has provided 40 arms to 35 people. Its “Bionic Kids” family includes one adult — a woman who modeled the device in 2016 during New York Fashion Week.
According to the U.S. Centers for Disease Control and Prevention, researchers estimate that one in every 1,900 babies is born with an underdeveloped limb in the U.S.; some babies are born with issues involving both upper and lower limbs.
Cancer, other illnesses and accidents also can claim limbs. Among children who have lost limbs due to trauma, lawnmower accidents are the leading culprit, Manero said.
Because they are mostly 3D printed, limbs created by Limbitless might not meet the load-bearing requirements of prosthetic legs, but for people who need arms, the process could open opportunities.
“Our goal is to adapt to any geometry, organic geometry, to be able to support anyone who wants a prosthetic,” Manero said.
Limbitless’ first recipients had limb differences due to amniotic band syndrome, a condition that occurs when strands of tissue wrap around a limb or limbs of a fetus, cutting off blood flow. But Limbitless — which is seeking kids ages 7 to 17 who need bionic arms to test the devices as part of its ongoing quest to gain approval for the devices from the U.S. Food and Drug Administration — isn’t stopping there.
It can help children who have limb differences caused by any number of conditions, including amputations, as long as the upper-arm area is intact enough to accommodate a prosthetic and the prosthetic arm is substantial enough to house electronics to translate upper-arm signals to lower-arm movements.
In addition to bionic arms, Limbitless is looking for other ways to help. In partnership with the Mayo Clinic, the team is working to make wheelchairs that are responsive to facial movements.
Printing possibilities
From the start, seeing how Alex, Limbitless’ first Bionic Kid, took to his new arm made the work “addictive” for everyone, said Courbin, who first became acquainted with the project as an assistant machinist in the UCF lab.
To begin the work, the engineers pressed into service a couple of Stratasys printers that UCF had on hand.
The ability to build low-cost, one-off parts, or prototypes, is a benefit of 3D printing, said Jesse Roitenberg, the director of segment sales for Stratasys, which has become an official sponsor of the nonprofit.
“Our customers are always showing us new and inventive ways to use our equipment. This case is no different, but what makes us more proud is the impact on lives that this is making,” Roitenberg said. “Seeing parents tear up when their child is presented with a new custom prosthetic and then that child participating in an activity they couldn’t before makes us so proud to have selfless partners that truly care about those in need.”
According to Manero, Limbitless used Dimension Elite and Dimension 1200es printers. When its original machines were discontinued, Stratasys provided an upgrade — six Fortus 250mc printers.
To keep things simple, the team uses ABS for all its plastic parts.
“It’s a standard kind of engineering plastic. And we were very comfortable from working with ABS from the 3D printing side. … Knowing those material strengths, knowing those kind of performance envelopes of ABS, it was simple to kind of just migrate those 3D printed designs to injection molded designs,” said Courbin, a mechanical engineer who is now Limbitless’ director of production.
Addition by subtractive (manufacturing)
Honing the process brought the benefits of injection molding into view.
While the socket that provides attachments to the user is customized, based on each child’s anatomy, not all of Limbitless’ prosthetic components have to be tailored.
“We made this decision matrix of which parts would benefit the most from being made quickly, which were changed least,” Courbin explained. “We started with the most stable kind of design, and then just kind of worked our way through there. … We’ve identified our top 16 parts that we will eventually injection mold, and we've done about nine of them so far.”
All told, the Limbitless arms weigh less than 1.5 pounds — compared with other arms that weigh around 4 pounds, when made for children, or about 7 to 8 pounds for men.
With spacer parts that can be replaced or added, the design allows Limbitless to provide arms that can grow with their users; they are modular, giving Manero hope the project’s impact will be able to reach more users, as it acquires access to technologies that can accommodate bigger volumes.
“As we continue to look to scale, we’ve been really working on an effort to standardize a lot of the structural core parts that are similar across everybody,” he said.
Limbitless’ largest injection molded part measures only about 2 cubic inches and is about 6 inches long.
Mothballed in a closet at UCF, the Limbitless team found an ad-hoc injection molding solution — a Model G-55T pneumatic desktop press from Morgan Industries.
It has no auger and commands 20 tons of clamping force, with a maximum shot size of 3 cubic inches, according to Courbin and Manero.
The engineers have retrofitted the machine with electronics for semi-automation, Manero said.
“In the context of making children’s arms, that happened to be the perfect size for us to use. And that’s where I think that a lot of the companies that have been formed around making equipment — not necessarily for the machine shop, doing like 1,000, or tens of thousands of things — but to be able to enable innovation, that’s where that magic is happening, because it does allow you to build something that can then go and be used to support the community,” Manero said.
Preparing the mold
At employee-owned Tormach, the magic happening on the UCF campus became evident once Limbitless developed a need for molds.
“We truly feel like what Albert [Manero] and the Limbitless folks are bringing to the world is fantastic. … Not only are they providing children with bionic arms, but they’re making it fun for the kids,” said Lori Morrison Bufalo, the marketing director for the Madison, Wis.-based company, which began supplying equipment to Limbitless in late 2020.
Designed for do-it-yourselfers, as well as machine shops and mold makers, Tormach’s equipment is ideal for small volumes, and the company’s software is easy to use, Morrison Bufalo said.
The Tormach equipment produces good finishes, Courbin said.
“We were perfectly comfortable using the machines; the price point was perfect; the power requirement was perfect; and then the size requirements, everything was just that perfect spot for us.”
While Limbitless uses its equipment to make aluminum molds and components, Tormach’s technologies can handle many other materials, depending on the cutters users specify. Being able to do the work in-house streamlines Limbitless’ process.
“If you’re outsourcing it, it adds to the time to market that they’re trying to get something completed. It’s a challenge sometimes, when you’re using a third party and you want to make one minor modification to it,” Morrison Bufalo said.
“Working with Tormach, we’ve unlocked some new capacities, and we do hope we’ll be able to continue to innovate for new devices, new equipment that can help more people,” Manero said.
Team approach
What began as an impulse to help just one child has grown from an 18-student effort into a 35-member team, including engineers, artists and five full-time staff members. Sociologists work with children and their families.
A program called Limbitless Scholars, open by application to all undergraduates of any major, allows students to find ways to dedicate their talents to the mission. The nonprofit’s website — replete with statistics, videos and graphics — testifies to the nonprofit’s multidisciplinary approach.
There is even a team of developers for video games — that’s how the children learn how to manipulate their arms, using sensors that provide them and their prosthetics a way to sync up.
“It’s separating any sort of alienation or any sort of frustration away from the device. People are very used to being frustrated with video games. We found that a person can be terrible at a video game, and they’re OK with that,” Courbin said. “But there creates this bad feeling or distaste when they’re not good at controlling a part of themselves, so, by being able to separate that, by the time that they strap on the arm, the arm already knows what sort of threshold the person’s used to; the arm is aware of those characteristics that we built in the video game.”
Depending on the specifics of the trial in which the children are participating, some can take their arms home on their first visit to the lab, Manero said.
With their new arms, the children can open and close their hands, give a fist-bump or a high-five, or play sports, as Annika demonstrates on the soccer field.
Personal touch
On the day she received her arm, Annika leaned over to caress Winter, a dolphin who lost her tail as a baby after becoming entangled in a rope attached to a crab trap. The moment is captured by video. Two other Bionic Kids dip their hands into the water to greet Winter, whose tale of survival became the inspiration for the movie “Dolphin Tale.”
Along with Winter, who sported her prosthetic tail, they reminded Annika she’s not alone, Manero said.
“Today, you got to watch Annika meet Wyatt and Alex, a community of children and parents who are all of a sudden being connected.”
An earlier video, shot when Wyatt was 12, shows the big reveal. The boy, who has autism, is ecstatic as he takes in the sights during what he thinks is a behind-the-scenes tour his mother has won before a performance of the Blue Man Group — which he loves.
The performers come out to greet him, and he screams, jumping up and down.
Moments later, one of the performers opens a chest, in which is nestled Wyatt’s new prosthetic.
“It’s pretty awesome!” he exclaims.
The arm is deep blue, a perfect match for a daub of paint another of the performers has silently rubbed on Wyatt’s cheek.
For Manero, Limbitless’ mission has always been more than just making prosthetics for kids.
“It is incredible to watch them have that experience when they realize that the arm gets to go home with them, and we’ve seen that just their smiles light up," Manero said. "And we’ve also seen children look down in the sunshine and they can see their shadow with two limbs for the first time, and they stopped us and were like, ‘This is a big moment.’ ”
Karen Hanna, senior staff reporter
Contact:
Formech USA, Middleton, Wis., 608-424-2524, https://formech.com
Limbitless Solutions, Orlando, Fla., 407-823-6757, www.limbitless-solutions.org, [email protected]
Morgan Industries Inc., Long Beach, Calif., 562-634-4074, www.morganindustriesinc.com
Stratasys US, Eden Prairie, Minn., 952-937-3000, www.stratasys.com
Tormach Inc., Madison, Wis., 608-849-8381, www.tormach.com
Looking to grow
Limbitless Solutions, a University of Central Florida research team that has worked with children ages 6 to 17 who need bionic arms, is looking to move to the next level, including creating prosthetics for adults. In August, it moved into another facility, but space and its access to technologies and materials put some restrictions on what it is able to do.
“Our real hope is to be able to do this globally, so we can help any child that really would like a prosthetic,” said Albert Manero, the president and CEO of Limbitless, a nonprofit he founded with two other people.
Already, it’s on its way — with arms that cost about $1,500 for hardware, compared with $40,000 and more for other devices. The cost to put a child though a full, one-year clinical trial for the experimental arms is about $10,000, not including travel expenses.
The nonprofit is looking for donors and partners.
“If we can scale our production, from right now like 20 arms per study, to eventually like 100 arms in a run, there’s a considerable cost savings that can come with that. We do know that there will be room to improve some of those numbers as we continue to grow,” Manero said.
The organization’s current goal is to find sponsors to fully fund 100 Bionic Kids — which would require $10,000 to support each bionic arm and the clinical trial costs per Bionic Kid. It is currently seeking 20 trial participants at one hospital and five at another.
Participants become part of Limbitless’ family of Bionic Kids.
“Combined with cutting-edge electronics, we have worked to make things lighter, faster, more colorful and artistic while listening to children about what they’re looking for, what their needs are; [that] has really helped us transform this technology. We found that kids are able to embrace their new bionic solutions, simply because it reflects some of their personality and their expression,” Manero said.
Contact:
Limbitless Solutions, Orlando, Fla., 407-823-6757, www.limbitless-solutions.org, [email protected]
Karen Hanna | Senior Staff Reporter
Senior Staff Reporter Karen Hanna covers injection molding, molds and tooling, processors, workforce and other topics, and writes features including In Other Words and Problem Solved for Plastics Machinery & Manufacturing, Plastics Recycling and The Journal of Blow Molding. She has more than 15 years of experience in daily and magazine journalism.
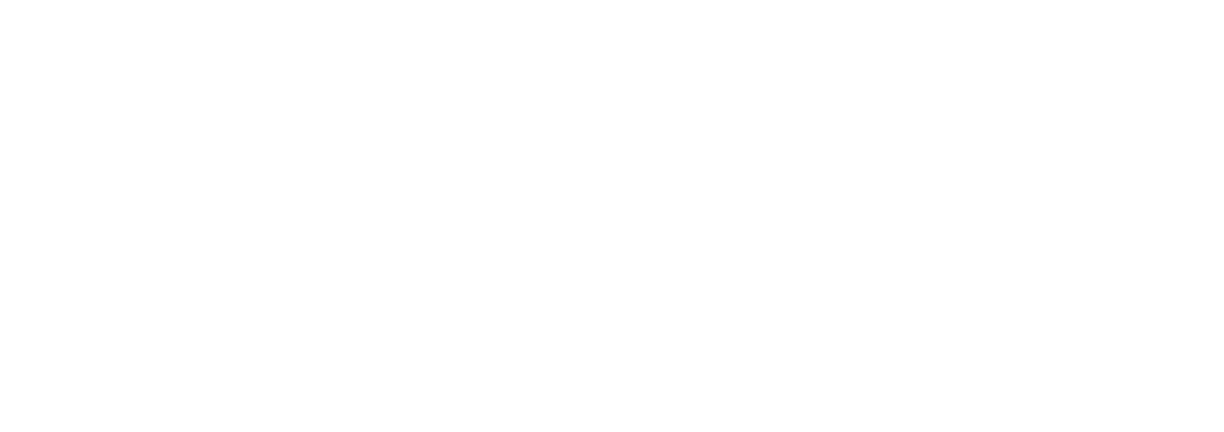