CCM48S D Sacmi’s continuous compression molding machines cut a suitably sized pellet from melt produced by its plasticization unit, then insert the pellet into a mold cavity to be compressed into its final shape. Compression molding is used to produce more than 45 percent of plastic beverage caps. The D version, which is the latest-generation Sacmi rotary molder, features 48 cavities with the ability to mold products with a diameter up to 1.49 inches.
What’s new? Incorporation of the CMFlow extruder, which features a 35mm screw and is now standard equipment on the CCM48S D. The CMFlow extruder also can be a retrofit for some earlier generations of compression molders, depending on the automation version.
Benefits Lower energy use and simplified maintenance thanks to the CMFlow extruder. Energy consumption can be reduced as much as 9 percent, depending on the cap format. The CMFlow has a maximum throughput of almost 441 pounds per hour — matching the output of traditional extruders with a 75mm diameter, while fitting in a footprint about 3 feet shorter. Sacmi said customers are seeing reductions in scrap and the time needed for color changes.
Sacmi USA Ltd., Des Moines, Iowa, 515-276-2052, https://sacmiusa.com
David Tillett
Associate Editor David Tillett writes and edits for Plastics Machinery & Manufacturing, Plastics Recycling and The Journal of Blow Molding. He covers new products, industry news, patents and consumer and business equipment. He has more than 20 years of experience in daily newspaper, online and magazine journalism.
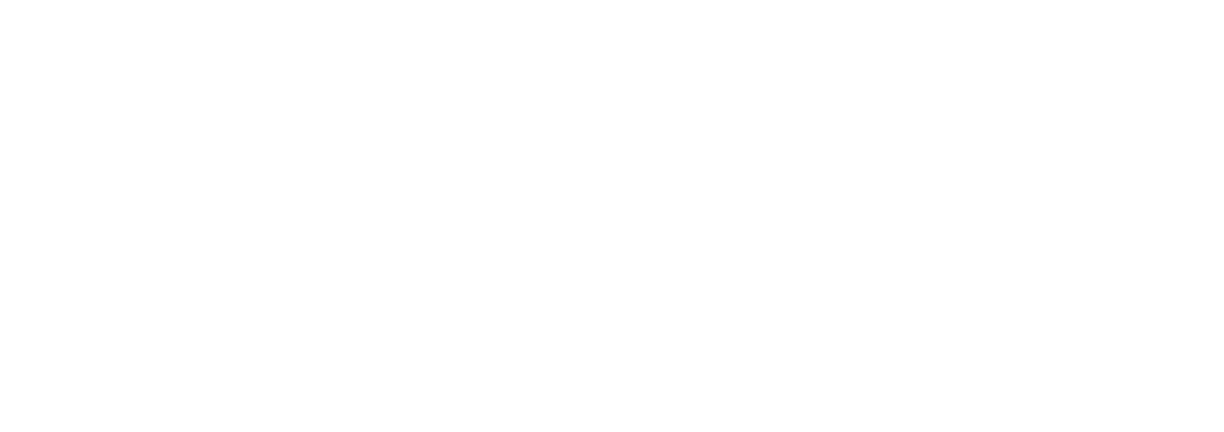