By Karen Hanna
3D printing is poised for its next leap forward, experts say, as technology makers increasingly boast the ability to produce bigger volumes more quickly. While some manufacturers tout situations in which their 3D printing can replace molding, others seek coexistence.
In a webinar announcing his company’s new Xip Pro, Michael Currie, chief product officer for Nexa3D, ticked off some of the situations in which 3D printing has traditionally left its mark — including applications that require small volumes, quick turnarounds or particularly complex shapes. Then, in offering up another application, he mentioned a bigger possibility — replacing injection molding.
“There’s a fourth opportunity which we haven’t talked about yet. And this is instead of trying to replace formative manufacturing — injection molding — straight up, which we believe we can be able to do with the Xip Pro,” he said. “ ...This opportunity is to actually augment the formative process …” by producing tooling.
3D printing might strike fear in the hearts of some manufacturers, said Lewis Simms, Nexa3D’s head of industrial product marketing. But some experts — including Currie — say they should see opportunity instead.
“I would say from a business perspective, I think that you’re not going to make it a black-and-white decision on, ‘OK, I’m going to go all in 3D printing and go melt down my injection molding machine.’ I think what’s going to happen is these companies are going to grab ahold of that technology and then use it to capture opportunities that they would otherwise have to pass up,” Currie said.
Related: 3D printing is fulfilling its promise for mass customization
The benefits of 3D printing — including the potential to shorten prototyping and time-to-market schedules, and to design and create parts that were previously difficult or impossible to produce — should have the attention of manufacturers that use traditional processes. The process also provides an avenue for manufacturing aftermarket parts that long ago disappeared from inventory.
Low-volume parts and parts with tricky geometries or unreliable supply chains are a good place to start.
“If I were an injection molder, first of all, I would add 3D printing as a tool to my business. And I would look to see … where can 3D printing disrupt the market?” she asked.
A hybrid approach already is becoming commonplace, said 3D printing expert Brent Stucker, who in May started his own firm, 3DX Consulting.
“We’ve come a long way. I would say, for people who make physical products, it’s very rare if they don’t use additive manufacturing (AM), or 3D printing somewhere in their ecosystem, either to prototype something, or actually as a production operation,” said Stucker, an AM expert with decades of experience at various OEMs.
How it started
From their early days, when many 3D printers were marketed as “anyone-can-make-anything” garage-tinkerers’ toys, the technologies have come a long way. But there are still strides to be made.
“Our holy grail is to scale up our ability to produce lots of parts,” Currie said during the webinar. “... Can we replace traditional manufacturing? If so, where and what is the state of the play right now, in that sense? So, the first opportunity we have is competing against — we always benchmark ourselves — against injection molding.”
Related: See innovative parts produced using 3D printing technology
In a May 25 conference call following his company's $1.8 billion purchase of Desktop Metal Inc. Burlington, Mass., Stratasys Ltd. CEO Yoav Zeif said AM hasn't lived up to the hype.
“I’m here for three-and-a-half years, and I’m struggling with the positioning of additive globally,” he told investors, according to a report from IndustryWeek, an Endeavor Business Media publication.
From labor shortages to sustainability concerns and operating efficiencies, AM has failed to provide manufacturers solutions to the biggest challenges they face, Zeif said.
“We are the only profitable company in this industry, so something doesn’t work... Additive doesn’t provide the quality per part, cost per part or process that manufacturing need.”
While conceding the technologies aren't fully mature, executives of other AM OEMs continue to tout their potential.
Experts seem to agree — it’s not there, yet.
Experts on 3D printing delineate its evolution as an industrial-scale technology into a few basic stages. Thanks to increasing build rates and improved precision, “after more than 20 years of development, 3D printing has evolved from a prototype strategy (rapid prototyping) to a small- and medium-series production strategy,” states a prepared Q-and-A with Aim3D managing director and founder Vincent Morrison, whose company released its composite-extrusion-modeling (CEM) printer, the ExAM 255 in late 2021.
As Simms sees it, 3D printing has evolved from its first three stages — design, prototyping, low-volume or bridge production — to mass production. So far, it’s found a niche at every step along the way, including as a tool for making spare parts, up to churning out mid-sized volumes.
That will make the battle for part orders of mid-sized volumes competitive, predicted Fabian Krauss, head of polymer systems for EOS.
“Injection molding will keep defending the lower, the mid-volume segment,” he said.
With “big industrial-scale machinery that is ready to run 24/7/365, day in, day out,” EOS is well-positioned for the next stage, Krauss said.
“I think the future of 3D printing is that 3D printing will be complementing traditional manufacturing in the supply chains. … We’re now entering Phase 4, which is serious production of additive parts in the supply chain. I think this will define the industry for the next five years. And that means quality is a given. It’s now about cost and scalability,” he said.
Current state of play
Zeif isn't alone in believing that AM has fallen short. Even so, it's captured a big shared of manufacturing.
“When I started in 2010, I think we were somewhere on the upward slope. 3D printing was the next big thing. It was in ‘Time’ magazine, in ‘The Economist.’ ‘Forbes’ had a big article about it, and it was supposed to be the new future. We would print entire airplanes, entire cars, and so on. That was the peak,” Krauss said.
Not that 3D printing isn't already cashing in.
“The global 3D printing market size is projected to grow from 18.33 billion [dollars] in 2022 to 83.90 billion by 2029,” said Phil DeSimone, a member of the CEO's office and co-founder at Carbon. “Large manufacturers are looking to use technology for mass production — that technology is 3D printing.”
One source of growth could come from the White House, which last year launched AM Forward. Included in the initiative are pledges of investments in new manufacturing facilities, as well as small- and medium-sized companies, and the development of workforce training and apprenticeship programs dealing with AM.
Large manufacturers, including GE Aviation, Honeywell, Lockheed Martin, Raytheon and Siemens Energy, along with their U.S.-based suppliers, have entered a voluntary compact supporting adoption of new AM capabilities.
“Each of these iconic companies will make clear, public commitments to purchase additively produced parts from smaller U.S.-based suppliers; train the workers of their suppliers on new additive technologies; provide detailed technical assistance to support their suppliers’ adoption of new capabilities; and engage in common standards development and certification for additive products,” a White House news release states.
Derek Vilim, hardware product management for Formlabs, whose 3D printers have made over 100 million parts, said manufacturers are taking notice of AM.
“Companies of all sizes in diverse industries, such as engineering, manufacturing, automotive, aerospace, dental, medical, education, entertainment, consumer products, audio and more, have embraced this technology to innovate new product designs, test prototypes, manufacture special purpose-built tools, models and props, and customize products at more accessible price point than before,” he said.
Numbers game
In a video promoting its newest printer, Nexa3D sums up the Catch-22 it sought to tackle with the release of the Xip Pro. The challenge has been with 3D printing since its beginnings: “Additive Manufacturing, easy to set up but expensive to scale.”
“This applies to all branches and markets; otherwise, additive will not make the broad and wide-[ranging] step into series production. To achieve this, we need more productive and more robust AM machines and processes," Morrison said.
In cases where 3D printing eliminates the need for tooling, it can strip from traditional manufacturing processes major hurdles of time, labor and costs. Bigger volumes, however, drive down the price-per-part of those traditional steps.
But Vilim said, “Additive manufacturing can directly compete with various traditional plastics processing techniques, as a more cost-effective option. It’s also a faster production method for low and medium quantities of plastic components, removing the need for tooling, so engineers and designers can go straight to production with their 3D files.”
How many parts 3D printers can reasonably handle before tool making becomes a more economical approach varies by part and industry.
AIM3D, for example, is working to scale up to produce 30,000 automotive parts as part of a collaboration with Schaeffler Technologies AG & Co. KG, Herzogenaurach, Germany, and ZF Friedrichshafen AG, Morrison said.
Other OEMs reported they can compete on some projects that involve 100,000 or more parts.
While 3D printers from Nexa3D and other OEMs can handle lots of kinds and geometries of parts, Simms cautioned manufacturers should practice discernment to determine which situations make sense.
“The decision to make something with 3D printing technology has to not just make technical sense, like, ‘Can I print it?’ But it also has to make business sense: ‘Should I print it?’ ” he said.
He offered some questions to consider: Do I have a technology with the quality and performance of the competing or primary technologies to print it? Can I do it in the same time? How many parts can I pump through the system?
To reduce the costs of 3D printing, 3D printer throughputs must increase, according to AIM3D.
“If the mechanical requirements must not be 1:1 to traditional manufacturing processes or if the geometry can be adapted to additive needs, then the AIM3D ExAMs are economical[ly] the right choice for up to 3,000 parts,” Morrison said. “If the customers can also change the geometry to optimize the process times or maybe join two or three parts into one, then the series number can increase up to 10,000 parts. For higher numbers, we are working with our customers on special machine concepts, which are integrated in their production environments.”
Democratizing the manufacturing process
For Mason, 3D printers represent potential.
“There are so many new things that are going to be on the planet that aren’t here today, because people are going to be able to create in ways they weren’t able to create before, because we brought the cost of failure down so low,” he said, of his company’s prototyping process.
With 3D printing, parts with projected volumes once deemed too small to manufacture have a way to reach market that doesn’t require tooling.
According to Simms, who discussed Nexa3D's Xip Pro, that gives product developers, as well as manufacturers, the freedom to try out designs that might otherwise be quashed over profitability concerns.
“Because for your setup, maybe a couple hundred, or maybe 1,000 or 2,000, or 5,000 parts was going to be too low for you or too expensive for you to produce through traditional tooling, or maybe you wouldn’t be able to meet the deadlines,” Simms said. “Now, this also opens up that opportunity for molding houses, as well.”
Hurdles to overcome
Owing to its maker roots, 3D printing still has something to prove.
As 3D printer OEMs continue to home in on improving print speeds, materials and process control, consultant Rosman and James Reeves, global director of polymer sintering for Voxeljet, which is anticipating the commercial release of a new printer later this year, identified a few challenges that have little to do with the technology itself.
“If you’re going to use 3D printing in a production environment, which is kind of mission-critical ... then your service-level agreements need to be much tighter; your customer support has to be much better,” Rosman said. “You have to have faster response times, and your printers have to be more reliable and robust. So, I think there’s certainly a lot of work on the material side. There’s work on the hardware side, and then there’s work around qualification.”
Rosman recounted how one manufacturer spent six months showing its printed replacement of a part caught up in a web of supply chain snags was just as good as the original.
With the struggles it was experiencing at the time, the work paid off — lead times for the original, traditionally manufactured components were nine months.
But 3D printing still has to make its case.
“3D printing grew from prototyping,” Rosman said. “So, in the past, for a lot of machines, the quality was fairly low, and that’s stuck in people’s minds, and, so, they’re very skeptical.”
Part design is another issue, Reeves said.
“Most new customers come to us with a finished product design, which are nearly always moldable and therefore don’t benefit from 3D printing. 3D printing needs be considered during product conception, when there is an opportunity to differentiate the product by using the benefits of 3D printing. Our biggest users designed products from Day 1 to use 3D printing,” he said.Just another tool in the toolbox
While it still experiences growing pains, 3D printing is becoming part of the routine. Experts say its role will only grow — even if it never fully overtakes injection molding.
“I think you’re going to find that, more and more, additive manufacturing is not considered a niche process; it’s just considered one of the things in our manufacturing facility that we use to make this part,” said independent consultant Stucker, the co-author of a textbook on the topic, “Additive Manufacturing Technologies.”
The Formlabs’ executive said he believes AM Forward will lead to the creation of high-paying jobs and make the supply chain more resilient.
Buoyed by the initiative, AM is poised to transform manufacturing.
“Fueled by technology innovation and improving material properties, additive manufacturing is on a quick path to expand far beyond rapid prototyping toward end-use parts, mass production and consumer components,” Vilim said.
That leaves a place for each tool and process to find its own niche.
Most manufacturing companies will have 3D printers to perform some applications, Reeves said.
“It is important to recognize that while 3D printing is slated to transform the manufacturing industry, its intended use is not to replace traditional manufacturing methods, tools, or processes, but rather work alongside them and provide differentiated value to its users. Where traditional manufacturing processes are limited in their capabilities, 3D printing technology thrives,” said Francois Minec, global head of 3D polymers for HP’s Personalization and 3D Printing business.
With so many kinds of 3D printers on the market, Rosman said it’s anyone’s guess which ones will shake out as go-to industrial technologies.
Build speed, part size and economic efficiency of production could be factors in the competition among various 3D printing processes, AIM3D’s Morrison said.
Finding out which technologies win out in the end could take some time — as Stucker sees it, compared with how far the technologies will continue to evolve, growth in 3D printing is just getting started.
This still is the early-adopter phase.
“We have a lot of things that additive manufacturing could do that people are not yet utilizing it for,” Stucker said.
“A very low percentage of the parts produced as end-use components are made with additive manufacturing today. I think that percentage is going to grow and grow and grow. Where is it going to plateau? I don’t know. But it’s going to plateau in my mind in the hundreds of billions of dollars of products, or maybe even to the trillions of dollars of products.”
Karen Hanna, senior staff reporter
Contact:
3DX Consulting LLC, Park City, Utah, 435-363-5197, brent.stucker@outlook.com
AIM3D, Rostock, Germany, 49-381-367-66090, www.aim3d.de
Arburg Inc., Rocky Hill, Conn., 860-667-6500, www.arburg.com
Carbon Inc., Redwood City, Calif., 650-285-6307, www.carbon3d.com
EOS, Pflugerville, Texas, 512-388-7916; Novi, Mich., 248-306-0143, www.eos.info/en
Formlabs Inc., Somerville, Mass., 617-702-8476, www.formlabs.com
HP Inc., Palo Alto, Calif., 650-857-1501, www.hp.com
Nexa3D, Ventura, Calif., 800-797-0633, www.nexa3d.com
Tali Rosman, [email protected], via Linkedin at www.linkedin.com/in/talirosman
Stratasys Ltd., Eden Prairie, Minn., 952-937-3000, www.stratasys.com
Voxeljet America Inc., Canton, Mich., 734-808-0025, www.voxeljet.com
Karen Hanna | Senior Staff Reporter
Senior Staff Reporter Karen Hanna covers injection molding, molds and tooling, processors, workforce and other topics, and writes features including In Other Words and Problem Solved for Plastics Machinery & Manufacturing, Plastics Recycling and The Journal of Blow Molding. She has more than 15 years of experience in daily and magazine journalism.
Related
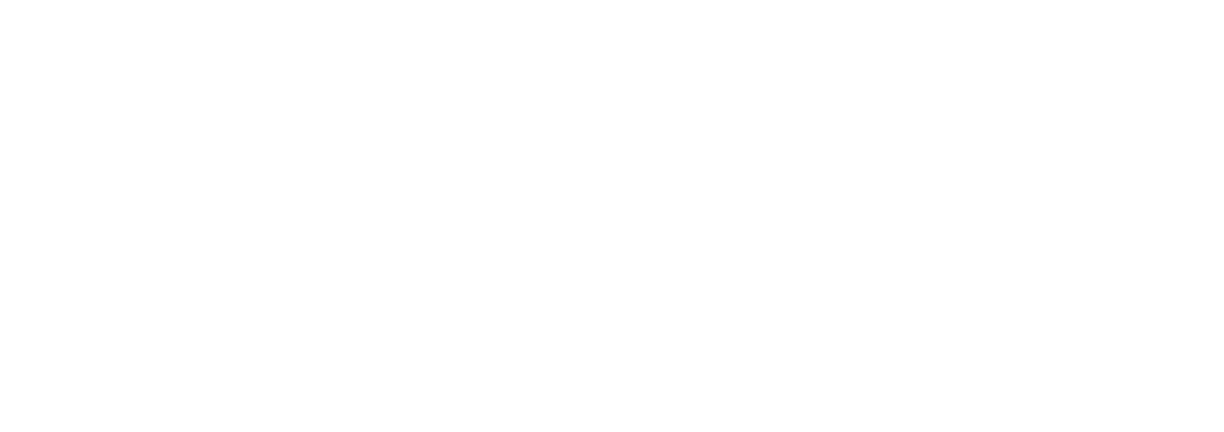