Makers of sorting equipment and metal-detection technologies are upgrading their products to meet recyclers’ demands for purer material streams.
Tomra
Tomra is touting its work in adding artificial intelligence to its high-precision Autosort flake-sorting equipment with an add-on called Gain. The company said Gain can quickly adapt to new waste streams and increases sorting effectiveness.
Tomra demonstrated Gain at Ecomondo, an Italian show for green technology in November, on its AutoSort system. AutoSort has a conveyor belt that carries material past sensors and cameras that identify colors and textures. It can handle a variety of waste streams and objects, including packaging, mixed plastics and commercial and industrial waste.
Gain enhances existing sortation systems, Tomra said. It classifies objects based on camera data. Deep learning allows the image identification function to get better over time.
The first version of Gain uses algorithms to eject cartridges used to hold silicone sealant from a PE stream.
Tomra said the Gain system works on a conveyor belt traveling up to 10 feet per second.
Tomra also is marketing its new Innosort Flake optical sorter, which combines color and material sorting and can recognize plastic flakes 2mm in size. It utilizes RGB cameras and ultra-high-resolution near-infrared sensors.
“This all-in-one solution with ultra-high-resolution and specialized color sensor configuration offers superior performance with exponential results,” the company said in a news release.
Innosort Flake employs Tomra’s Flying Beam technology, which features continuous signal correction, an integrated light source and enhanced light distribution. The light technology saves up to 70 percent in energy costs, Tomra said.
Throughput is up to 6 tons per hour.
It is available in models with a 3.2-foot and a 4.6-foot scanner box above the material chute. It has a small footprint: 5.7 feet wide by 6 feet long for the smaller model; 7.5 feet wide by 6 feet long for the larger size.
Innosort Flake will be available in North America later in 2020. It was first introduced in China in September 2018.
Steinert
Steinert is continuing to develop the airflow system to boost the throughput and accuracy of its UniSort Film sorting system.
The latest version of the airflow technology, called Active Object Control (AOC), was shown at K 2019 and is now available in North America. It is especially effective on hard-to-sort films such as conventional PVC, bio-based, biodegradable and black agricultural film and paper. Typical uses are to remove paper and other impurities from batches of film prior to washing or for sorting out PE and PP packaging waste.
AOC uses air to stabilize pieces of film on the conveyor belt as they move through the detection area of the sorting machine. It also improves trajectory of the flakes as they leave the belt. Stabilizing the film to the belt surface “has a substantial impact on purity and efficiency,” a company spokesman said.
The enclosed airflow system does not emit fumes, Steinert said. Fans are located beneath the sorting belt to synchronize air speed to belt speed.
The Unisort Film sorter has been on the market for about five years. It is still available without AOC technology. It is suitable for recycling operations, as well as in processing plants.
An advantage of the AOC option is that it allows a smaller machine to run at higher speeds since pieces of film are not flying around as they go through the detection area. Steinert said a sorting machine equipped with AOC can run as much as 50 percent faster than a similar machine without AOC.
In addition to the new AOC technology, the UniSort Film processing system includes its Hyper Spectral Imaging (HIS) camera technology. It is located, along with the control system, in the UniSort Film’s bridge and monitors the entire width of the belt.
Sesotec
Sesotec has launched its Rapid Pro-Sense 6 metal separator for free-falling flakes. It is designed for inline detection and separation of magnetic and non-magnetic metal contaminants.
The newest version of the Rapid Pro-Sense series has a new reject mechanism designed for applications that require frequent color changes. Reject systems must be cleaned along with the rest of the conveying system during color changes to prevent mixing of colors. Sesotec’s new reject system is designed to be accessed and cleaned without tools. There are also optional water nozzles inside so that it cleans itself automatically.
The Rapid Pro-Sense 6 is primarily used for quality inspection and is typically installed directly before the flake is put into big bags, gaylords or silos. It is also used for quality inspection of incoming resin.
Sesotec said the unit protects processing machines and molds against damage, which reduces downtime.
The separator has a modular design and a low mounting height to facilitate integration of the metal separator in existing materials handling systems. An auto-clean system is available as an option.
Sesotec also has released Flake Scan, a plastic flake analysis system, designed to automate and speed up time-consuming manual testing of recycled material.
Flake Scan can be used to test incoming or outgoing material.
“A few minutes is all it takes to get reports on the composition of various plastics and on off-color components,” the company said in a news release.
For more information:
Sesotec Inc., Bartlett, Ill., 224-208-1900, www.sesotec.us
Steinert US, Walton, Ky., 800-595-4014, www.steinertus.com
Tomra Sorting Inc., West Sacramento, Calif., 916-388-3949, www.tomra.com/en/sorting/recycling
Ron Shinn | Editor
Editor Ron Shinn is a co-founder of Plastics Machinery & Manufacturing and has been covering the plastics industry for more than 35 years. He leads the editorial team, directs coverage and sets the editorial calendar. He also writes features, including the Talking Points column and On the Factory Floor, and covers recycling and sustainability for PMM and Plastics Recycling.
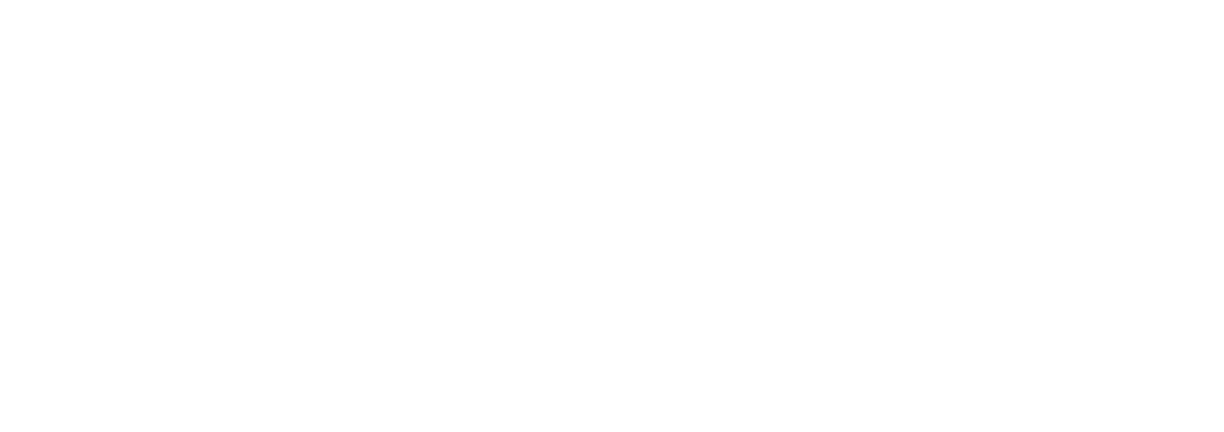