By Karen Hanna
Sustainability has driven the mission behind Refork SE, a Prague company formed in 2019 with the ambitious goal of replacing everyday plastic sundries with products that can decompose safely back into the environment. Buttressing that project are technical innovations that make processing bioresins possible.
According to Refork, as well as Mold-Masters, one of its suppliers, molders and mold makers must take account of flowability and the possibility of corrosion, along with narrow process windows due to the materials’ sensitivity to temperature changes and shear.
With a portfolio of Mold-Masters hot runners that has included four-, eight- and 48-cavity systems capable of producing 10-million-plus parts a month, Refork is looking for future growth. At the same time, Mold-Masters continues pushing the boundaries of what’s moldable.
“For us, Mold-Masters is more than a supplier, they are a development partner,” Refork CEO Josef Žádník said.
Replacing plastics
Refork started with the idea of using biopolymers to produce single-use products, said Josef Homola, a Refork founder and member of its supervisory board.
The team that would establish Refork unearthed their Holy Grail in 2018, when they developed an in-house blend of wood flour and natural polymers.
But the COVID-19 pandemic hampered initial demand, and as it subsided, European plastics processors began labeling straws with the word, “Reuse,” to satisfy demand for sustainability without making any actual changes to their products. European Union legislation has now cracked down on that trend, Homola said.
“We believe this is exactly the opportunity we have been waiting for, and that our significant production capacity and investment in state-of-the-art machinery will finally pay off, allowing us to fulfill our original vision,” he said.
Currently, Refork makes forks, knives, spoons, napkins and straws that are fully biodegradable in home composting, soil and marine environments. They are composed of wood flour waste from the lumber industry, a polyhydroxyalkanoate (PHA) binder and a variety of minerals that enhance mechanical properties.
From its early days, Refork worked with Mold-Masters to build its hot-runner systems.
With more than 20 years of experience with bioresins, Mold-Masters has the expertise to help customers transition from traditional, oil-based plastics to the biomaterials and post-consumer recycled (PCR) resins that it says are increasingly in demand. Generally, it helps convert those customers to sustainable materials for parts ranging from under a gram to just under 8 pounds.
“Bioresins can be very challenging to process compared to the common resins they typically aim to replace,” said Sudheer Thrissileri, senior director of product development for Mold-Masters. “This of course can make producing good parts very difficult and sometimes impossible.”
According to Mold-Masters, one concern was material degradation, as the PHA binders and flour tend to break down quickly during the injection process.
While both monolayer and co-injection tooling can run bioresins, Thrissileri said, manufacturers must tailor the mold to the application. Just as with traditional resins, mold makers should consider factors such as shrinkage, pressure drop and residence time, among other issues.
Biomaterials can be especially hygroscopic, and some, such as materials derived from sunflower seeds, can cause damage to internal mold components and increase the need for maintenance.
According to Homola, material flow posed Refork with particular problems.
“Since the core know-how of our company lies in the ability to combine expensive biopolymer with significantly cheaper fillers — up to 70 percent — this greatly affects material flow. I believe the biggest challenge has been managing the low flowability of our materials and their residence time to prevent degradation,” he said. “All our materials are based on PHA, which is highly sensitive to shear friction and high temperatures.”
Thrissileri said flow problems can result in visual defects.
He recommended Mold-Masters’ iFlow manifolds for enhanced management of melt characteristics such as shear, temperature and pressure drop. Designed for medium- and high-cavitation systems, the manifolds feature individually milled halves, which are brazed together. This unique manufacturing process gives designers a great deal of flexibility over each section and the ability to design both multiple melt channels and complex curved flow paths.
The iFlow manifolds are available with the company’s Master, Summit, Sprint, Axiom and select Fusion G2 hot runners.
When handling bioresins, Thrissileri said hot-runner design is important. The system should be paired with a high-performance temperature controller that complements it.
“Mold-Masters brazed heaters are permanently fixed and embedded within custom tailored heater channels,” he said. “These heater channels are unique to the component [providing] optimal thermal profile based on in-depth R&D testing and development. Heater channels are consistent from component to component, which allows for exceptional thermal consistency drop to drop.”
Compared to the brazed heaters, traditional heating technologing have “inherent limitations,” he said.
By maintaining precise temperature control, Mold-Masters said molders can better ensure part quality, while minimizing process variability and scrap.
Designed to minimize injection pressure so smaller presses could accommodate the process, the Refork hot-runner systems overcame the challenges of handling bioresins, Thrissileri said.
“Mold-Masters hot runners were able to achieve a consistent cycle time, minimize scrap and decrease the required injection pressure to enable the molds to be operated with smaller machines. Today, Refork produces about 151 [million] bioresin utensils on an annual basis using Mold-Masters hot-runner and temperature control systems,” Thrissileri said.
Further advances
When it comes to processing bioresins, both Mold-Masters and Refork still see opportunities for growth.
In November, Mold-Masters announced an Aizuwakamatsu, Japan, packaging company, Sanyoshi Lacquerware, had used a hot-runner system it supplied to produce a transparent cup made of 100 percent polylactic acid (PLA), a biodegradable material. The cup has a wall thickness of just 0.53mm.
According to Mold-Masters, PLA is thermally sensitive, corrosive and prone to visual defects, discoloration and degradation.
“The additional challenge with injection molding PLA in a thin-wall application is that PLA is a difficult material to inject into every corner of the mold due to its high viscosity,” Mold-Masters says on its website.
Because of their ultra-thin walls, cups can fully decompose within 30 days in ideal conditions, according to Sanyoshi Lacquerware.
“Mold-Masters’ Summit-series hot-runner system played a critical role in allowing us to push the boundaries of what’s possible in this application,” said Michio Komatsu, the packaging company’s president.
Meanwhile, Refork plans to further leverage its partnership with Mold-Masters as it eyes a new market.
“Refork is also planning to establish a production facility in the U.S., having already held negotiations in Chicago last year. If we launch production in the U.S., we definitely anticipate collaborating with Mold-Masters!” Homola wrote in an email to Plastics Machinery & Manufacturing.
Contact:
Mold-Masters, Georgetown, Ontario, 905-877-0185, www.moldmasters.com
More on our website
- Demand for biomaterials is strong, but the supply chain is weak. plasticsmachinerymanufacturing.com/55134683
- Most current machinery can process bioplastics; viscosity and temperature are key. plasticsmachinerymanufacturing.com/55135459
- What are biomaterials? Here are some terms to know. plasticsmachinerymanufacturing.com/55135453
Karen Hanna | Senior Staff Reporter
Senior Staff Reporter Karen Hanna covers injection molding, molds and tooling, processors, workforce and other topics, and writes features including In Other Words and Problem Solved for Plastics Machinery & Manufacturing, Plastics Recycling and The Journal of Blow Molding. She has more than 15 years of experience in daily and magazine journalism.
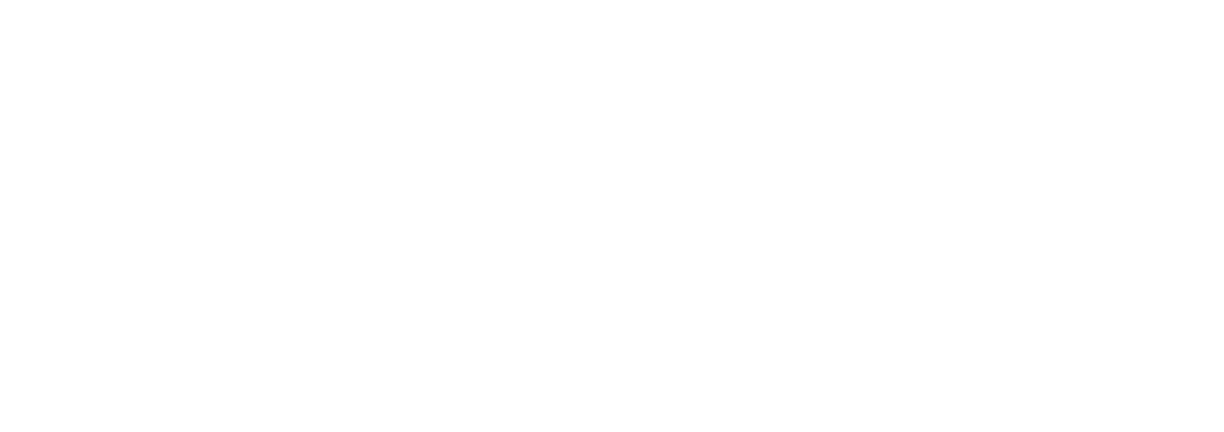