Report: Plastics drive lightweighting, fuel efficiency for auto sector
By Bruce Geiselman
The amount of plastics in automobiles produced in North America has increased as automakers seek to boost fuel efficiency, reduce carbon emissions and produce safety benefits like seatbelts and airbags, according to a new report from the American Chemistry Council (ACC).
In 2021, more than 13 million passenger automobiles and light-duty trucks were built in the United States, Canada and Mexico. The average weight of an automobile in 2021 was 4,287 pounds, a 3 percent or 121-pound increase compared to 2020.
Plastics and polymer composites in 2021 accounted for nearly 10 percent (411 pounds) of the average weight, up 16 percent compared to 2012 (354 pounds), according to “Chemistry and Automobiles: Lighting the Way to the Future of Motor Vehicles,” released in March by the ACC.
More than a dozen resins are used in significant quantities in automobiles, including on average 97 pounds of polypropylene (PP), 84 pounds of polyurethane foam, 41 pounds of nylon, 34 pounds of high-density polyethylene (HDPE), and 31 pounds of polyvinyl chloride (PVC).
Average vehicle weights have fluctuated over the years due to factors including consumer preferences (small cars vs. SUVs and light trucks) and gasoline prices. However, automakers in recent years have been trying to reduce the weight of vehicles to help meet the U.S. corporate average fuel economy (CAFE) fuel economy standards.
“Lightweight plastics and polymer composites play a critical role in today’s automobiles, as well as in the transition to next-generation vehicles, as they enable vehicle weight reduction that helps automakers meet increasingly stringent fuel economy standards, while enhancing safety for drivers, passengers, and pedestrians,” according to ACC's report.
Plastics make up 50 percent or more of the volume of an average vehicle but less than 10 percent of its weight, according to the ACC.
Plastics and polymer composites are being used throughout today’s vehicles. Examples cited in the ACC report include everything from exterior bumpers made of thermoplastic olefins (TPOs), to plastic composite hoods and door panels that resist dents and improve aerodynamics, to fiber-reinforced composites that can absorb four times the crush energy of steel.
Even windshields include a tear-resistant plastic layer that prevents occupant ejection. North American windshields come as a multi-layer unit. The addition of the plastic layer to glass windshields reduces the weight of the glass required.
Resins including ABS, polycarbonates and polypropylene are used in manufacturing instrument panels and airbag housings. Automated driver safety assist systems, such as cameras and sensors, are made largely out of plastic components.
Plastics today are being incorporated into the chassis, the primary framework of an automobile. Thanks to technology innovations, including fiber-reinforcement, plastics provide lighter weight, higher stiffness and lower cost than traditional materials including steel.
The ability to combine several parts into one is another advantage for plastics. What used to be several parts or components made out of metal and then assembled can often be manufactured as a single part from plastic, said Gina Oliver, senior director for durable markets advocacy within the plastics division of the ACC.
“When you’re reducing the number of parts or the number of components in an assembly, obviously, you’re reducing weight, no matter what, but then on top of that, when you look at our strength-to-weight ratio, the math is in our favor,” Oliver said.
Advances in acrylic fiber optic cables have eliminated the need for much of the heavy copper wiring used to illuminate dashboards, according to the ACC report.
“This means enhanced illumination of the interior, more accurate GPS data, and highly responsive ABS sensors,” according to the report. “Plastics are also used in switches and sockets, connectors, and wiring.”
High-temperature plastic parts installed under the hood can help automakers reduce weight and cost, according to the ACC report. Plastics also can help reduce the number of parts needed per component. Temperature resistant and thermally conductive plastics are used in heat-sensitive applications, including electric vehicle battery parts and enclosures. Plastic battery enclosures on average weigh 35 percent less than metal enclosures, which extends the range of EVs, according to the ACC.
As automakers transition to producing increasing numbers of electric vehicles, hybrid vehicles, plug-in hybrid vehicles and hydrogen fuel cell vehicles, it has a significant influence on vehicle weights and the materials composition of vehicles.
“EVs are heavy, right?” Oliver said. “They’re heavy vehicles because of that battery, so, you have to offset that range anxiety.”
For example, the Ford F-150 Lightning’s battery alone weighs 1,800 pounds, according to the ACC report. Fuel cells, used in hydrogen fuel cell vehicles, also add considerable weight.
In order to offset or partially offset those weight increases, automakers are using more lightweight plastics.
“Additionally, the desirable conductive properties of plastics and polymers composites make them sought-after materials for various components of electric vehicle batteries, including battery casings and enclosures,” according to the report.
Toyota in 1997 launched sales of the Prius, the world’s first mass-produced hybrid passenger vehicle. Since then, hybrid and EV sales have grown dramatically. In 2021, 1.4 million hybrid, plug-in hybrid and electric vehicles were sold in North America, which accounted for 16 percent of total vehicle production, according to the ACC report.
“I was excited but yet surprised to see the trajectory on the electric vehicles,” Oliver said. “And happy, because at the end of the day, sustainability is in everything that we’re trying to do here.”
EV sales are expected to continue to increase as President Biden in August 2021 signed an executive order setting a goal that 50 percent of all new passenger cars and light trucks sold in the United States in 2030 be zero-emission vehicles.
“As such, the market for critical chemistries such as polycarbonates, carbon fiber, flame retardants, and electronic chemicals, used in the operations and manufacture of hybrid, PHEVs, and EVs will likely increase,” according to the ACC report.
Plastics also will play a key role in building up the nation’s infrastructure required to keep electric vehicles charged, such as the components required in alternative fueling stations.
The chemistry value in an average automobile in 2021 was $4,069, a 20 percent increase as compared to a decade ago, according to the ACC report. With over 13 million passenger automobiles and light-duty trucks manufactured for sale in the United States, Canada and Mexico, the chemistry value in the North American automobile market reached nearly $53 billion in 2021.
That $4,069 value per vehicle includes $710 in plastics and polymer composites, $651 in synthetic rubber and elastomers, $540 in semiconductors and other electronic chemicals, $324 in fluids and lubricants, and $241 in textiles, along with other chemicals, according to the ACC report.
Bruce Geiselman
Contact:
American Chemistry Council Inc., Washington, D.C., 202-249-7000, www.americanchemistry.com
Bruce Geiselman
Senior Staff Reporter Bruce Geiselman covers extrusion, blow molding, additive manufacturing, automation and end markets including automotive and packaging. He also writes features, including In Other Words and Problem Solved, for Plastics Machinery & Manufacturing, Plastics Recycling and The Journal of Blow Molding. He has extensive experience in daily and magazine journalism.
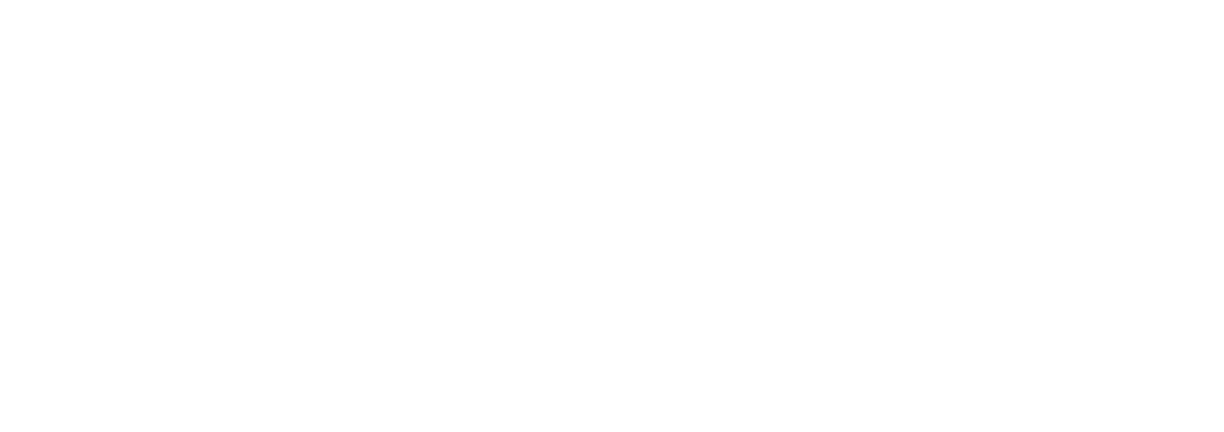