By Bruce Geiselman
The challenge of producing materials that are lighter-weight and that can handle the higher-temperature demands of electric vehicles (EVs) has at least one SABIC Petrochemicals representative excited for the road ahead.
“I think this is the most exciting time for anyone associated with the plastic industry, whether it’s the material manufacturers or Tier 1 manufacturers or anyone who is working in a plastic industry,” said Dhanendra Nagwanshi, global automotive leader for the company's EV Batteries & Electricals, at SABIC Petrochemicals.
Conventional materials, like steel and aluminum, have limitations as automakers are transitioning from internal combustion engine (ICE) vehicles to EVs, and plastics can address many of those limitations, he said. Plastics offer advantages including reduced complexity in parts manufacturing, allowing for the consolidation of several parts into one and weight reduction. Also, engineered plastics can provide better fire protection than aluminum.
As part of its Bluehero platform, designed to accelerate the world’s energy transition to electric power, SABIC has been developing new flame-retardant materials for use with EV batteries.
In an aluminum battery enclosure, flames can melt through the metal, endangering occupants of an EV. However, in laboratory testing, a battery lid manufactured with SABIC’s new Stamax FR resin prevented flames from breaking through during a 5-minute exposure. When the material comes into contact with intense heat, it forms char or an intumescent layer that is hard and stiff and prevents flames from penetrating the battery enclosure. Despite a 2,012-degree Fahrenheit flame on one side of a composite battery lid manufactured with Stamax FR, the temperature on the other side of the lid reached a maximum of only 392 degrees Fahrenheit, Nagwanshi said.
Using Stamax FR resin for a battery cover in place of aluminum can eliminate the need for a thermal blanket, reducing cost and weight, Nagwanshi said.
Honda made an EV battery pack cover for its CR-V model in China with SABIC’s flame-retardant PP compound. With the short-glass-fiber material, the EV needed no thermal blankets to comply with China’s EV fire safety requirements. The part reduced part weight by 40 percent versus a similar design in metal, according to SABIC.
Another advantage of using plastic parts, rather than aluminum parts, is reduced carbon dioxide emissions during manufacturing, Nagwanshi said.
“Plastic manufacturing processes bring some advantages in reducing the CO2 emissions during the manufacturing of these parts,” he said. “For example, we did some initial lifecycle-assessment, LCA, studies, and aluminum is a very high-energy intensive process. If we use methods like injection molding using our thermoplastic materials, our initial calculations are about a 10 percent to 15 percent reduction in CO2 emissions in manufacturing of a large part with thermoplastic as compared to a high-energy intensive process like aluminum.”
SABIC is working with automakers and parts suppliers interested in sustainability to supply them with more plastics made with recycled materials and biorenewable materials.
“We have a lot going on with respect to having a right portfolio of circular materials,” Nagwanshi said. “Recently, our CEO announced that by 2030, SABIC is committed to have 1 million [metric] tons of circular products.”
SABIC’s TruCircle solutions will include materials produced at the company’s first commercial advanced recycling plant in Geleen, Netherlands. In January, the plant was in the final stages of construction. It is expected to deliver its first commercial polymers this year.
Bruce Geiselman, senior staff reporter
Contact:
SABIC, Houston, 800-845-0600, www.sabic.com/en
Bruce Geiselman
Senior Staff Reporter Bruce Geiselman covers extrusion, blow molding, additive manufacturing, automation and end markets including automotive and packaging. He also writes features, including In Other Words and Problem Solved, for Plastics Machinery & Manufacturing, Plastics Recycling and The Journal of Blow Molding. He has extensive experience in daily and magazine journalism.
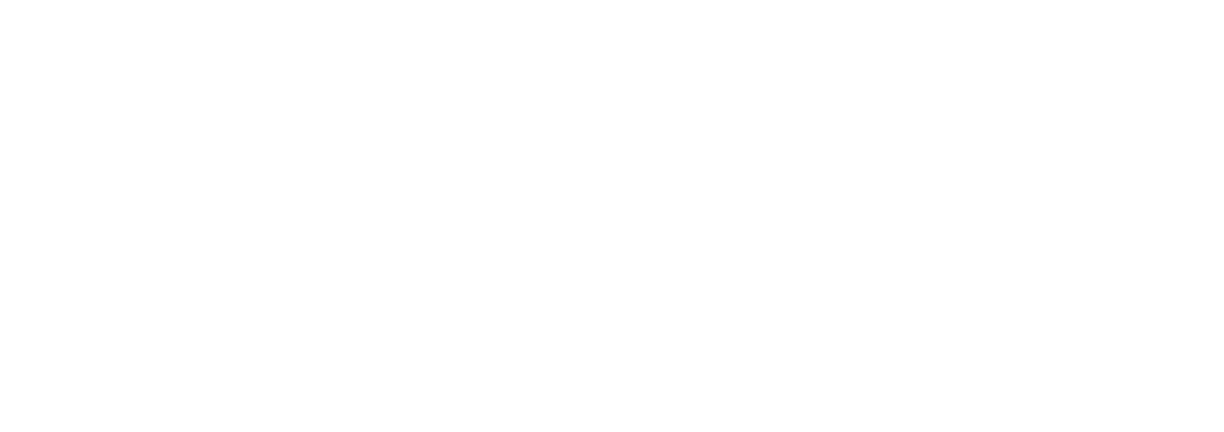