By Bruce Geiselman
President Biden, who ran on a platform that included green energy, has unveiled policies to increase the sales of battery-powered electric vehicles (EVs), creating new opportunities for the plastics industry.
The Biden administration announced a goal for clean energy vehicles (including battery electric, plug-in hybrid electric, and fuel-cell electric vehicles) to make up 50 percent of all vehicles sold in the United States by 2030. In a Sept. 14 announcement, Biden said his goal was shared by automakers and autoworkers.
Alan Amici, president and CEO of the nonprofit Center for Automotive Research (CAR), called the president’s goal aspirational but achievable with proper incentives.
The Biden administration said the president’s economic agenda, including “Made in America” policies, has spurred domestic manufacturing of EVs, EV chargers and batteries. The Inflation Reduction Act (IRA) includes incentives that make new and used EVs more affordable for consumers, according to the administration.
According to the administration, Toyota, Honda, Ford, General Motors and Panasonic have announced investments in EV-related manufacturing facilities in North Carolina, Michigan, Ohio, Missouri, Kansas and elsewhere.
Laws boosting EVs include:
- The Bipartisan Infrastructure Law, which invests $7.5 billion to build a nationwide network of 500,000 EV chargers around the country. The measure also contains more than $7 billion in funding through the Department of Energy to support an end-to-end domestic supply chain for critical minerals and other components necessary for domestic EV battery manufacturing.
- The Inflation Reduction Act, which provides incentives for buyers of new and used EVs and credits to help manufacturers retool existing facilities and build new manufacturing facilities in the United States.
- The CHIPS and Science Act, which invests in building domestic capacity for the semiconductors necessary for vehicles.
- The federal government also is increasing the number of EVs it purchases. In 2020, less than 1 percent of new federal vehicle purchases were electric. That number has increased under the Biden administration, which has stated a goal of by 2027 purchasing 100 percent zero-emission light-duty federal vehicles.
The Biden administration’s goal of about 50 percent EV sales by 2030 is more aggressive than most industry forecasters, who believe EV sales might make up a little better than 30 percent of vehicle sales by 2030, Amici said.
However, Amici said federal funding to help build charging stations around the country could help spur sales by reducing so-called “range anxiety” among potential EV buyers. As part of the infrastructure law, the government has allocated $5 billion to be allocated to the states for installing EV charging stations along alternative fuel corridors across the country.
“These would be, generally, the major highways in the state,” Amici said.
The plan is to ensure that a DC fast charger is available every 50 miles along these highways. Most EVs now are advertising a 300-plus-mile range on a full charge, he said.
“This is not the end solution, but this was the government’s way of priming the pump and getting the infrastructure up and running,” Amici said. “I think range-anxiety concerns can be reduced with the build-out of the EV chargers, which will accelerate EV sales.”
The law also provides $2.5 billion for communities and corridors through a competitive grant program that will support innovative approaches and ensure that charger deployment meets administration priorities such as supporting rural charging, improving local air quality and increasing EV charging access in disadvantaged communities.
Also important for helping boost the sales of EVs is addressing buyers’ price concerns. EVs are generally more expensive than comparable vehicles with internal combustion engines (ICE).
The IRA offers incentives of as much as $7,500 for buyers of qualified EVs with final assembly in North America. Numerous other requirements dictate the amount of an incentive. Plug-in-America, a non-profit advocacy group, has created a webpage that explains the guidelines.
“Certainly, the IRA offered incentives for EV sales based on U.S. manufacturing,” Amici said. “There was a $7,500 credit; that goes a long way to reducing the price gap between EVs and internal combustion engines. So, with those things in place, 50 percent market share by ’30 is, I think, achievable. It’s certainly aspirational, but I think it’s achievable.”
What it means for the plastics industry
The transition to EVs creates new opportunities and challenges for the plastics industry because reducing the weight of parts is more important than ever, and EVs require plastics with different properties.
“Electric vehicles are significantly heavier than their internal combustion engine counterparts,” Amici said. “This is primarily due to the weight of the battery. These batteries are 70 to 90 kilowatt hours. They're large batteries; they're very heavy, and that’s a significant increase in weight in vehicles … A lighter vehicle, all things being equal, can get better fuel economy, and it’s the same thing with an EV. A lighter vehicle, all things being equal in terms of battery size and such, can get better range.”
Research is going into high-performance resins and plastics that can replace aluminum or other metals.
In addition, EVs have more numerous and larger electrical connectors than ICE vehicles because the electrical systems carry more current and at a higher voltage.
“Traditionally, you and I drive with 12-volt electrical systems in our internal combustion engine cars,” Amici said. “The EVs on the road today, the first generation are 300 volts, but most automakers are looking at even 800 volts and in the future going up to 1,000 volts. This is a challenge to the plastics industry because the electrical connectors have to change, and the electrical wiring has to change.”
The increased voltage generates higher temperatures, and that means higher-performance plastics are necessary for the connectors.
“These plastics have to be designed that can handle higher temperatures so they don’t warp and mis-shape at higher temperatures, but they still have to have the salt-spray durability and sealing capabilities that they’ve always had,” Amici said. “This is a challenge where connector companies are looking at new higher-performance materials from resin suppliers — different polymers that can withstand the higher temperatures.”
Another change Amici has observed is the need to use plastics that can shield electromagnetic interference (EMI).
“The high currents running through the wires and connectors going from the battery to the motor create electrical noise,” Amici said. “You can think of this on your AM radio when you have excessive static. If the noise is strong enough, it can interfere with communications in the car and can even affect performance of certain components in the car. So, automakers have to come up with countermeasures to suppress or shield the rest of the vehicle from this electromagnetic interference.”
Typically, a metal shroud or metal harness might be used to address EMI, but automakers now are developing conductive polymer composites to act as an EMI shield that can perhaps reduce costs and weight, he said.
Sustainability concerns fuel change
Automakers also face pressures to reduce the weight of ICE vehicles due to tightening Corporate Average Fuel Economy standards.
Standards adopted last year require an industry-wide fleet average of 49 MPG for passenger cars and light trucks in model year 2026, increasing fuel efficiency by 8 percent annually for model years 2024 and 2025, and 10 percent annually for model year 2026, according to information on the National Highway Traffic Safety Administration website.
The Biden administration is likely going to propose even more stringent standards for coming years, said Brett Smith, a CAR research fellow.
Plastics offer opportunities to reduce mass and consolidate parts, which is a further advantage to automakers, Smith said.
However, plastics processors could face challenges as automakers increasingly seek to make their operations more environmentally friendly and sustainable, feeling pressure from customers and shareholders. That includes reducing greenhouse gas emissions during manufacturing and ensuring that materials in cars can be recycled.
In an effort to improve sustainability, companies also are looking at ways to make composite plastics out of things other than petroleum-based products. Manufacturers are beginning to look more seriously at using bioplastics and recycled plastics.
“I raise this not as a today thing,” Smith said. “I think it is absolutely something that the car companies are talking about and are trying to understand … There are several companies where it has made it into their business plan, but most companies are still trying to figure out how to rate it on a scale of importance.”
Bioplastics are not new. They have been around for decades. However, concerns exist about taking potential food crops and using them to make bioplastics. So, a lot of attention right now is being focused on recycling plastic already in cars, Smith said.
Bruce Geiselman, senior staff reporter
Contact:
Center for Automotive Research, Ann Arbor, Mich., 734-662-1287, www.cargroup.org
Bruce Geiselman
Senior Staff Reporter Bruce Geiselman covers extrusion, blow molding, additive manufacturing, automation and end markets including automotive and packaging. He also writes features, including In Other Words and Problem Solved, for Plastics Machinery & Manufacturing, Plastics Recycling and The Journal of Blow Molding. He has extensive experience in daily and magazine journalism.
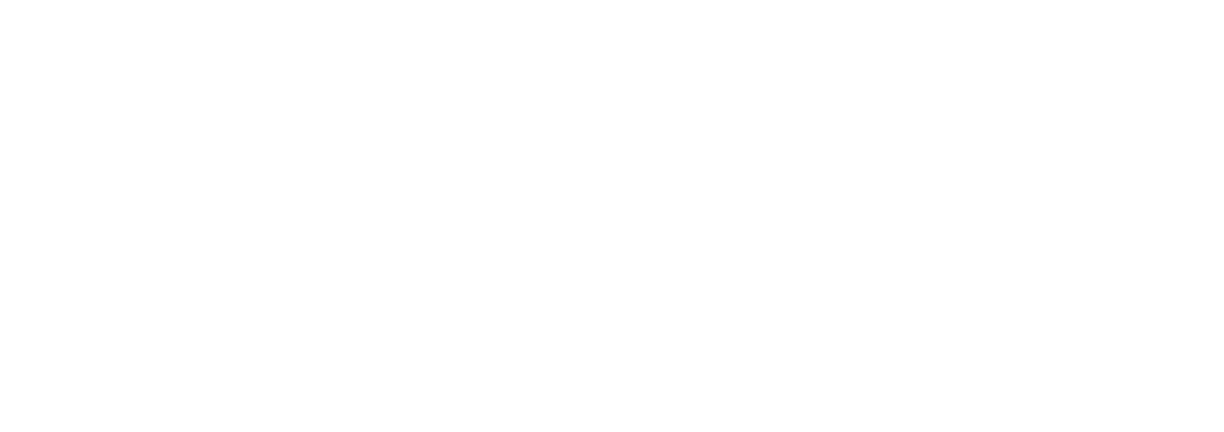