By Karen Hanna
A concert series. Company housing. Free meat. Paid training. The chance to see leaders as peers, and the opportunity to grow into their positions.
For mold building company Westminster Tool and plastics processor Monoflo International, there’s a lot more to employee perks than salaries and PTO, as representatives of the two companies told participants at the Nov. 16 “Developing and Retaining Your Skilled Talent” webinar hosted by Plastics Machinery & Manufacturing, now available on demand.
“Every single company out there needs to stay competitive,” said Hannah Coombs, talent development manager at Westminster Tool in Plainfield, Conn. “We, as a company, owe it to our employees to be as competitive as possible with our benefits. ... But at the same time, yes, we’re competitive, but it’s not a differentiator.”
New eBook: Plastics and the Labor Crunch, Part 1: Causes and Solutions
Over the last 10 years, Westminster Tool has undertaken a project to transform its culture, from a company that touts experience and expertise, to one that embraces collaboration and continuous learning. Along the way, Coombs said, it’s changed the look of its own workforce — from one that was heavily dominated by white men with an average age of about 50, to one that’s a mix of women and men, with an average employee age in the 30s. About 90 percent of its 40-some employees come to the company with no prior manufacturing experience, she said.
To develop its workers, Westminster Tool works with an array of community partners, including high schools and community colleges, and it’s created its own in-house Westminster Academy, with more than 8,000 lessons and 60 career paths, Coombs said.
Ben Waterman, business development manager at Monoflo, headquartered in Winchester, Va., said employee development is important to his company, too.
“Our goal is to identify individuals with relevant interest and aptitude. We’re going to create an environment that fosters growth and retain skilled talent to contribute to the development of future talent,” he said.
Like Westminster Tool, Monoflo has invested in programs to grow its workforce, by developing its own academy, Plastic Injection Molding Academy, also known as PIMA, and partnering with Paulson Training Programs Inc., Chester, Conn. Paulson sponsored the Nov. 16 webinar.
It even offers housing to interns.
But, as its workforce has aged, Monoflo realized it had to do even more — “to make a world-class effort to be a good employer and retain and grow folks,” Waterman said.
To that end, it has put a lot of emphasis on a perk not typically associated with the bottom line: Fun.
“We’re going to build a strong sense of community, we’re going to deliver employee perks, and we’re going to show employees recognition,” Waterman said.
Among other things, Monoflo sponsors a company picnic, holiday parties, monthly happy hours and a raffle of meat it purchases at the county fair.
Its signature event is a concert series open to the community, with free admission and concessions available for employees.
Waterman and Coombs acknowledged their companies’ decision to embrace culture change hasn’t come without cost. At Westminster Tool, which put off capital purchases for five years to invest in employees instead, workforce-development costs over the past decade have exceeded six figures.
But, amid hiring challenges, Waterman said the cost of doing nothing is even higher.
“We really looked at, how do we elevate our group of folks manufacturing and conducting our business? And the cost of failure was far greater than anything we could be spending. [We] kind of used it as a justification without necessarily pinpointing an ROI,” he said.
“We were spending money to recruit talent. Now, we have a waiting list that at any time of the year will have around six to eight employees, six to eight applicants,” Coombs said.
The presenters agreed their companies’ transformations won’t stop. Westminster Tool would like each of its employees to be cross-trained in at least two other areas — it’s not there yet, Coombs said.
Neither is Monoflo in reaching its goals, Waterman said.
Both he and Coombs said continuous learning and improvement are essential to the way their companies do business.
“I’m really thinking even as we look towards next year, we’re going to continue to look at this and grow it and not rest on our laurels,” Waterman said.
Karen Hanna, senior staff reporter
Karen Hanna | Senior Staff Reporter
Senior Staff Reporter Karen Hanna covers injection molding, molds and tooling, processors, workforce and other topics, and writes features including In Other Words and Problem Solved for Plastics Machinery & Manufacturing, Plastics Recycling and The Journal of Blow Molding. She has more than 15 years of experience in daily and magazine journalism.
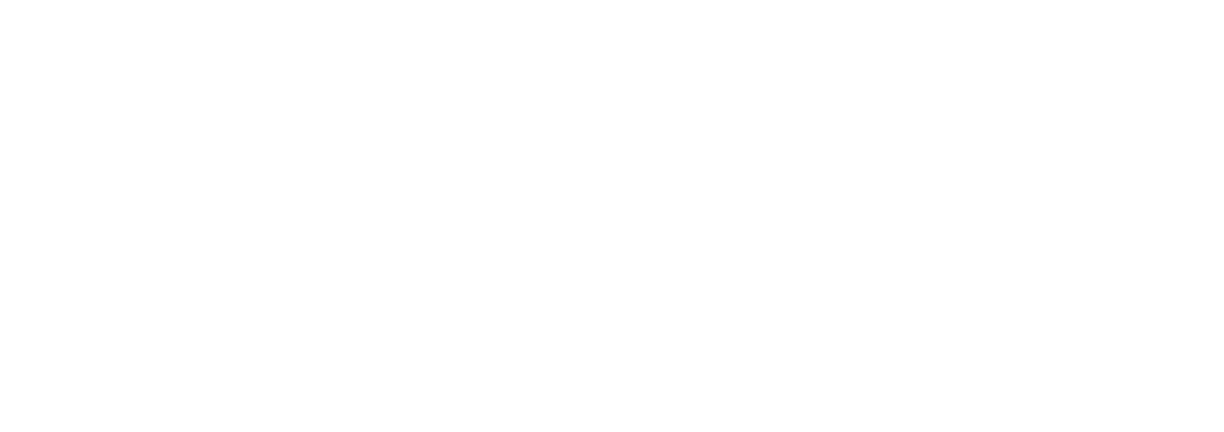