By Karen Hanna
According to a U.S. Bureau of Labor Statistics study, an average person born in the baby boomer era will have more than a dozen jobs over their lifetime. But Ron Hertzer isn't average. He’s had three jobs since college, and in his fifth decade working for Milacron, he’s in no hurry to fully retire. He’s having too much fun. Now a technical adviser, Milacron’s former director of new product development recently spoke with Plastics Machinery & Manufacturing Senior Reporter Karen Hanna.
What’s your current role with Milacron?
Hertzer: I officially retired from full-time work last April 2021, I work, 15 to 20 hours a week. In terms of product design and implementation, the first stage is ideation. The second stage is a business case justification and the project details. I am involved with new forward-looking projects that fall into these first two stages. Once a project is justified or moving on into the implementation phase, I move on to other projects.
Why continue working at all?
Hertzer: I enjoy work. I enjoy all the people I work with, All the bosses I have had — or at least 90 percent of them — have given me a hands-off approach and listened to my ideas. Now, since I'm working part time, the work I am involved in — getting a project going and figuring out the details and getting it on its way — it's probably the most satisfying part of what I did. And that is now all I do!
How did you get your start in the plastics industry?
Hertzer: When I was in high school — I am from Cleveland — the father of a good friend of mine went to UC [the University of Cincinnati]. My dad was a CPA, so it was a choice between accounting and engineering. I like mathematics and practical stuff. I did not intend to get into plastics. I went to the University of Cincinnati (UC). I was part of a co-op program. So, I had a lot of experience designing parts; every other quarter, you'd work in a plant. I took a lot of interest in control theories, things, like how ABS brakes work to eliminate skidding. I am a hands-on person. I enjoy working on cars, building things, woodworking. My first job was with a company called Hunkar Labs in Newtown, Ohio, that built retrofit controls for injection molding machines. My first job was as a field installation engineer. I’d go in and install controls and get them started up and running. That is where I became involved in and learned how to mold parts, learned about machinery, and learned how to apply control theory, the practical aspects of it.
What brought you to Milacron?
Hertzer: I have worked for three companies since 1975. I worked at Hunkar for about a year and a half, then I got married. If you are 100 percent on the road, that does not work well for a marriage. So, I got a design job at Empire Products designing electrical connectors. I enjoyed that, but it did not have the excitement of travel, troubleshooting problems with machines, collaborating with customers and those kinds of things. So, the first job I took [at] Milacron was in the application/testing group. That really was the job that had the excitement of field travel and collaborating with customers, and I got to stay at home for the most part. You'd look at a part and then you’d recommend a machine configuration to the customer. There was some troubleshooting of processes in the field. And then there was in-house testing. The way my job was organized, which was great, 30 percent [of the time] you weren't really assigned tasks. You could use this time to investigate or run tests In addition, [there was] customer support and sales support for applications, so it was the perfect job.
How many patents are in your name?
Hertzer: I looked that up because I did not know. I have one from the job I had at Empire Products for an electrical connector, and then I have five here at Milacron.
Is there one that particularly stands out?
Hertzer: Probably the one that had the biggest impact on the industry or became adopted as the norm is the application of servo motors to drive hydraulic pumps. My name was the lead name [on the] Milacron patent on the application of servo motors, with variable displacement pumps to the injection molding machine. We ended up near the end licensing other people to utilize that patent. Today, virtually every hydraulic machine is driven by a servo motor. They used to all be induction motors. The efficiency has gone [from] maybe 1 kWh [kilowatt per hour] per pound of material to now it's tenfold, like 0.1 kWh per pound.
When was that?
Hertzer: That patent was granted in 1991; the patent has since run out. It’s since evolved. I've worked on improvements, too, that further improve efficiency and reliability. Currently, we use a different type of servo motor, and more efficient internal gear pumps.
You've been in the industry 43 years. What are the most exciting advances you've seen in that time? And what advances still await? Any big changes?
Hertzer: It's incremental on the software side and the machine design side. It's very mature. In terms of the machine design, I'd say the clamps have evolved, from full hydraulic machines and hydraulic toggles, to now they're all electric toggles, or very compact two-platen machines. Most machinery manufacturers including Milacron, have a variation of these two clamp types. In terms of injection unit, the feed screws have evolved from a basic 10//5 standard screw to some variation of a barrier screw. The injection pressures have all gotten higher. I'd say the materials have gotten easier to process, and the parts are lighter. In most [machines], they have gone from hydraulic vein motors to piston motors or electric motors on the extruder axis.
As technology has been applied to machines, they have become a lot faster, more repeatable and more compact. And they are also more complicated. In 1980, the machines had relays instead of computer control. They had manual flow control instead of proportional valves. The machines are very refined and stable, and they've become smaller and smaller with evolutionary improvements.
In terms of what is coming, in the industry, including here at Milacron, there is a shortage of qualified engineers or technicians that are interested in this kind of thing. I think the application of AI [artificial intelligence] to stabilize the process or help with setup wizards and other advanced control features for our customers, where they don't have trained technicians, that allow them to get to good parts faster, and then maintain that part quality, is where things are evolving.
The other impact is government regulations. I think how the industry or how the machines evolve relative to government regulations for recycling is what's going to impact the design. And the other is the impact of automotive MPG requirements driving the increased use of carbon fiber and composites and other plastics to reduce weight.
You’ve been at Milacron since 1980. What made you stay so long?
Hertzer: I think camaraderie and support for management and just the general work environment. I think that's unique at Milacron, there are a lot of people here — even the young people today — you come here to Milacron, and it's a very good place to work.
Any advice for what employers can do to encourage that kind of longevity?
Hertzer: I think companies need to focus more on promoting from within. Maybe not Milacron, but in general, I think there's so much pressure that people burn out and then move to another job to get a promotion.
Milacron allows [people] like me to mentor other people. That is important. There are places, plants I've been in, where there's kind of a mentality that the workers should keep to themselves, work just on their own productivity and not be helping the guy next to him. I think that is not good. The older people need to bring the other younger guys along, teaching them the trade in whatever they are doing.
What advice would you give to younger engineers?
Hertzer: The first one would be to listen and understand where your predecessors went before you, what worked and what did not. Do not get set in your ways and be open to change. If some new technology comes along, or some supplier comes in pitching some idea, don't just throw it out. We really need to be open to new technologies and new ideas because what may not have worked four years ago, it might work great now. So, you really need to be open to new ideas.
And — this isn’t the current thinking — you need to put in the time to get better. Both my kids are workaholics, like I am, but I think a lot of their friends are not. They do not just put the job first.
When you're working, you need to be honest with yourself and have some integrity. Be honest in what you think and do. And then speak up if the company's going on the wrong track, in a professional way. You don't want to design yourself over a cliff.
If somebody is a new worker, if you are going to work every day, and it's a drag, you need to probably find a different job or do something that really sparks your interest, [that is] fun to do. It can be hard work and stressful and all those things, but you need to enjoy what you're doing.
A lot of times, engineers aren't good at writing stuff down, so when they leave, that information is gone forever. It is important that new engineers learn how to document what they know.
How have the tools you use to build machines changed over your career?
Hertzer: When I started in engineering, we used a slide rule and a drafting board. We didn't even have simple calculators. A lot’s changed. Now, everyone's got a laptop.
It sounds like it’s a lot easier to be a young engineer today.
Hertzer: Well, it's probably harder because you don't learn the principles. I kind of think of myself as maybe a little intuitive. If you know the principles, as opposed to just entering the data in a computer, I think that helps you get to the solution quicker.
What do you think of the state of injection molding today?
Hertzer: A lot of this manufacturing in the U.S. [has] moved offshore and probably not coming back because of the environmental restrictions here that other countries just don't follow.
How long might you stay in your part-time role?
Hertzer: I'd say until it's not fun anymore, so, there's no defined finish date. It's still fun.
What do you like to do in your spare time?
Hertzer: I enjoy woodworking and biking. Since I have retired, I’ve redone the kitchen. I joined two golf leagues, and then I have an old 2001 Audi TT that I am slowly bringing back to new.
I’m probably spending more time with the family now. I have two children, a son and a daughter, and then I have four grandchildren. All of them live here in Cincinnati, so we get to spend time with them.
What would you like your legacy to be?
Hertzer: On a personal basis, it is the work ethic my wife and I instilled in our daughter and son. They both work hard; they enjoy work. From a professional standpoint, firstly, all the injection machines [from Milacron] have my stamp or my influence on the design. And I'd say the work I've done on servo hydraulics and process controls utilized in Milacron machines are probably the legacy; it's going to live on in the machinery itself.
JUST THE FACTS
Who is he? Ron Hertzer
Title: Technical adviser, Milacron LLC
Age: 72
Education: Degree in mechanical engineering, University of Cincinnati,1975
Karen Hanna | Senior Staff Reporter
Senior Staff Reporter Karen Hanna covers injection molding, molds and tooling, processors, workforce and other topics, and writes features including In Other Words and Problem Solved for Plastics Machinery & Manufacturing, Plastics Recycling and The Journal of Blow Molding. She has more than 15 years of experience in daily and magazine journalism.
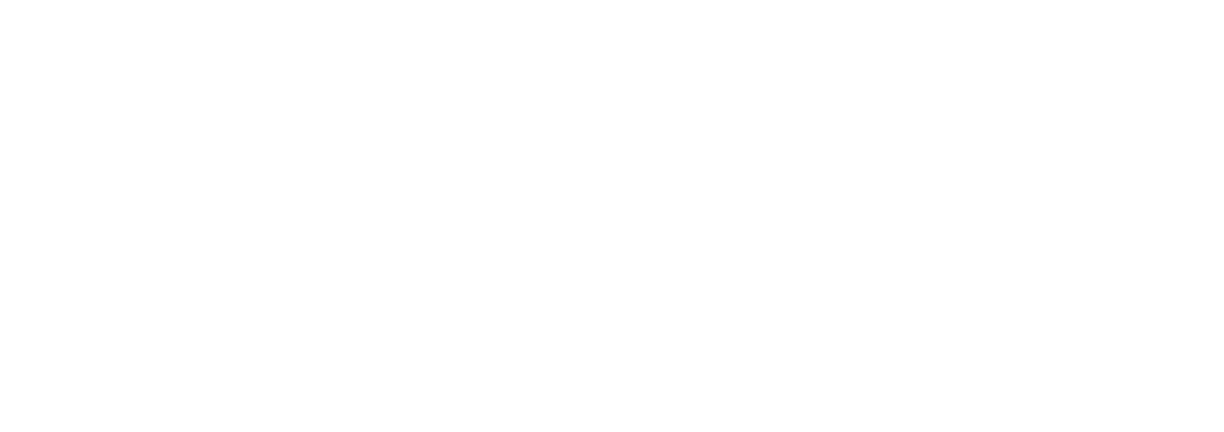