By Karen Hanna
Smart functions designed to send your injection molding machine (IMM) to the head of the class were among the highlights at the K Show, where innovations in software vied for attention alongside hardware upgrades.
Among IMM makers touting intelligent machine functions were Haitian International, Arburg, Sumitomo (SHI) Demag and Engel.
Haitian shows Smart Solutions
Under the motto "Smart Technologies, Flexible Integration, Sustainable Solutions,” Haitian exhibited for the first time Haitian Smart Solutions and its intelligent machine functions that enable plastics processors to better integrate their equipment and achieve greater efficiency. Leveraging software that makes sense of data from sensors, the company’s smart functions include energy management, process optimization, plasticizing efficiency and clamping force optimization.
“Haitian International — both Haitian Plastics Machinery’s servo-hydraulic molding machines and Zhafir electric molding machines — have settled on a flexible approach to smart molding. Haitian’s philosophy is dictated by its global footprint and high volume of machine sales,” Marketing Coordinator Ben Hartigan said. “The result is a molder-friendly machine that adapts to a wide range of smart molding approaches.”
According to a press release, the innovations all attest to Haitian’s vision. “Haitian International’s declared goal: To offer smart features as a standard feature at no extra charge,” it states. Among other benefits, the company’s latest technologies simplify integration with manufacturing execution systems (MES) and Industry 4.0 platforms, and improve energy efficiency.
The company boasts that its innovations offer flexible integration, standardized interfaces and open system integration, giving Zhafir and Haitian users wide latitude in their choice of machine controls and integration partners. Users can integrate lines into their MES platforms, regardless of the manufacturer of their auxiliary equipment, Hartigan said.
“It is as simple as taking an Ethernet cable from the machine right to their computer or server or whatever they are using to collect data. We don’t believe in forcing customers to use a specific MES system. Let them pick their own MES system and then work with us. It is what we call common sense connectivity," he said.
One variable in the sights of smart molding applications is energy consumption.
Available on new IMMs beginning this year at additional no cost, Haitian’s new Energy Control 1.0 uses a combination of sensors and software that allows molders to understand and control their machines’ energy usage.
With the feature, molders have access to real-time energy consumption data and analysis, and can see the impact adjustments to machine settings have on energy usage. “For example,” Hartigan said, “what happens to energy usage if the processor adjusts the clamp speed by 1 percent?”
This gives molders another factor to consider in evaluating process optimization and plasticizing efficiency, he said.
Arburg's FillAssist gains functions
Arburg, too, continues to make strides in digitization. Among the features it spotlighted at the K Show were the aXw Control FillAssist, which is available on any Arburg Allrounder molding machine equipped with a Gestica control, and aXw Control RecyclatePilot.
In a press release looking forward to the Swiss Plastics Expo from Jan. 17-19 in Lucerne, Switzerland, Marcel Spadini, managing director of the Arburg Switzerland subsidiary in Münsingen, revealed the importance the company places on features such as FillAssist.
He said: “Intelligent injection molding, recyclate processing and the potential offered by digitalization will all be on show for our customers.”
First released a number of years ago, FillAssist continues to gain functionality. The feature is appropriate for any application in which the mold-filling sequence is critical to part quality.
In a K Show exhibit showcasing a 730-ton Allrounder H press, Arburg demonstrated FillAssist using a new plug-in that works with filling-analysis software developed by Simcon kunststofftechnische Software GmbH, Wuerselen, Germany. The plug-in, called Varimos, uses artificial intelligence (AI) to analyze multiple points simultaneously to determine optimal flow design before metal is ever cut to make a mold.
Once the mold is installed on the molding machine, the results of the Varimos analysis can be transferred to the Gestica control and, using FillAssist, the operator can change speed parameters and see within seconds what effects changes will have on filling behavior before molding even starts.
The combination of technologies makes it easier for users to optimize machine settings, so they can transition from designing to molding parts more quickly, shortening development time from several weeks to a few days.
According to an Arburg press release, “Through the cross-linking of the software with the Gestica control system, even more precise machine parameters can be generated during the filling simulation.”
Another Arburg technology, the RecyclatePilot process-control program, enables more-sustainable molding by automatically adapting process parameters to ensure consistent cycling and stable shot weight despite the variability that is typical of recycled feedstock. According to Arburg, it’s still under development.
Sumitomo (SHI) Demag leverages data
Sumitomo (SHI) Demag is taking a multi-pronged approach to improve molders’ insights into the manufacturing process — both literally, with special glasses, and analytically, by leveraging ever-growing streams of data.
At the K Show, Sumitomo (SHI) Demag demonstrated myConnect Basic, now available as standard on all new IMMs and robots from the company, and as a retrofit on NC5 controls. The company also displayed a new version with even more available features, called myConnect Premium, which allows molders to integrate their machines’ HMIs and CPUs with the OEM’s software solutions.
“Using myConnect, customers can access machine documentation online, and our service teams can connect to the machine online to troubleshoot and resolve any technical issues,” said Arnaud Nomblot, director business development packaging, in a press release.
The myConnect Basic version provides access to remote monitoring capabilities, up-to-date documentation about the machine and machine events, and Sumitomo’s service and spare-parts departments.
Optional modules offering users more support and data access are available through myConnect Premium.
Among the latest myConnect Premium modules is mySmartVision, which allows users to tap into live chats with Sumitomo (SHI) Demag service personnel. Smart glasses — a separate purchase — give molders a way to show Sumitomo (SHI) Demag technicians what they’re seeing, so they can solve problems quickly.
The premium version also includes mySupport, an online portal to 24/7 support from Sumitomo (SHI) Demag.
Other modules in myConnect Premium include myApplicationExpert, which provides weekly expert technical support, and myProduction, which allows customers to individually configure how they prefer to record and present production diagram and table data. The myAlarming module allows users to define what machine events trigger e-mail notifications.
A sixth myConnect Premium module, called myMaintenance, provides a structured maintenance management program. It will make its debut later this year.
Engel makes molding more efficient
At the K Show, Engel showed off two features — the ecograph plus and ecobalance — that contribute to more-efficient molding. According to the company, the plus version of ecograph measures the energy consumption of all plant components — including the peripheral units and hot runners — and provides graphics illustrating the situation for users. Based on these values, ecobalance distributes the total power defined for the machine or production cell in question across the injection molding cycle in line with demand.
Together, ecograph and ecobalance help users manage energy peaks and avoid penalties.
Karen Hanna, senior staff reporter
Contact:
Absolute Haitian, 216-452-1000, Parma, Ohio, www.absolutehaitian.com
Arburg Inc., Rocky Hill, Conn., 860-667-6500, www.arburg.com
Engel Machinery Inc., York, Pa., 717-764-6818, www.engelglobal.com
Sumitomo (SHI) Demag, Suwanee, Ga., 678-892-7900, www.sumitomo-shi-demag.us
Karen Hanna | Senior Staff Reporter
Senior Staff Reporter Karen Hanna covers injection molding, molds and tooling, processors, workforce and other topics, and writes features including In Other Words and Problem Solved for Plastics Machinery & Manufacturing, Plastics Recycling and The Journal of Blow Molding. She has more than 15 years of experience in daily and magazine journalism.
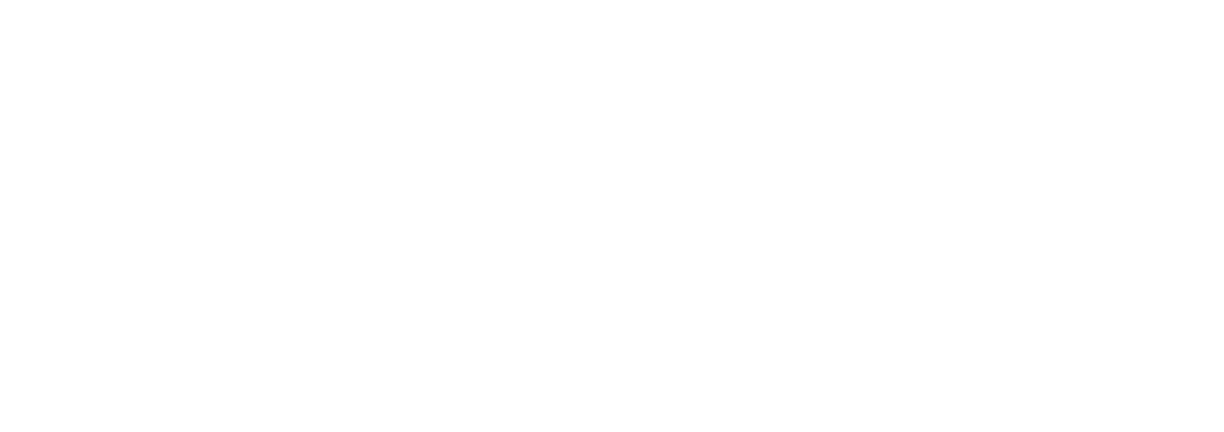