Parkway Products tackles technical deficit with training program
Problem: Plastics processors continue to struggle to fill positions.
Solution: Injection molder Parkway Products has started a companywide training program to develop talent internally.
By Karen Hanna
One number separated the job candidate from the open position injection molder Parkway Products LLC needed to fill:
Seventy-five percent. That was the salary increase the technician accepted to stay with his then-employer, rather than take the job with Parkway.
In what Amber Galford, Parkway’s chief human resources officer, calls a dog-eat-dog world for landing new, technically proficient workers, the company has sometimes found itself holding the bag. With the U.S. Bureau of Labor Statistics reporting 834,000 unfilled manufacturing jobs as of the end of July, the company’s experience is not unique.
But, Galford said, the Greenville, S.C.-based company is now cultivating a path toward growing its own talent. In January, with the approval of CEO Andrew Green, who’s been on the job about two years, the company began offering Paulson Training Programs classes to all its of employees.
“Somebody walks out the door, and you don’t have somebody on the bench, all of a sudden you look around and say, ‘Oh, well, OK, you, you’ve got a little bit of technical aptitude, let’s grab you.’ Now, we’re building this bench of people that we’ve identified that have that technical aptitude, which is important,” she said.
The company, which employs around 750 to 800 people, has had as many as 50 open positions at a time, but recently, it’s had better luck filling entry-level jobs, which account for about 75 percent of its workforce. That’s left fewer open positions — about a dozen, as of early September — but they’re the tech-intensive roles essential to plant success. In bidding wars, companies like Parkway are shelling out big premiums to lure skilled workers, Galford said.
In-demand positions include people with backgrounds in processing, mold setting, maintenance and engineering.
Growing from within
Over about the last 15 years, Parkway has grown both internally and through acquisitions from a manufacturer with about 100 employees and a laser focus on automotive parts, to a diversified company with about $135 million in annual sales, Galford said.
Its biggest customers now include buyers of agricultural products, as well as meter covers for the utility industry. At its 10 manufacturing plants in the U.S. and Mexico, workers fill a variety of roles from running injection molding machines (IMMs) to assembling parts. IMMs with clamping forces ranging from 17 to 1,760 tons handle everything from high-performance polymers to thermosets.
In assessing the workforce, Galford recalled thinking, “Can we take our current team and really help them rise far above where we’ve ever given them the opportunity for from a knowledge standpoint?”
Students develop a shared language, said Michelle Parr Paulson, director of marketing communications for Paulson Training Programs.
“Say you’re working in a company like Parkway Products, wouldn’t it be wonderful if you’re in the front office, and you’re talking to one of your customers? Wouldn’t it be wonderful that you have a good legitimate knowledge of the plastic, the processing and what your company actually produces?” Paulson said. “You can speak the language and be intelligent about it.”
Getting technical
Paulson Training Programs’ portfolio includes classes that are relevant to roles and positions throughout Parkway, Galford said, but, with the need for developing technically proficient workers, an offering called the Technology of Injection Molding Series (TIMS) has taken special prominence.
She said Parkway officials already are taking notice of workers who have developed new skills. She recounted a recent meeting:
"The plant manager talked about one of their technicians, and just what a different tech he was, since he’s gotten this formal training, and he said, ‘You know, there’s a prime example of a guy that wanted to do the right things, cared about his job, we just really hadn’t gotten him the proper training up to that point.’ And it wasn’t that we didn’t want to train him. It’s that we have been chasing our tails so much on labor, like everybody else in this industry, that we neglected some of those key areas that we’ve gotten back to and really focused on.”
TIMS is a series of three online, self-guided courses that build upon each other. Each has specific lessons followed by tests, and each lesson includes a set of active lab lessons in which students interact with a virtual molding machine, a vendor-neutral simulator called SimTech, to tackle pre-determined molding problems or scenarios. Together, the lessons and interactions with SimTech reinforce to students how plastics responds to heat, flow, pressure and cooling.
Level 1 builds a foundation for students, but the series of courses presents more complex issues as students move on
Level 2 teaches skills to help students optimize the molding process.
“Level 3 is definitely far more technical. … It’s got a lot more science involved, a lot more math involved,” she said.
The point is to drive home to students the reasons why certain settings might yield certain results.
Ultimately, learning the physics behind plastics processing is a more efficient and faster way to develop technical proficiency than simply shadowing — or trying to copy — someone else on the plant floor, both Galford and Paulson said.
“If you can get your processing under control, you know that piece of it, have it tightened up and [you’re] understanding your parameters and in your guys, knowing not just turning knobs, but understanding what knobs are turning and why they’re turning them or when not to turn them, those are the things that really elevate your business, and you start producing good quality parts that you can ship the first time,” Galford said.
By understanding how plastic works, employees also can optimize the amount of resin they use, Paulson said.
“When you go through training, and you understand this, you are going to use less plastic, too. You’re not going to create as much waste. That is significant, I think, because as we all know, prices are rising,” she said, adding that companies can benefit, too, from showing their commitment to the environment.
While the particular offerings Parkway opted to offer its employees fall under the heading of Paulson University, Paulson Training Programs offers a variety of plastics-related curriculum packages in online and in-person formats. Its portfolio of classes help plastics professionals understand the science of how plastics work, and
deal with many major plastics processes, in addition to injection molding. Most recently, it added offerings for injection stretch blow molding PET parts, and, in addition to the SimTech IMM, it is developing a SimTech simulator for extruders.
Changing culture
Paulson said the skills gap has driven companies to invest in training.
“The drumbeat continues that there is a challenge in developing a workforce and finding people. That is a challenge,” she said.
Attracting and retaining workers will remain a challenge, said Galford, who conceded that, in training workers, companies expose themselves to making investments in people who might ultimately leave. But the risk — and the rewards — are worth it.
“We have found that, when you truly invest in people and you treat them right, you have to pay them fair, once you’ve invested in them and do the right things, then you have something that is an asset in this person that’s worth X amount of dollars,” she said. “You have to be willing to do that. You have to be willing to understand the market and treat people right.”
To incentivize its workers, Parkway is offering pay raises and promotions to workers who take on classes and demonstrate proficiency. For their part, workers are showing enthusiasm for the opportunity. Whether they grow into new roles at Parkway, or even somewhere else, Galford said offering the training is the right course of action.
“If you’re doing your job as leaders and you’re preparing the organization for those changes, you don’t have to hit the panic button,” she said.
With training, replacements already are in the pipeline.
Karen Hanna, senior staff reporter
Contact:
Paulson Training Programs Inc., Chester, Conn., 860-526-3099, www.paulsontraining.com
Karen Hanna | Senior Staff Reporter
Senior Staff Reporter Karen Hanna covers injection molding, molds and tooling, processors, workforce and other topics, and writes features including In Other Words and Problem Solved for Plastics Machinery & Manufacturing, Plastics Recycling and The Journal of Blow Molding. She has more than 15 years of experience in daily and magazine journalism.
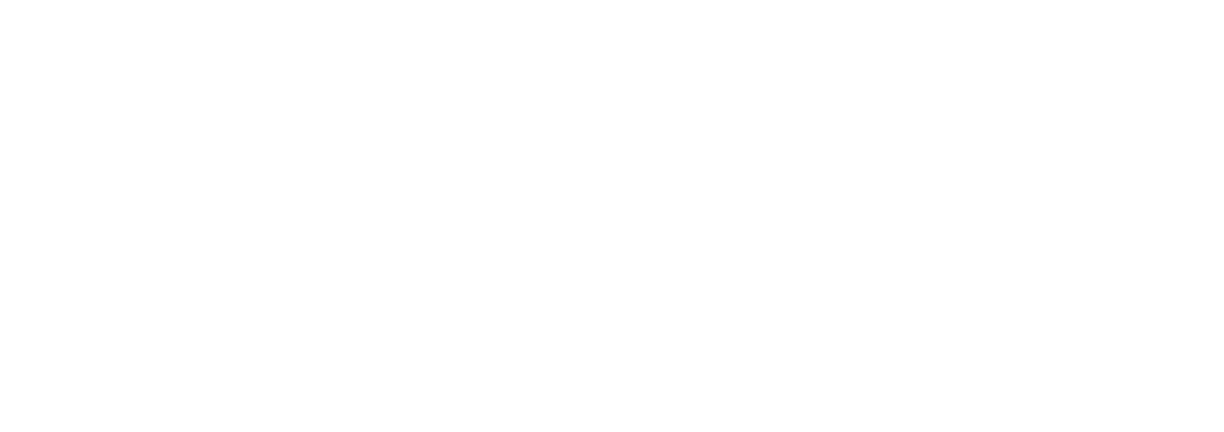