Switch to predictive maintenance enhances molder's efficiency
Problem: An injection molder of containers needed to gain better control over machine downtime.
Solution: Milacron’s M-Powered Solutions suite of monitoring devices and cloud-based services leverages machine data to spot component wear and other problems.
By Karen Hanna
The little icons on a car’s dashboard that warn of low tire pressure or a missed oil change can alert drivers to small problems that can escalate into anxiety-producing, stranded-on-the-freeway moments.
As motorists know, preventive maintenance can be the best medicine. For companies that make plastic parts, the mission to keep machines running and avoid downtime is no less urgent.
“The goal has always been to give us a ‘check engine’ light for our injection molding machine similar to your car. When my truck tells me my left front tire is under pressure, I can fix the issue and monitor it, if necessary, to see if there is a larger issue prior to having to replace the tire,” said Hank Fuller Sr., a manufacturing engineer at Oconomowoc, Wis.-based Orbis Corp.
Orbis, which makes plastic totes, pallets and containers, has been enjoying the benefits of its drive to leverage data to put the brakes on downtime, using Milacron’s M-Powered Solutions suite of equipment-monitoring services. The system, designed for use by both injection molders and extrusion companies, scores the conditions of the machine components it monitors, and issues alerts to users when the scores decline below the thresholds they set. Upon receiving an alert, users can replace the components or work with Milacron technicians via remote connection to troubleshoot the issue.
Along with other strides in advancing its proactive maintenance program, Orbis has recently taken a deep look at the health of its pumps, feedscrews and screw tips.
“Orbis was the first partner that had the same vision for IIoT as Milacron,” Edward Jump, M-Powered IIoT digital analytics leader, said in a case study provided by Milacron. “Machine data provides a detailed list of tasks that need to be done and why. Not only are you preventing unplanned stops, but you are more effectively utilizing your labor and workforce. We’ve made a lot of progress, and we’re still not done yet.”
He acknowledged that making the transition from reactive to predictive maintenance requires adopting a new philosophy. In its journey, Orbis has been “ahead of the curve,” he said.
“I think the process of shifting a mindset from being able to plug in and gauge — which is what a typical maintenance staff is used to; you plug a gauge, you see something on the machine that can tell you how this thing is performing; it can also point to part failures — when you shift that to, ‘I’ve got a bunch of zeros and ones now telling me the same information,’ it’s a mindset shift. ... It’s a culture shift. As we shift generations of technicians, of maintenance staff, within the industry, we see some of that resistance starting to pull away,” Jump said.
A heater-band study — begun in 2019, just two years after Orbis began implementing M-Powered Solutions — illustrates the value of the company’s partnership with Milacron.
First, as part of an audit of downtime issues, Milacron and Orbis worked to develop hypotheses around machinery efficiency to streamline preventative maintenance using M-Powered tools. They based their ideas on information collected from Orbis’ machines by Milacron’s data-collection devices, as well as on the observations and experiences of Orbis technicians; meanwhile, Milacron worked on algorithms to score the condition of various machine components.
To test the condition scores Milacron developed, the team turned its focus on heater bands — components that are often overlooked until they stop working.
In one instance, Orbis realized that two barrel zones had begun expending more energy per shot, totaling an additional 0.52 kilowatt per hour. Based on that observation, Orbis replaced the associated heater bands, allowing the company to save about $58.60 per day, due to improved energy efficiency, and reductions in downtime, labor requirements, and scrap.
Improving heater-band maintenance has been just one target of Orbis’ machine-monitoring efforts.
Along with other components, Orbis is studying its oil use and working to develop ways to predict pump failures. In addition, M-Powered developers are creating a program that would allow users to set up automatic shipments of spare parts based on the data they’ve collected regarding the longevity of specific components.
“When we start to get to data analytics, the sky's the limit as far as what we're potentially capable of,” said Bob Mobley, Milacron’s director of marketing and innovation. “And it's really, how much data can we get? And how can we view that data? And use predictive analytics to help us interpret the data to provide solutions?”
With the data, companies can increase machine uptime and ensure the efficiency of resource deployment, including labor. It can even help them compensate for worker shortages, ensuring that they’re able to use skilled maintenance staff as productively as possible.
“Not only do we provide predictive services, we also have smart maintenance tools that help you even on the preventative side,” Jump said. “We have people working the help desk here that can connect into machines remotely and help with downtime issues. So, as people do have that labor shortage and they're trying to keep the machines running — they have to get the same amount of product out with less people — we do see a combination of the predictive maintenance or preventative tools that help customers maintain the machines at the right point in time.”
Along with Mobley, Jump believes there’s still a lot of potential for predictive maintenance, even among companies, like Orbis, that have bought into the approach.
“How can we now use the machine data to tell you when to act upon that those same things that you were doing on that routine basis or waiting till it broke in the past?” Jump asked. “So, when you think of things like cylinders, valves, just to name a few, there's a lot of things on the machine that we are going to tackle in the future that we think the data can help us point to the whole-machine aspect, and not just the individual ones we focused on at this point.”
While reducing downtime has been Orbis’ focus, the company also been able to gain insight into resin consumption and waste, Fuller said.
“It became evident as we collected additional data, that we could infer waste from our studies and in turn figure out which machines/molds are contributing towards our scrap rate to help us to continue to minimize scrap in our processes,” he said.
He said he believes Orbis’ transition to a proactive maintenance approach has only just begun. He believes the company will continue to unlock the benefits of being able to monitor the entire work cell — and access process support and recommendations.
“With our partnership, we’re hoping to eliminate most reactive maintenance activities for our assets,” Fuller said. “We’d like to be completely predictive in our machine assessments and running as lean as possible while maximizing performance and uptime.”
Karen Hanna, senior staff reporter
Contact:
Milacron LLC, Batavia, Ohio, 513-536-2000, www.milacron.com
Karen Hanna | Senior Staff Reporter
Senior Staff Reporter Karen Hanna covers injection molding, molds and tooling, processors, workforce and other topics, and writes features including In Other Words and Problem Solved for Plastics Machinery & Manufacturing, Plastics Recycling and The Journal of Blow Molding. She has more than 15 years of experience in daily and magazine journalism.
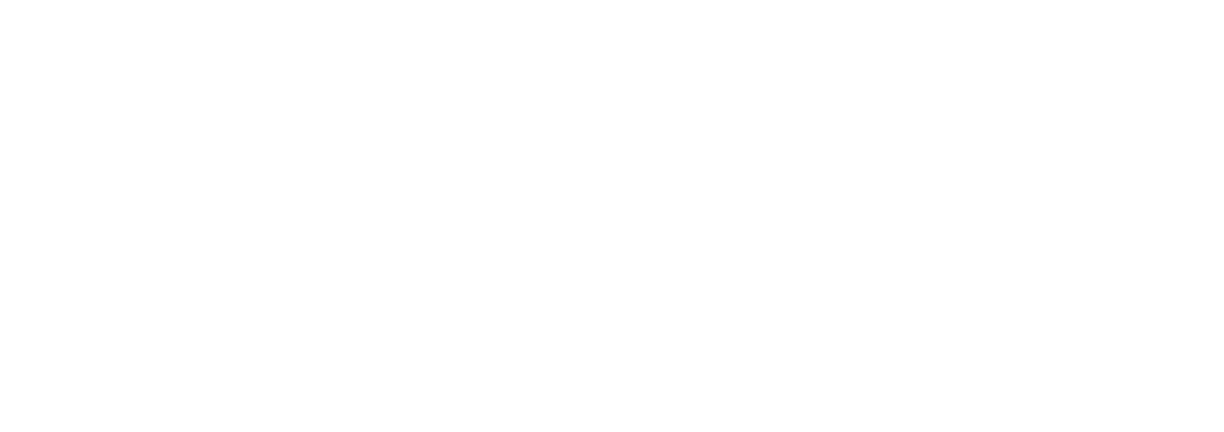