“An ounce of prevention is worth a pound of cure,” according to Benjamin Franklin.
When it comes to extruder maintenance, an ounce of grease could prevent thousands of dollars in repair costs.
“One ounce of grease costs about nothing, but a new screw and gearbox repair can quickly cost several tens of thousands of dollars,” said Robert Fack, service division manager at Kuhne Group.
Extruder manufacturer officials, when asked to identify maintenance steps processors must take to extend the life of their equipment, frequently mentioned lubrication.
Inadequate lubrication can lead to parts seizing up, which is expensive to repair.
“Use the maintenance records of the machine and follow the manufacturers’ recommendations for maintenance,” Fack said. “This information in the documentation is based on many years of experience and knowledge of the manufacturer. Following those recommendations protects the customer from painfully gathering this experience himself.”
Fack also recommended obtaining spare parts only from the OEM because it knows the exact specifications of the parts used.
It is important to maintain an inventory of spare parts, including items that may come with longer lead times, said Mike Puhalla, director of extrusion engineering and technology at Milacron.
“Our team works with customers to understand what vital parts are needed or should be in stock to maintain machinery and its respective components,” Puhalla said.
Regular maintenance results in fewer emergency repairs, less downtime, lower overall costs, better operating efficiency, higher throughputs and fewer production interruptions, said Bert Elliott, engineering manager with Leistritz.
“More uptime allows for management planning instead of putting out fires,” Elliott said.
Successful processors schedule downtime for maintenance, use a preventive maintenance checklist and keep a well-stocked area with all the supplies, tools and equipment needed, Elliott said. In addition, many companies make line operators responsible for maintaining the machinery instead of having them call a maintenance person when there is a problem.
“That way, the operators take more ownership of the machinery and want to keep it in good shape,” Elliott said.
Elliott’s maintenance recommendations for processors include: conducting vibration tests on gearboxes every six to 12 months; using a thermal imaging camera to analyze power panel components; using a thermal imaging camera to ensure barrel and die heating and cooling systems are operating correctly; using a scope to inspect barrels; X-raying or dye-testing shafts to check for fatigue cracks; using synthetic gear oil; keeping records of all AC drive settings and PLC programs on the company’s server; keeping a maintenance log; and removing all screw elements from the shafts every six months, inspecting the parts for cracks and recoating the shafts with an anti-seize compound.
Kevin Slusarz, director of process technology at US Extruders, said regular maintenance is necessary to maintain product quality and to keep parts within spec.
Checking screws and barrels for wear and rebuilding them or replacing them as needed are essential maintenance steps, Slusarz said.
“Ideally, you would pull the screw and measure the screw and barrel twice a year,” Slusarz said. “Another alternative would be to have a standard material that you run and do an output test at three different RPMs and compare [the results] every six months.”
When the output drops, it indicates wear, and the screw or barrel may need to be rebuilt or replaced. Failing to maintain screws and barrels can affect the quality of the end product.
“Most processors have a fixed line speed that they want to keep, so they just turn up the extruder to maintain that line speed,” Slusarz said. “When you increase your extruder speed, you increase your melt temperature, you increase the amount of shear that you put into the material, and those things can affect physical properties.”
As a result, the final product could be brittle, or sag more easily, Slusarz said.
However, the most important maintenance steps may be changing the oil in the gearbox and analyzing it.
“It can tell you if you have either bearings that are beginning to fail or gears that are beginning to fail so you can prevent a catastrophic failure,” Slusarz said. “There have been a ton of catastrophic failures with not maintaining the gearbox. It’s just like the transmission in your car; if you run out of oil, you start wearing parts out and it will fail.”
The presence of steel in the oil could mean there is a problem with the gears; the presence of brass could indicate a problem with bearings, he said.
Inadequate maintenance can lead to breakdowns that disrupt production schedules, said Mark Jones, director of support services for extrusion line supplier SML North America Service Inc.
“We see that occasionally people will skimp on maintenance in order to keep the machine running rather than stop for planned maintenance,” Jones said. “Then they end up with a breakdown, and they end up taking a lot more time to fix things than would otherwise be the case.”
This also can reduce output and lead to increased raw material costs.
“If you don’t maintain the machine, what tends to happen is you can’t control the quality of your product quite correctly,” Jones said. “Often with films, for example, you try to keep it as thin as possible. If you’ve got poor gauging systems, or you’ve not maintained them correctly, then your product ends up somewhat thicker, using more raw materials, and that costs you a lot.”
“Machinery longevity, consistent product quality and predictability in production are all outcomes of an effective machine maintenance program, which includes not only the traditional lubrication and cleanings, but also incorporates diagnostics and trending of machinery parameters such as motor loads, vibration and heat maps,” said Justin Kilgore, VP of engineering at Graham Engineering.
Graham Engineering sells single-screw extruders and extrusion systems under the Graham Engineering, American Kuhne and Welex brands.
Routine barrel and screw inspections allow for planned and fast replacement of the parts, whereas neglect could lead to unexpected downtime that could last for months while awaiting new parts, Kilgore said.
Among Graham Engineering’s recommendations: Follow a regular maintenance plan; routinely inspect and replace critical fluids; check for screw and barrel wear; routinely check safety systems to ensure worker safety; clean and replace filters to ensure good airflow over electrical devices; and maintain a good record of baseline current draws for critical devices, which allows the operator to discover issues before they become catastrophic.
Entek field service specialist Toby Daugherty said processors who emphasize machine maintenance can boost employee satisfaction.
“Operators and maintenance [employees] seeing the willingness to invest in keeping their machines running in prime condition are more likely to participate in keeping the equipment up to standards,” he said.
In addition to the regular maintenance items mentioned by other OEMs, Daugherty said simple good housekeeping is important.
“A clean machine makes it safer and easier to work on,” Daugherty said. “It can also be a driver for daily inspection. For example, noticing a pressure gauge reading is suddenly different while wiping it off.”
It’s also important for companies to listen to their equipment operators.
“They are your eyes and ears on the floor and spend the most time with the equipment,” Daugherty said. “If they bring up a possible issue, it would be wise to investigate it. They may also have ideas to improve production quality or consistency.”
The bottom-line benefit to good maintenance procedures is profitability, said Stefan Lachenmayer, head of Coperion’s extruder modernization team.
“At the end of the day, this all leads to more profitable production of our customers, and that should be the main purpose and the main idea of our customers — to run their machines at the highest efficiency at the highest profitable way,” Lachenmayer said.
The longer a machine lasts, the more profitable it can be, he said.
Maintenance goes high-tech
Computer technology can help processors maintain their equipment.
“The big extrusion lines now are completely computer-controlled,” SML’s Jones said. “They have within them a lot of different sensors that monitor the positions of different parts.”
The sensors, in conjunction with the control system, can alert the operator if parts are taking too long to rotate or if other components are operating outside of normal parameters. Error messages will start flashing on the controller screen to alert the operator, Jones said.
SML software even monitors electric currents. If an extruder component has a sticky bearing, for example, it could be drawing more current from the motors, and that would trigger an alarm.
In addition to the basic monitoring, which is standard on SML extruders, the company offers a system called bit.Wise that can monitor a variety of sensors on several machines and can provide additional information to aid machine maintenance and optimization.
“Say you’re a manager, you can look at how long was the machine running this particular product and how fast is it going,” Jones said. “This is so you can see how well the machine has performed. It’s data analysis.”
SML technicians, like others in the field, are using augmented reality to diagnose equipment problems, Jones said.
“It kind of sounds highfalutin and sci-fi, but it’s really very down-to-earth and basic stuff. A processor’s employees can use a cell phone to connect to SML headquarters, and their technicians will be able to help diagnose problems by seeing what the processor’s workers see. OEM technicians, using third-party software on their laptops, can even draw pictures on a cell phone image to help a processor identify the faulty part.
Kuhne’s Fack said processors should employ personnel for electrical and mechanical maintenance, but Kuhne service technicians can provide remote assistance when necessary.
Kuhne recently began offering customers Remote Lens, smart glasses that connect a processor’s employee directly with experts at Kuhne. The glasses allow the Kuhne expert to see and hear what the on-site technician sees and hears and allows them to communicate in real time. Each person can speak in his or her native language, with the dialogue translated automatically. The glasses are from RealWare, and the software is from a German company called Adtance and has been customized for Kuhne, Fack said.
Kuhne also offers remote online service, which, with a customer’s permission, allows a Kuhne service technician to access a machine remotely and analyze and correct faults in real time.
Graham Engineering’s extruders also include technology that helps processors predict maintenance issues before they arise, Kilgore said.
“Using built-in data trending in a modern control system, such as our Navigator controls, allows for constant monitoring and alerting of machinery performance data to indicate early signs of wear, which will allow for planned maintenance rather than breakdown maintenance.”
Milacron’s M-Powered suite of applications provides predictive maintenance capabilities.
“M-Powered can closely monitor a growing number of machines and components, intervening in time to replace parts before they go bad or a costly downtime event occurs,” Puhalla said. “Part wear and key process parameters are measured against predictive models that drive pre-emptive part stocking programs or on-demand orders before failures occur. Secure monitoring features also work to determine when components begin to impact productivity.”
Coronavirus challenges
The COVID-19 pandemic has driven home the role technology plays in maintenance, especially the ability for OEMs to connect remotely with their customers’ equipment.
The availability of remote technology is especially important now with COVID-19 travel restrictions, Coperion’s Lachenmayer said. “We saw that technology can help us a lot.”
Through remote connections Coperion service technicians can monitor the operating conditions of customers’ machines and help diagnose problems. The company is including additional sensors, including vibration monitors, in its new machines, which helps with troubleshooting.
Coperion technicians also are performing more software upgrades remotely.
“We use the technology to do a software upgrade, for instance, on the other side of the world, where we usually had to fly in,” Lachenmayer said. “With the travel restrictions, we couldn’t send a service tech from one state in the U.S. to another because of restrictions, or they couldn’t fly from the East to the West Coast or from Germany.”
With a customer’s permission, Coperion installs a service box for free that allows its technicians to connect to the machine. The information collected by the service box along with optional software modules can provide additional insight into the operation of the extruder and assist with predictive maintenance.
When should an extruder be replaced?
Extruders are rugged machines. In many cases, with routine maintenance, they can last for decades.
“Honestly, you know, I’d be happy if everybody replaced them every year, but that’s not realistic,” US Extruders’ Slusarz said. “I’ve been in facilities that had machines for up to 30 years.”
The barrel and screw are most prone to wear and can easily be replaced. If an extruder is air-cooled and blowers burn out, those also are simple to replace, Slusarz said.
“There is no set rule for [when to replace an extruder],” Leistritz’s Elliott said. “As long as barrels and screws are available, they can be replaced indefinitely. However, if the gearbox, barrels and screws all need to be replaced, that might cost almost as much as a new machine. Also, older electrical panels don’t have data logging, which helps identify when maintenance (such as screw wear) is appropriate.”
Extruders may need to be replaced if they aren’t able to meet a user’s requirements or are unable to meet those requirements cost-effectively, Jones said.
“The real reason for changing an extrusion line would be that it’s no longer capable of producing product cost-effectively,” he said. “One of the things you might see is that films have gotten much thinner than previously.”
Older extrusion lines might not be able to produce thinner film or do so at a reasonable production rate, which could necessitate replacement. As computer controls get better, operators can reduce the amount of off-spec product, and they’re able to control the gauge a lot more precisely.
“That saves you a lot of materials,” Jones said.
“I have seen machines that are over 30 years old that continue to produce as well as when they were new,” Entek’s Daugherty said. “Those machines continue to operate because they have been well-maintained and updated when components become obsolete. Investing in your investment will make a huge difference in the longevity of the machine.”
Coperion’s Lachenmayer said upgrading is frequently smarter than replacing an extruder. So, when should an extruder be replaced?
“That’s an interesting question,” Lachenmayer said. “Because I am part of the service after-sales team, I would say never. Our extruder is a modular-built system. It consists of a lot of individual pieces, and you can replace each piece one by one with spare parts or you can also upgrade every piece.”
That means, for example, if your PLC needs to be replaced and a newer, more advanced controller is compatible with your 20-year-old extruder, you can upgrade to more state-of-the-art technology at the same time you replace a worn-out component.
“Your machine can evolve over the years and always kind of stay up to date,” Lachenmayer said.
However, if a company is planning on changing the throughput of its machine, switching to a different manufacturing process, or moving its extruder to a new location, it probably makes sense to buy a new machine, he said.
Bruce Geiselman, senior staff reporter
For more information:
Coperion Corp., Sewell, N.J., 856-256-3175, www.coperion.com
Entek Extruders, Lebanon, Ore., 541-259-1068, http://entek.com/
Graham Engineering Corp., York, Pa., 717-848-3755, www.grahamengineering.com
Kuhne Group, Sankt Augustin, Germany, 49-2241-902-147, www.kuhne-group.com
Leistritz Extrusion, Somerville, N.J., 908-685-2333, www.leistritz.com/en
Milacron LLC, Batavia, Ohio, 513-536-2000, www.milacron.com
SML North America Service Inc., Gloucester, Mass., 978-281-0560, www.sml.at
US Extruders, Westerly, R.I., 401-584-4710, www.us-extruders.com
Bruce Geiselman
Senior Staff Reporter Bruce Geiselman covers extrusion, blow molding, additive manufacturing, automation and end markets including automotive and packaging. He also writes features, including In Other Words and Problem Solved, for Plastics Machinery & Manufacturing, Plastics Recycling and The Journal of Blow Molding. He has extensive experience in daily and magazine journalism.
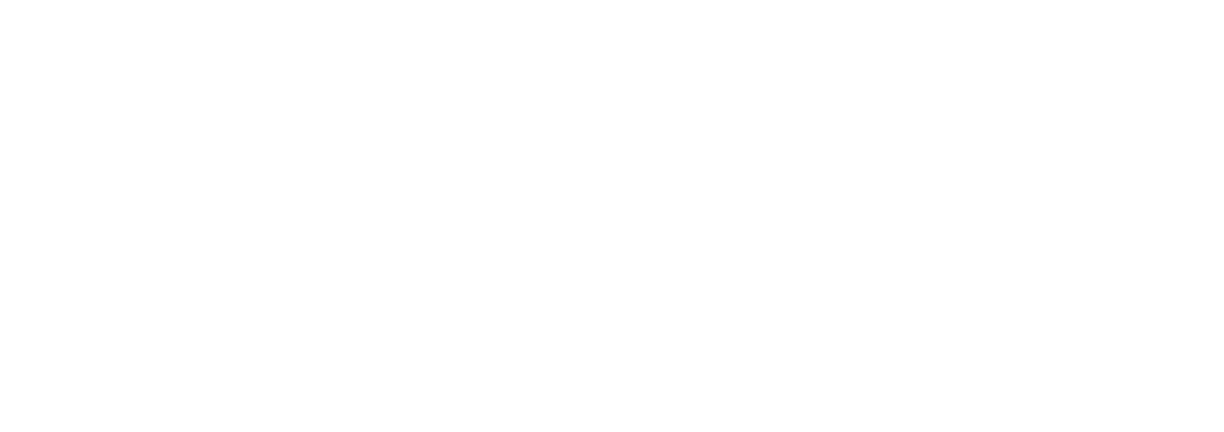