Mold makers, auxiliary equipment manufacturers help process recycled materials
Part 4 of a series on machinery that tackles recycled materials and new resins.
By Bruce Adams
It’s not just injection molding machine manufacturers that build or modify their equipment to handle recycled materials. So do companies that manufacture auxiliary equipment, like Advanced Extruder Technologies (AET), and mold makers, like StackTeck.
Advanced Extruder Technologies
AET makes extruders, and, for more than 20 years, it also has built crammers, which mount on extruders and injection molding machines to enhance the flow of raw materials. The devices, also called crammer feeders, are most often used in scrap reclamation and compounding applications. Crammers help feed difficult materials, such as powders, scrap foam, chopped film, fiber scrap and other low-bulk-density material. An automatic feedback control is incorporated into every feeder; it corrects for density changes.
AET's feeders can be adapted to all single-screw extruders by modifying or replacing the existing feed throat.
“Crammer feeders are used a lot in powder applications,” Jalili said. “If you have 100 percent powder and you want to move that material continuously. Or for blending light-density material with fiber. Sometimes, people just want to use crammer feeders to force-feed the material into the feed throat and pack it so the screw can take it more effectively.”
AET is a custom machinery builder, and all its crammers are made for a specific application and a specific machine.
“They are not off-the-shelf products,” Jalili said. “They depend on the geometry of the machine, the material blend, space restrictions and the best way to bring the material into the crammer feeder. Each one is built custom.”
He said he sells most of his crammers to plastics processors, but some manufacturers of custom injection molding machines, such as Wilmington Machinery Inc., contact his company to manufacture a crammer for a custom machine they are designing.
Editor’s note: See related story on page xx or click here.
AET offers crammers with screw diameters ranging from 75mm to 350mm.
The company also manufacturers two lines of heavy-duty extruders designed for the reclamation of low-bulk-density scrap: dual-diameter reclaim extruders and ram-feed extruders.
“The dual-diameter is a stand-alone machine, and basically is an extruder with a built-in in-line crammer feeder,” Jalili said. “It does a great job, especially with very low-bulk-density materials, such as foam. It can produce twice as much as a conventional extruder.”
The heavy-duty side-ram-feed extruders are for feeding low-bulk-density materials and hot-melt-batch discharge into a short L:D extruder. The ram section can be retrofitted to existing extruders. Screw diameters range from 89mm to 381mm.
StackTeck
Sustainability can present challenges to injection mold manufacturers, according to Jordan Robertson, VP of business development and marketing at StackTeck.
“In one project involving sustainability, we were asked to look at a thicker resin like PET and try to use it in applications that typically call for a high melt index where polyolefins are used,” Robertson said. “The challenge there becomes doing everything you can in the specification of the mold to make it easy to fill because you are working with a more difficult viscosity level with PET than you would with polyolefin.”
The company has developed various technologies for making thin-wall packaging.
StackTeck also has worked on molds for products made from biodegradable resins.
“We can’t say a lot about those because what we know is from customer projects that are confidential,” Robertson said. “In some cases, it’s a matter of viscosity, and filling a part and making a good part with a very different kind of viscosity than we are accustomed to for an item like cutlery. In some cases, we are looking to use very different molding conditions where we have very different temperatures in the molds. Sometimes, in addition to a cooling phase, we want to have a curing phase, which is very different than a standard injection molding approach, and we have to look at the ability to both cool and heat within the mold, and that brings a whole new challenge.”
StackTeck partnered with Arburg and Borealis on a project at K 2019 to make 16-ounce containers out of virgin and recycled PP supplied by Borealis. The parts were molded out of 30 percent recycled material on a 600-ton Arburg packaging machine.
“We found that this recycled material processed the same as virgin material,” Robertson said. “We didn’t need to make any adjustments to the mold. Normally, when we are told that the material has been changed in some way, we anticipate we will have to live with some difficulty, but there wasn’t any.”
However, processors that want to manufacture parts with high levels of recycled content need to make mold adjustments.
“Multiple gating or putting strategically placed thin panels on the part will make the part easier to manufacture,” Robertson said.
Bruce Adams, senior staff reporter
Contact:
Advanced Extruder Technologies, Elk Grove Village, Ill., 847-238-9651, www.aetextruder.com
StackTeck Systems Ltd., Brampton, Ontario, 416-749-0880, https://stackteck.com
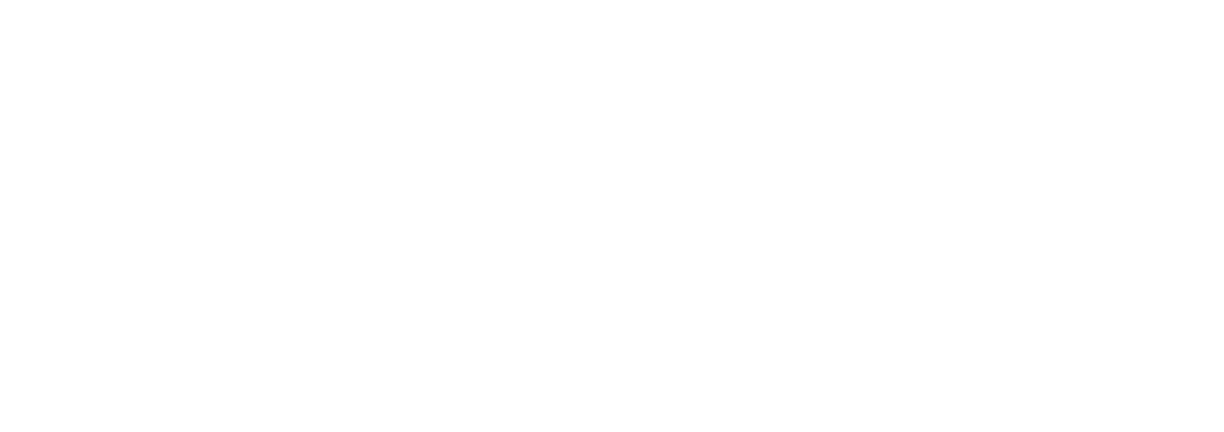