9T Labs' additive fusion technology upgrade boosts throughput
By Bruce Geiselman
9T Labs AG has upgraded its continuous-fiber-composite 3D printing technology, resulting in what the company says is a boost in reliability and a tenfold increase in throughput compared to the previous generation.
9T Labs’ Red Series AFT (Additive Fusion Technology) printing system manufactures parts with continuous-fiber-reinforced polymers with up to 60 percent fiber volume ratio. Thermoplastics can include polyetheretherketone, polyetherketoneketone, polyphenylene sulfide, polyamide (PA) 12, and PA11. Carbon fibers are most frequently used for reinforcement. However, 9T Labs said it has done tests with glass, Kevlar and basalt.
The company’s Fibrify design software handles functions dealing with digital design and analysis. It optimizes internal fiber structures and strategically allocates material where required, according to the company.
9T Labs has updated the software to optimize tracking and provide part-specific reporting with the information available through a dashboard with an updated and optimized user interface.
In addition, the company has incorporated new actuators in its print system’s build module, along with additional sensors and advanced firmware controls, resulting in more precise control and increased throughput and product quality. Sensors typically measure temperature and pressure to forward signals to the actuators, according to the company.
“Today’s Build Module now offers enhanced process repeatability and throughput, boasting a [ten]fold increase compared to the previous generation,” according to a statement from the company.
9T Labs also installed a new modular deposition head configuration that enhances usability, streamlines maintenance and paves the way for future material upgrades through new material heating and guiding features.
9T Labs also announced hardware upgrades, including improved bed leveling and tape-cutting components to simplify handling and extend the lifetime of various wear components. Bed leveling requires the print head to know its exact position in relation to the print bed position. In the latest version, bed leveling now is 100 percent automated, while there were some minor manual operations in the previous machine generations. Improvements have been made for cutting of UD tapes with fiber-thermoplastic polymer ratios of 60:40. In addition, the new machine features a cutting knife designed to last longer.
The build module could be described as a hybrid between an FFF (fused filament deposition) printer and a high-resolution ATP (automated tape placement) machine, according to the company. The fusion module takes the preform and consolidates and reshapes it to obtain the final part.
Both the fusion and build modules have obtained UL certification in compliance with regulatory standards in North America and Australia, according to the company.
Contact:
9T Labs, Zurich, Yannick Willemin, [email protected], www.9tlabs.com,
www.9tlabs.com
Vital Statistics
Print volume | 13.8 inches by 10.6 inches by 9.8 inches |
Maximum printing temperature | 752 degrees Fahrenheit |
Bruce Geiselman
Senior Staff Reporter Bruce Geiselman covers extrusion, blow molding, additive manufacturing, automation and end markets including automotive and packaging. He also writes features, including In Other Words and Problem Solved, for Plastics Machinery & Manufacturing, Plastics Recycling and The Journal of Blow Molding. He has extensive experience in daily and magazine journalism.
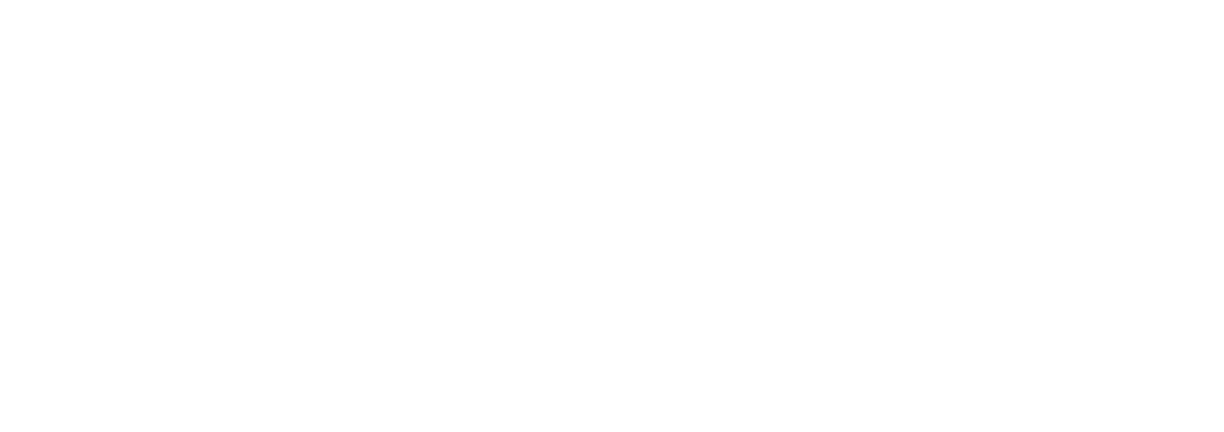