ExAM 255 Aim3D’s ExAM 255 3D printer uses the company’s composite-extrusion-modeling (CEM) method to allow it to print plastic, ceramic or metal parts. When printing plastic parts, the printer can use standard resin pellets, which decreases material costs substantially and allows for faster printing.
What’s new? Several upgrades, including the introduction of a vacuum clamping table, nozzle lock and optional filament extruder.
Benefits Improved print quality and efficiency. The vacuum clamping table lets users attach plates and foils made of a wide variety of materials on the heated printing bed. This makes setup between print runs quicker, and can ensure a secure first printing layer of material such as PP, which has poor adhesion to other materials. The ExAM 255’s new filament extruder option has the same quick-change system and connector as its granulate extruder, making it simple to swap it into one of the printer’s two slots for extruders. Adding a filament extruder lets users take advantage of materials not available in pellet form, such as soluble support materials or newly developed filament materials. The nozzle closure, which can be used with both granulate and filament extruders, prevents material from leaking from the extruder when it is not actively printing. Such leaks can cause problems, such as when soluble support material leaks onto a part, which can cause defects.
AIM3D, Rostock, Germany, 49-381-36766090, www.aim3d.de
David Tillett
Associate Editor David Tillett writes and edits for Plastics Machinery & Manufacturing, Plastics Recycling and The Journal of Blow Molding. He covers new products, industry news, patents and consumer and business equipment. He has more than 20 years of experience in daily newspaper, online and magazine journalism.
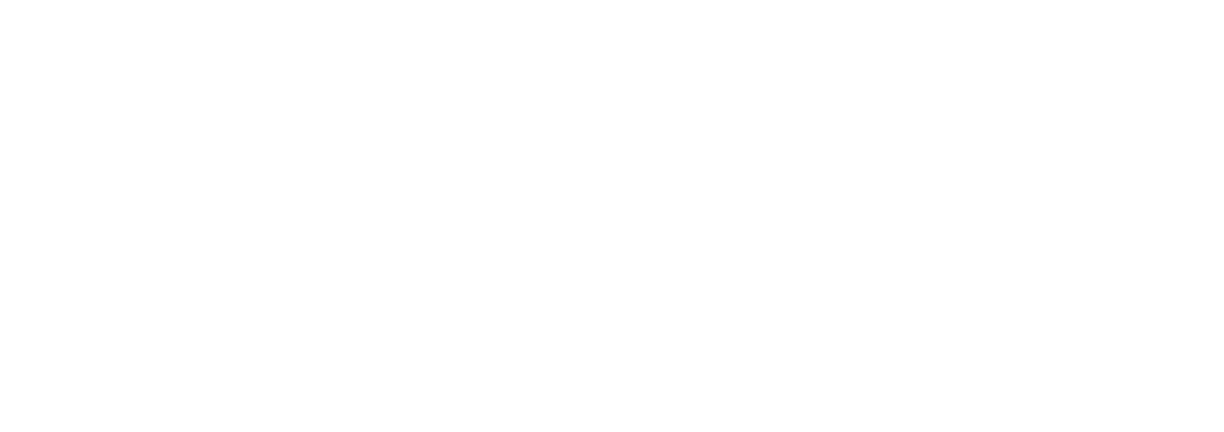