By Ron Shinn
Plenty of innovative new equipment for both plastic and metal 3D printing was on display at the 3D printing industry's biggest show. While talk outside April’s Rapid + TCT 2025 centered around tariffs announced by President Trump about a week earlier, representatives at the show said they were unsure how they would be impacted.
Photos from Rapid + TCT
Check out this gallery from the show floor.
“It won’t be good, but we will just have to work through it,” said one representative of a Chinese manufacturer who asked not to be identified. The representative for a German printer maker said the market might slow down, but it is maturing and plenty of manufacturers will still need new equipment.
There was still plenty of innovative new equipment for both plastic and metal 3D printing at the industry’s biggest show. Here are a few of the technologies.
3D Systems stresses precision and speed
3D Systems introduced the Figure 4 135 DLP printer for manufacturers that want prototyping and low- to mid-volume part production that is faster, more flexible and less costly than injection mold tooling.
3D Systems, based in Rock Hill, S.C., said the printer is designed to provide accuracy and repeatability, from part to part and printer to printer. It is suited for both batch and serial production. A hands-free door is standard.
In addition to prototyping, the Figure 4 135 can produce flame-retardant parts for electronics and thin-wall components. The company said sensors, connectors, housings, covers, snap-fits, knobs, grommets and spacers are typical uses.
The print area is 5.3 inches by 3 inches by 6.5 inches. Maximum print speed exceeds 2.7 inches per hour for most materials. The resolution of the pixels is 50 microns. It comes with a 7-inch touch-screen display.
The unit’s footprint is only 2.2 feet by 2.3 feet, and it is about 4.5 feet high.
Material can be fed automatically from a 19-pound resin cartridge, or users can pour it by hand from a bottle for low-volume applications, such as material testing. Material changeovers take less than 3 minutes.
The printer can process more than 20 high-performance and engineering resins.
The Figure 4 135 uses a projector array to cure an entire layer of liquid resin at once. This technique enables faster print speeds and higher-resolution printing.
The system comes with 3D Sprint software for file preparation, editing, printing and management. No third-party software is needed.
A built-in bar-code scanner provides traceability for part platform, machine ID, material batch and time stamp.
EOS system boosts productivity, cuts costs
EOS GmbH showed its new EOS P3 Next SLS additive manufacturing system for the first time in North America. It boasts an optimized workflow, innovative software and hardware features the company says boost productivity by 50 percent and cut costs by 30 percent.
The EOS P3 Next has a build volume of 13.4 inches by 13.4 inches by 23.6 inches. It uses a single, 70-watt laser, and scan speed is up to 19.7 feet per second.
Available options include an unpacking and sieving station to remove excess material, sieve and convey used powder. A blasting cabinet, cool-down cover and mixing station are also available.
EOS said the P3 Next has an 80 percent material reusability rate.
The new printer utilizes EOS System Suite software to access all machine data, including quality-control information. EOS said it streamlines workflow, provides control on the shop floor and reduces order-to-print time by 30 percent.
Mosaic Array includes four printers, robot arm
The Array, designed for high-volume industrial production with integrated robotics and multi-material technology, generated plenty of attention at Rapid.
The fully automated system consists of four FFF 3D printers, automated print queuing and build plate removal. It can accommodate 32 material pods — eight for each printer so it can print up to eight materials in each part. Material changes are automated.
Build volume for each of the four printers is 14 inches by 14 inches by 13 inches. Element print speed is about 7.9 inches per second and element travel speed is 11.8 inches per second. Beds can be heated up to 248 degrees Fahrenheit and the thermal chamber up to 176 degrees Fahrenheit.
Mosaic, the Canadian company that builds the Array, said it enables one operator to run the equivalent of 250 3D printers. The Array is capable of 72 hours of continuous, unattended operation.
The Array has 40 print beds for continuous operation. An onboard robotic arm automatically removes and replaces print beds. A storage cart for completed print beds is included.
The unit has an automatic bed leveling feature. There is an integrated exhaust fan with HEPA filter in the cabinet. Failure detection is also automated.
The Array is about 5.3 feet wide, 5.3 feet deep and 7.3 inches high. Multiple units can be connected via LAN or Ethernet.
Mosaic’s Canvas software monitors and manages the printer system.
Elegoo’s Jupiter 2 targets large-format printing
Chinese manufacturer Elegoo unveiled the Jupiter 2, a new large-format 3D resin printer that features a modular design and smart resin-management system.
Other key features include an enclosed light source, multi-point auto-leveling and a manual leveling option for additional control.
Elegoo said the modular design lets users swap the LCD screen in 10 minutes, one-fifth the time of traditional setups. Replacing the release film takes 10 seconds, which is much faster than conventional methods.
The Jupiter 2 also introduces a smart resin-management system, automatically feeding and recycling resin with a detachable box that can hold a 67.6-ounce resin bottle. The heated resin tank ensures that the resin stays at the ideal temperature, guaranteeing consistent results throughout the print process.
There is also a built-in camera for viewing the build remotely.
"The Jupiter 2 is our bold step forward in elevating the resin 3D printing experience," Elegoo CEO Chris Hong said. He expects the Jupiter 2 to have broad applications in toys, health-care and consumer goods products, as well as prototyping.
Elegoo, a 10-year-old company, is located in Shenzhen. It has 700 employees, and sales in 2024 were more than $700 million, the company said.
HP debuts inexpensive flame-retardant material
HP Inc., working with Evonik, introduced an inexpensive, halogen-free, flame-retardant material for advanced 3D printing applications.
The new material, named HP 3D HR (High Reusability) PA 12 FR, is now in full production. It meets UL94 V-O at 2.5mm thickness. The standard means burning stops within 10 seconds on a vertical specimen.
HP, based in Palo Alto, Calif., also said the material is more sustainable, has better flame- resistance and superior strength, and minimizes waste and provides a smoother surface finish than previously available materials. It is designed for prototyping, as well as for manufacturing production parts.
Magics software update speeds design process
Software developer Materialise introduced the latest version of its Magics software for 3D design and production. The company said the new release, which includes nTop implicit geometries, reduces build preparation time from days to seconds while maintaining design precision.
“This new capability in Magics combined with Materialise’s next generation of build processors, enables printability of complex parts that could not be printed before,” the company said in a news release.
Magics 2025 will be available in May. It introduces seamless processing of nTop geometries without the need for mesh conversion, drastically reducing preparation time for complex parts.
nTop is software for designers that increases the speed of complex modeling operations and creates geometries that are not possible in traditional CAD.
Materialise is based in Belgium.
Contact:
3D Systems, Rock Hill, S.C., 888-598-1438, www.3dsystems.com
Elegoo, Shenzhen, China, [email protected], www.elegoo.com
EOS of North America Inc., Novi, Mich., 877-388-7916, www.eos.info
HP Inc., Palo Alto, Calif., 650-857-1501, www.hp.com
Materialise USA, Plymouth, Mich., 734-259-6445, www.materialise.com
Mosaic, Toronto, [email protected], www.mosiacmfg.com
Ron Shinn | Editor
Editor Ron Shinn is a co-founder of Plastics Machinery & Manufacturing and has been covering the plastics industry for more than 35 years. He leads the editorial team, directs coverage and sets the editorial calendar. He also writes features, including the Talking Points column and On the Factory Floor, and covers recycling and sustainability for PMM and Plastics Recycling.
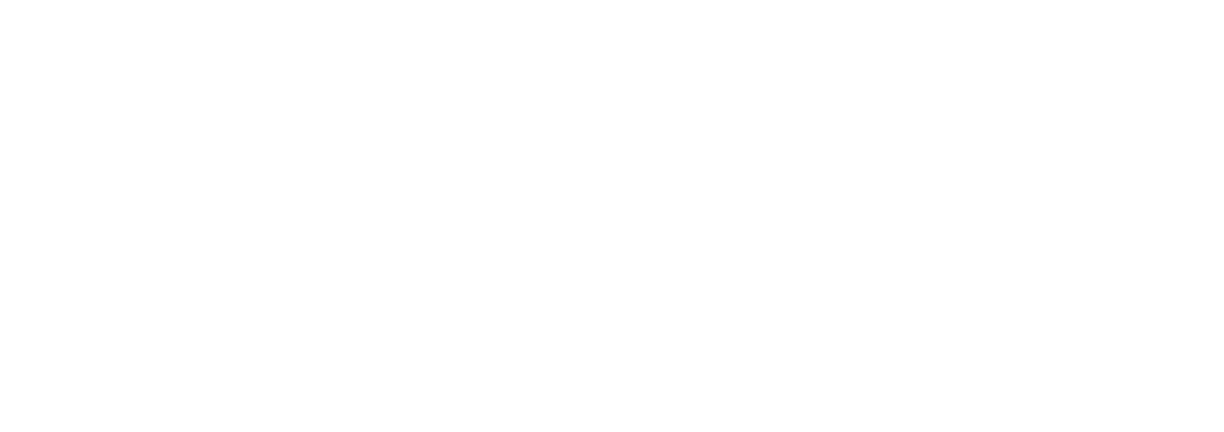