By Karen Hanna
For manufacturers looking to expand on their use of 3D printers, materials availability and cost continue to present a major stumbling block. But 3D printing experts say the situation is improving.
“You can go ask any one of these machine manufacturers and say ... ‘I want a 30 percent glass-filled nylon part that's yellow, and I want … a purple silicone seal on top,’ which happens every day in the injection molding world. And they would all say, ‘Oh, yeah, that can't be done,’ or, ‘It's going to cost a million dollars,’ ” he said. “And literally, it's happening every day, just down the street with this legacy technology.”
As Fabian Krauss, head of the polymer systems business for EOS, conceded in a discussion about 3D printing trends, “The broad opinion is that 3D printing has a limitation in materials.”
The stable of plastics appropriate for 3D printed parts targeted to consumers is especially small, Mason said.
Also, he said, surface quality and color selection are lacking, and, unlike conventional processes, most additive manufacturing (AM) technologies can’t handle more than one material at once.
“It’s ridiculous almost, how additive [manufacturing] is, in my opinion, for the consumer 30 or 40 years behind where the state-of-the-art technology is for other polymer manufacturing,” he said.
Material shortcomings
One challenge 3D printer users face is the price of material. Representatives of companies that make 3D printers marketed as open-materials platforms, including Nexa3D and Arburg, say manufacturers have options that can help them overcome this challenge.
According to Mason, 3D printing materials can cost 10 times as much as comparable resins used by injection molders, who enjoy much bigger economies of scale when it comes to material availability and pricing.
But Michael Currie, chief product officer for Nexa3D, pointed out that the cost of materials is just one aspect of the overall cost of printing — which gives OEMs options in how to enhance AM’s value.
Related: 3D printing OEMs are scaling up
“You look at say, polypropylene right now, the injection molded version of that is $1 a kilogram, and, at this moment, for 3D printed materials, it’s $50 and up,” he said. “The costs of 3D printing, it really comes down to the materials ... and then the labor associated with getting the part ready. If you can lower either of those two components, it’s going to put us on a better footing with the traditional manufacturers.”
Paying attention to which materials they will be able to use is important for any prospective 3D printer buyer, said Lewis Simms, Nexa3D’s head of industrial product marketing.
To make sure they have the greatest freedom, manufacturers should opt for printers that tout open-materials platforms, some experts advise.
“That’s another key thing too, as you’re looking at evaluating any sort of additive process, is ensuring that you as a user have as much control and latitude as possible, while still achieving good, consistent, reliable printing,” Simms said.
Open-materials platforms can use a variety of materials from many sources, rather than just proprietary materials. This means users have a broader selection, and with a bigger market to serve, materials makers enjoy more freedom to develop products with less risk. Also, as they bring bigger volumes to market, suppliers can adjust pricing, so it’s more purchaser-friendly.
Aim3D’s extrusion-based printers, including its latest ExAM 255, use a broad range of pellets, rather than filaments, from a variety of sources.
“It’s much easier to create a pellet material compared to making filaments, as these filaments have very high needs for flexibility and dimensional parameters,” Morrison said.
As manufacturers settle on particular formats and begin producing bigger volumes, experts predict prices will come down.
“The cost scaling will probably only be possible if we use standard series material from other high-volume processes in AM,” Morrison said.
Investing in R&D
Brent Stucker, who co-wrote the book “Additive Manufacturing Technologies,” used in college classrooms, is among experts excited by how much potential materials development has to advance 3D printing technologies. Opportunities for using more-sustainable materials or developing materials with new properties give him reason to believe the technologies still have a long runway.
“We’ve tried to mimic what we have available in traditional manufacturing, and we’re only just at the tip of the iceberg of saying, ‘Why mimic traditional stuff? Let’s go beyond it,’ ” he said.
AM materials already are branching out.
Related: See innovative parts produced using 3D printing technology
For example, Victor Roman, managing director of Arburgadditive, said Arburg’s Freeformers can process recyclates, biomaterials and pressure-sensitive adhesives. And Carbon’s materials can be used in lightweighting, said Phil DeSimone, a co-founder and member of the company’s CEO's office.
Stucker pointed to advances in flame-retardant materials, as well as other developments.
“... Things like aircraft engines, or consumer products or toys, we want toy materials that are nice and shiny and cool, but very biocompatible and friendly to the environment. There’s ways that we’re looking at making new additive manufacturing-based materials that are different than what you would get with injection molding,” he said.
Taking steps forward
3D technology suppliers reported they’re making headway, with the ability to produce materials that exhibit better characteristics, improve sustainability or provide other advantages.
Even with fewer materials available to them, 3D printer users can make a wide variety of parts, according to EOS’ Krauss.
“You have so much freedom in 3D printing that you don’t need the variance and the width of a portfolio in the material. Having said that, there is still a lot of work [being] done in broadening the material sets. We haven’t touched, or we haven’t completed the portfolio yet; there is higher temperatures; there is more-Companies addressing a common criticism of 3D printers — that they can’t handle more than one material at once — include Voxeljet and Arburg.
“We are currently working on the 3D printing equivalent to two-shot molding — where multiple material properties can be produced in the same part with no extra cost,” said James Reeves, global director of polymer sintering for Voxeljet, which is looking toward the coming commercial release of its VX1000 HSS high-speed-sintering printer. “Being a digital manufacturing process means this also can be done at a voxel level, so we can blend from one material to the other without a hard stop. For example, a hard TPU gradually changing to a soft TPU, therefore giving a structural and cushioning element to the same part.”
Users of Freeformers also can produce parts that exhibit a combination of hard and soft characteristics, said Roman, of Arburg, which last year released its biggest machine in the line, the Freeformer 750-3X.
For example, Roman said, manufacturers are using the machines to make robotThe machines are ideal for manufacturers of aviation or medical parts because they can process FDA-approved and certified original materials, he said.
Meanwhile, Derek Vilim, product hardware manager for Formlabs, touted his company’s development of its first flame-retardant material, as well as its new TPU 90A, a skin-safe powder that’s been validated for use in prosthetics, orthotics and other patient-specific devices requiring custom designs.
Summing up some of the rest of his company’s portfolio, Vilim said, “Formlabs 3D printers offer a wide range of materials and advanced engineering ideal for molding including Rigid 10K Resin, High Temp Resin and Grey Pro Resin. Using these and similar materials allows companies to create 3D printed parts with the quality and properties needed for their end products, such as temperature resistance, impact resistance, flame retardancy and more.”
Reasons for optimism
Greater uptake of 3D printing technologies and advances in materials could produce a positive feedback loop.
According to experts like Tali Rosman, who advises early-stage companies on strategy, product roadmap and corporate development, materials R&D is paying off.
“I also think, with better materials, 3D printing can, one, grab more of all of these markets, but also expand into other applications where it’s not necessarily playing today,” she said.
As demand grows for the technologies and materials, material costs will go down, said Simms, of Nexa3D, which recently released a new printer, the Xip Pro.
New developments in materials provide just a preview of what’s to come, according to Stucker, who’s been involved with AM for decades and started his own consulting firm, 3DX Consulting, in May.
“I really think we’re just at the cusp of where materials are going,” he said.
Karen Hanna, senior staff reporter
Contact:
- 3DX Consulting LLC, Park City, Utah, 435-363-5197, [email protected]
Aim3D, Rostock, Germany, 49-381-367-66090, www.aim3d.de
Arburg Inc., Rocky Hill, Conn., 860-667-6500, www.arburg.com
Carbon Inc., Redwood City, Calif., 650-285-6307, www.carbon3d.com
EOS North America, Pflugerville, Texas, 512-388-7916; Novi, Mich., 248-306-0143, www.eos.info/en
Formlabs Inc., Somerville, Mass., 617-702-8476, www.formlabs.com
Nexa3D, Ventura, Calif., 800-797-0633, www.nexa3d.com
Tali Rosman, [email protected], via Linkedin at www.linkedin.com/in/talirosman
Voxeljet America Inc., Canton, Mich., 734-808-0025, www.voxeljet.com
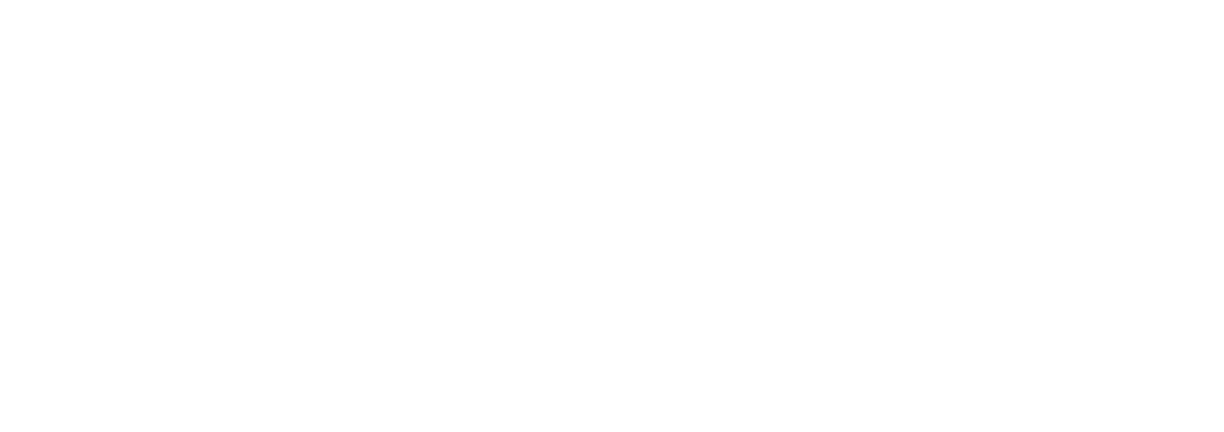