Trailblazing backpacks made with Carbon-printed component
By Bruce Geiselman
Osprey Packs Inc., a manufacturer of high-performance backpacks, has launched its new Osprey UNLTD backpacks, which feature a lattice-structure lumbar support created with Carbon’s DLS 3D printing technology.
The name UNLTD is pronounced “unlimited.”
Osprey is the first backpack manufacturer to use Carbon technology, according to the companies.
Osprey UNLTD’s 3D-Printed Fitscape Lumbar support delivers superior ventilation, fine-tuned cushion support and an anti-slip surface grip to keep loads firmly in place, Osprey said.
Tom Entwistle, a VP of sales and product for Osprey, in a press conference called the product launch “a paradigm shift” in backpack technology.
Future design today
“We believe that what we have in front of you is very likely what you’ll see 10 to 15 years out from other brands,” he said. “We wanted to pioneer and push the boundaries of technology to essentially create a time machine and bring you a product that is far forward in its design and mentality into the present day.”
The lattice structure is manufactured on Carbon printers using the company’s trademarked Digital Light Synthesis (DLS) technology, which uses digital light projection, oxygen-permeable optics, and engineering-grade liquid resins to produce polymeric parts with exceptional mechanical properties, resolution and surface finishes, according to Carbon. The DLS process allows engineers and designers to develop new products faster and create software-tunable lattices that can’t be accomplished with traditional foam padding.
“Traditional manufacturing methods teach us that in order to push the boundaries of innovation, product development timelines need to be extended,” said Phil DeSimone, Carbon co-founder and chief product and business development officer. “The entire process using Carbon DLS took about one year with only six months for us to iterate on the design, enabling Osprey to take this innovative product to market faster.”
Printing the impossible
The DLS technology allowed Osprey to use materials in the UNLTD backpacks that were “previously untapped by the pack industry,” Osprey said. Carbon’s EPU 41 elastomeric polyurethane resin was used. In addition, the lattice design offers a combination of comfort zones — alternating support and cushioning — that previously would have been difficult or impossible to achieve.
“You can have dozens of different response zones within a single part, which historically was unachievable, because you would have to lay multiple different types of foams in order to get that sort of complexity and comfort from softness to stiffness to bluntness,” DeSimone said.
In addition, unlike foam, which tends to hold in heat, the lattice structure dissipates heat.
“The ability of getting better airflow and an open cellular structure is way, way better,” DeSimone said. “The ability of getting extra airflow particularly in the back region is something that will differentiate this pack, particularly on a hot summer day.”
Unlocking potential
In a video describing the UNLTD packs, Osprey founder Mike Pfotenhauer said “This is our pursuit of new processes, design concepts and technologies with less regard for costs involved. It allows us more freedom to experiment with materials and manufacturing processes that normally would be beyond our price points.”
Osprey UNLTD packs are available in four styles: Osprey UNLTD AirScape 68 (men’s and women’s) and Osprey UNLTD Anti-Gravity 64 (men’s and women’s). While most of Osprey’s backpacking packs sell for between $155 and $390, each model of its UNLTD packs sells for $700 on the company’s website.
“Osprey UNLTD is the manifestation of Osprey’s approach to innovation,” said Rob BonDurant, VP of marketing for Osprey. “In developing Osprey UNLTD, we removed the shackles of commercialization and production schedules to move beyond traditional manufacturing technologies ushering in a new era of backpack design and the ultimate backpacking experience.”
Bruce Geiselman, senior staff reporter
Contact:
Carbon Inc., Redwood City, Calif., 650-285-6307, www.carbon3d.com
Osprey Packs Inc., Cortez, Colo., 866-284-7830, www.osprey.com
Bruce Geiselman
Senior Staff Reporter Bruce Geiselman covers extrusion, blow molding, additive manufacturing, automation and end markets including automotive and packaging. He also writes features, including In Other Words and Problem Solved, for Plastics Machinery & Manufacturing, Plastics Recycling and The Journal of Blow Molding. He has extensive experience in daily and magazine journalism.
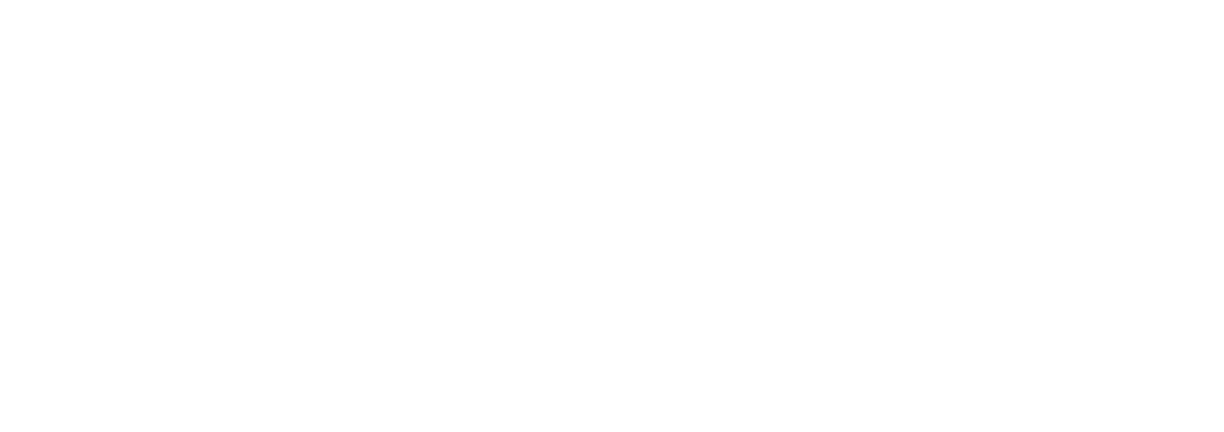