Latest Wasp printer targets serial part production
The new Delta Wasp 2040 Production 3-D printer from Italy’s CSP is designed for customized serial part production.
A new automated process built into the fused filament fabrication (FFF) printer allows for continuous printing without human intervention for part removal. The printer can run 24 hours a day, the company said. It also allows manufacturers to make fast and cheap product variations.
“Delta Wasp 2040 Production paves the way to a new concept in production, mixing the capacities of additive technology, hence customization, with mass production,” the company said.
The printer includes a stainless-steel belt, which also serves as the heated build plate. Once the printer forms the part or parts, the belt brings them forward and out of the printer until they detach and fall into a container. The belt then returns to the starting position to begin another print. The belt is divided into zones with different surface textures and materials to allow for optimal adhesion, the company said.
The belt can be heated to a maximum temperature of 248 degrees Fahrenheit. In addition, it maintains its flatness and stability throughout the printing process, thanks to a pump generating a vacuum on the build plate, which eliminates any vibration during the printing process. Once printing is complete, the vacuum pump is deactivated, which allows the belt to move and remove the completed part or parts.
An air heater is incorporated into the Delta Wasp 2040 Production model that improves printing with engineering resins such as ABS, carbon-fiber-infused polyamide and TPU. The heater raises the chamber temperature to 158 degrees Fahrenheit. The printer automatically opens the printing chamber door just high enough to remove the printed part, reducing heat loss.
The printer also includes a job queue feature that allows the user to select the number of parts to be printed and accommodates the scheduling of different parts.
One of the major benefits of the new Delta Wasp 2040 Production model is the ability to automate production, said Michael Burghoffer, founder and chief entrepreneur of PicoSolutions Group, which is the North American distributor of Wasp printers. The new model can be used overnight without the need for a worker to remove the finished parts, saving users “quite a bit of money,” Burghoffer said.
Bruce Geiselman, senior staff reporter
For more information:
CSP srl, Massa Lombarda, Italy, 39-0545-87858, www.wasproject.it/en
PicoSolutions Group Inc. Kearny, N.J, 877-731-9966, www.picoSolutions.com
Bruce Geiselman
Senior Staff Reporter Bruce Geiselman covers extrusion, blow molding, additive manufacturing, automation and end markets including automotive and packaging. He also writes features, including In Other Words and Problem Solved, for Plastics Machinery & Manufacturing, Plastics Recycling and The Journal of Blow Molding. He has extensive experience in daily and magazine journalism.
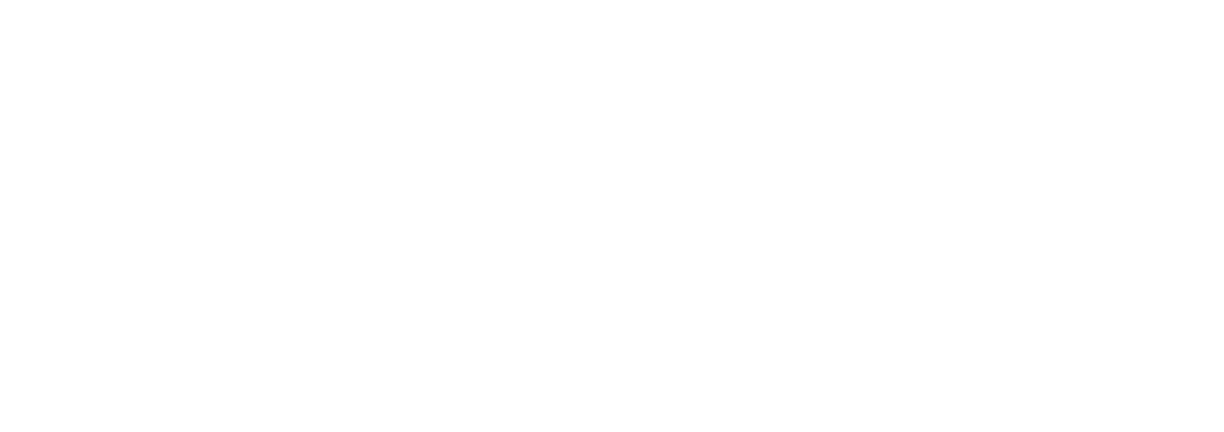