The president and CEO of Boston-based 3-D printer manufacturer Rize envisions four things for his company and 3-D printing in general: machines that are safe and easy to use, and that solve processing problems and protect users’ intellectual property from counterfeiters.
Andy Kalambi, named to the top post at the company in 2017, discussed these issues and more with Plastics Machinery Magazine senior staff reporter Bruce Adams.
What were your first few jobs out of college?
How were you first exposed to the plastics industry?
Kalambi: I started in plastics with BHEL in their control equipment division. We produced a wide range of electronic products, and there were a lot of injection molded components in the products. I was responsible for plant operations, and there were a number of injection molding machines that I had to manage. When I was with SAP in Singapore, one of my roles was strategic business development for manufacturing. I was responsible for five manufacturing industries, including chemical, pharmaceutical and plastics. At Dassault, I came in touch with the design aspect of plastics.
How does your training as a mechanical engineer shape your decisions as CEO?
Kalambi: I started my career in the hardware business with control panels at BHEL. I went into the software world for a long time. Coming to Rize was coming back to my roots. It is hardware with strong elements of design and manufacturing. It also has a big impact on supply chain and all elements of the whole value creation process, which I have been deeply involved with in all my jobs.
You were named president and CEO of Rize in 2017. How did your career prepare you for this position?
Kalambi: Dassault Systèmes exposed me to the design element that goes into 3-D printing. Also, as CEO of Enovia [a 3DEXPERIENCE-powered collaboration management software] while at Dassault Systèmes, I had the ability to run a full business. At SAP, I learned about the supply chain that put 3-D printing into the mainstream. At MatrixOne, I honed my sales, business development and market development skills. I learned digital continuity through the whole design and manufacturing world.
The Rize One printer is the company’s first using its patented augmented polymer deposition (APD) process. What makes it unique?
Kalambi: It solves three problems: the part support removal, safety, and authentication and security.
How does it overcome these problems?
Kalambi: Eugene Giller, our founder, spent a lot of time thinking about the problems that this industry faces in terms of the ability to scale. Two major problems … prevented 3-D printers from being used ubiquitously. When you print a part, you want to print it in the most safe and easy-to-use manner. You don’t want to breathe any emissions from extruding the plastic.
[Another] problem was the ability to do post-processing in an easy fashion … removing support always has been a challenge in this industry.
When Eugene and the company looked at how to do this, they found two technologies that were being used independently. An extrusion technology called fused-deposition modeling, or FDM, which allows you to extrude the material and print it. It was popular technology because it was easy to use. The problem with that was when you melted that plastic it would emit VOCs [volatile organic compounds] or ultra-fine particles. That was the first challenge we wanted to solve with the APD process.
We did a little innovation of the material itself and produced the first zero-VOC, industrial-grade 3-D printing process. We took plastic that had never been used in the 3-D printing industry, we applied it to our technology and made it work. This plastic is food-grade and medical-grade plastic … [and] it is better than ABS in terms of strength. We wanted the plastic to be totally safe for users and the environment. We are very proud of that.
The second challenge we wanted to solve was when printing you want the part to remain on the supports. But when the part is finished printing, you want to be able to easily and quickly remove the supports from the part without soaking the part in hazardous chemicals for hours and sometimes a full day. We took two existing technologies, [FDM] and material jetting technologies, and combined them in one hybrid process to address these problems. We found a way to jet a release ink between the part and the support so that the support can be removed very quickly, safely and easily and still leave clean surfaces, so no additional work needs to be done to the part.
How does APD address security issues?
Kalambi: A third problem with 3-D printing is that you are printing your intellectual property [IP]. Sending out your IP is like sending out a confidential document. You want the IP to be safe and authenticated and not lost to others printing more copies of it. We also can use marking inks to mark the part internally with QR [or] bar codes, instructions or part numbers, so that the marking cannot be removed. We extended that capability with colors to achieve functional, full-color parts. The APD process ... combines jetting with extrusion in a single process to solve the problems that I mentioned.
What is Rize working to develop now?
Kalambi: We are releasing the XRize in August. It is the first full-color 3-D machine to produce functional color parts in an office-friendly, easy-to-use environment. It will be safe and easy to use. We also are introducing new materials into our products. We recently introduced carbon composites. You can infuse plastics with composites to get different components, such as elastomeric materials for elastomeric applications. That had been a challenge due to the support removal process, but our ability to remove supports makes it much easier.
For the 3-D printing industry in general, it will be bringing more automation into the process by integrating robotics and video systems, and by creating highly connected environments. We have a software connected environment called Rize Connect, which enables users to remotely manage and monitor their Rize 3-D printers from any location.
What is your vision for the company?
Kalambi: Safety is vision No. 1 and ease of use is No. 2. Producing plastics has always had a risk associated with it. Make safety pervasive so that people don’t fear 3-D printers in any form. You don’t think twice about buying a photocopy machine and putting it next to you. It should be the same with a 3-D printer. You must be able to use a 3-D printer without venting the room.
What is the biggest challenge that 3-D printer manufacturers face as an industry?
Kalambi: People in the 3-D printing industry have been very focused on how to produce the part, which is important. But the user experience and how easy it is to use the printer to produce the part has not been a focus. That has stymied the growth of this industry. It is a 30-year-old industry. It should be much bigger than it is today. The innovation of the part and the user experience will take the industry to the next level.
Where do you see the 3-D printing industry five or 10 years from now?
Kalambi: I bet my future on this industry. There will be enormous innovations. There have been more patents filed in the 3-D printing industry than any other industry. The next after us is the electric vehicle industry. You will see a lot of 3-D printing on the shop floor. My vision is that our 3-D printer will become like a photocopy machine that is available anywhere at any time. You will see 3-D printing at the retail level. You will be able to 3-D print a part at a store, like Staples, for example, and use the part. Accelerators and labs will spur a lot of innovation with people who will design, print and consume all in one boat. It will empower the consumers to personalize what they want to consume.
How would you like to be remembered?
Kalambi: Most of us get remembered only for a few minutes. The only way to be remembered is if you stay in the hearts of people. I hope I’ve done something to improve their lives. People remember small acts of kindness that you did to help them. I would rather be remembered by people in their hearts, not in a grandiose fashion. I don’t want to lay claim to what we have done as a company. Many people contributed to our success. I hope that people think well of me after I’m gone.
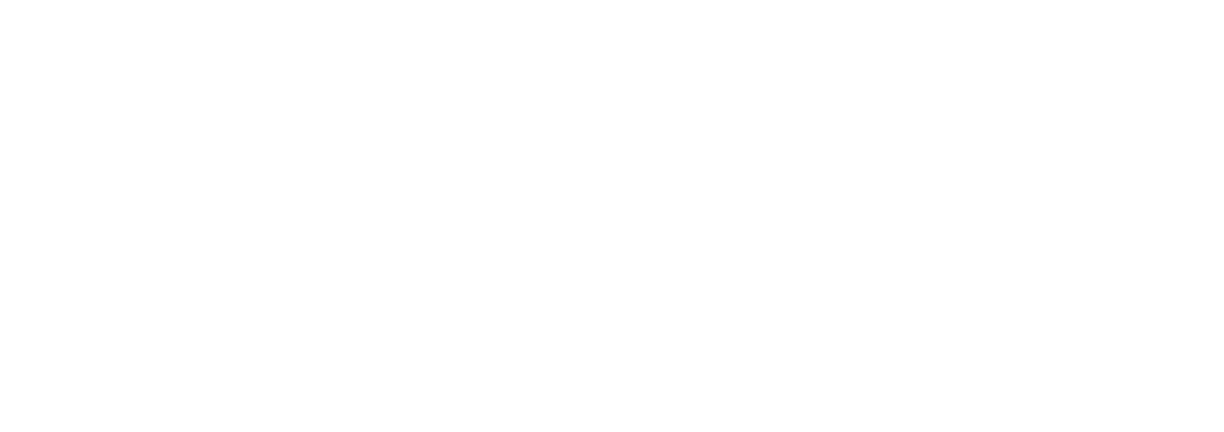