After acquisition, Protolabs ramps up prototyping, production
3-D printing is changing manufacturing, and Protolabs is leading the charge in the plastics industry.
The Maple Plain, Minn.-based company, which specializes in prototyping and low-volume production of injection molded parts, has embraced 3-D printing. In 2014, Protolabs acquired Fineline Prototyping, a 3-D printing company in Raleigh, N.C. Protolabs consolidated Fineline's two plants into a 77,000-square-foot facility in nearby Cary, N.C., in 2016. It is one of the largest 3-D printing facilities in the world, according to a Protolabs staff member.
It has more than 100 3-D printers turning out prototypes and production parts on a scale not seen elsewhere. It can produce 3-D plastic, elastomeric and metal parts and components.
Protolabs even has a dedicated team that tests and modifies new 3-D printers to improve performance. "We modify stereolithography machines to be able to offer the best part tolerances in the industry," applications engineer Joe Cretella said. "We do that across the board for all our technologies."
Modifying the inner workings of a new machine to make it faster and more consistent is a way Protolabs pushes the envelope on 3-D printing technology. Cretella said Protolabs gives feedback to machinery manufacturers. "That is how we have been able to influence some of the parameters that go into HP printers today," he said.
Protolabs was launched in 1999 with the goal of significantly reducing the time required for creating injection molded protype parts. The business grew and added injection molding capacity in Maple Plain, along with CNC machining and sheet metal fabrication. With 12 manufacturing facilities around the world, Protolabs now has more than 225 injection molding machines and more than 600 CNC machines and lathes.
Protolabs is a publicly traded company and had annual sales of $344.5 million in 2017. About 12.6 percent, or $43.4 million, came from 3-D printing.
"With Protolabs, we have grown exponentially," said Cretella, who came to Protolabs with the 2014 acquisition of Fineline. "We had about 70 employees, and, four years later, we are over 200 employees.
"We have seen a huge increase in customer interest, and that increases our ability to get more machines and equipment," he said during a recent Plastics Machinery Magazine visit to the North Carolina facility that is dedicated to 3-D printing.
You could say that Protolabs and 3-D printing were a perfect match.
"Our thought with 3-D printing was let's take what customers were already doing with 3-D, which was getting their prototypes and getting fast prototypes, and bring it in-house at Protolabs," Cretella said. "We can make it even faster and bring the quality aspects of prototyping that Protolabs has with CNC machining and injection molding to 3-D printing.
"We can offer our customers a turnkey service," he said. "We can build your prototype, take it to CNC if necessary and finally injection molding. Protolabs has added sheet metal fabrication as well. We have the whole suite of services to help our customers bring their products to market faster."
Speed to market drives everything Protolabs does. It promises it can ship as many as 50 3-D printed parts in one to seven days. Cretella said the standard time is actually three days. If a customer is in a rush, it can upload a CAD file to Protolabs and get an instant price quote and expected delivery date. In some cases, parts can be shipped the next day.
The service includes minor tweaks on a customer's CAD file to improve 3-D processing.
The North Carolina facility is organized and staffed to meet those deadlines. It might have the biggest collection of 3-D expertise in the plastics industry.
A staff of 20 applications engineers and applications specialists scrutinizes incoming orders. "How quick we respond to customers is an important metric," Cretella said. The team works with hundreds of projects every day.
The CAD file is then sent to be built with one of five printing processes. Quality checks guide the process from CAD file to finished part.
• Stereolithography (SLA) is the process that Fineline started with and is still the one that's most frequently used at Protolabs. The company has more than 70 SLA machines turning out concept models, cosmetic prototypes and intricate parts with complex geometries in a wide variety of materials. All the SLA printers are from 3D Systems and all have been modified by Protolabs to improve tolerances, repeatability and speed.
• PolyJet printers from Stratasys are best suited for parts with elastomeric features such as gaskets, seals and housings. A range of material durometers is available. The PolyJet process can be used for simulating overmolding and combining two colors and multiple materials in a single part.
• Selective-laser-sintering (SLS) printers from 3D Systems use a wide range of nylon materials, from nylon 11 to glass- and mineral-filled nylon 12. They can also print parts in a durable and flexible TPU that offers a 70 Shore A hardness.
• Multi Jet Fusion (MJF) printers from HP also use nylon materials and produce better surface finishes, finer resolutions and more consistent mechanical properties that SLS printers. They can create prototypes or end-use parts.
• Direct-metal-laser-sintering (DMLS) printers from Concept Laser use a fiber laser to weld atomized powder into fully dense metal parts. They use production-grade materials and create functional, end-use parts. This is a fast-growing technology and Protolabs acquired three DMLS machines this year and has two on order.
Each 3-D printing process has a dedicated service team at Protolabs.
Protolabs pushes the limits of 3-D technology by studying every instance in which a print job fails to meet expectations. A table in the areas where applications specialists work displays the less-than-perfect parts, so specialists can figure out how to improve the process.
"On the front end of a project, we try to steer customers to utilize our services in the best way possible," Cretella said. "We are not going to be the traditional millions-of-parts, steel-tool manufacturer. We are going to be a provider at the beginning or end of the product life cycle when the customer needs parts or prototypes quickly.
"If the customer's product has come to market and he needs parts, the traditional steel tool still has a couple months' lead time," he said. "If he needs parts now, we are going to provide those production-grade parts of the same quality as the traditional tool, but we are going to be faster, with a lead time of a couple days or weeks."
"It won't be a million parts, but it can be 10,000 parts," Cretella said.
At the end of a product's life cycle, when the volume of parts needed is tapering off and no longer justifies steel tool molding, Protolabs can provide a couple thousand parts at a time, he said.
He said Protolabs has provided more than 10,000 of the same 3-D printed parts to a single customer over a year. "Once you get the machine dialed in, you just let it run," he said.
The ability to produce a part one year from now that is exactly the same as one produced today sets Protolabs apart from many 3-D printing service bureaus. "That is something a customer can come to Protolabs for and know they are going to get consistent parts time and time again," Cretella said.
Consistency is one of the reasons Protolabs modifies all its printers. For small parts that need extremely fine details, Protolabs has modified some of its Viper SLA printers from 3D Systems and developed a proprietary resin. The modified Viper can build parts with a .001-inch layer and minimum feature size of .0025 inch. Normal resolution would be a .004-inch layer and a .01-inch feature size. To achieve the finer detail, Protolabs modified the Viper's optics, laser and internal workings.
Protolabs' proprietary resin, called Micro-Fine Green, is a thermoset material similar to ABS. Most parts built with this resin are no more than 1 inch by 1 inch by 1 inch. A microscope is generally needed to see details.
"We are always looking for ways to jump the process," Cretella said in referring to the printer and resin modifications.
Cretella said the MJF process is the most commonly used to bridge the gap from prototype to end-use part because of the quality of the part it produces.
"People are looking at 3-D printing in terms of 'Can I actually use this for my production part? Can I use this for smaller runs?' They can get from hundreds of parts to thousands of parts without building a steel tool."
He said some of Protolabs' customers in the medical and aerospace industries are especially keen on building production parts with the MJF and SLS processes. "We are starting to see a shift in thinking that 3-D printing can be used for production parts."
Protolabs builds approximately 3.1 million parts a month. More than 70,000 parts a month are 3-D printed. Protolabs' customers range from backyard engineers to major medical and aerospace company engineers.
The North Carolina plant runs 24/7. Protolabs also has 3-D printing capacity in Germany.
Protolabs' 3-D printing business is changing as more of its OEM customers acquire their own printers.
"A lot of our customers have their own 3-D printers now and are experienced in building parts in-house," he said. "They come to us to handle specialized materials, overflow work they cannot handle and sometimes just for speed. Their shop might be backed up a couple days, and we get the part to them the next day. That is the benefit of what we do."
Protolabs is constantly testing new 3-D printers. "Once we have vetted the technology, we start buying multiples of that machine," Cretella said. The company needs multiple versions of each machine to support its customer base.
"Most molders cannot vet new machines the way Protolabs does," Cretella said. "We have a dedicated team that looks at how it works; we test the speed, reliability and material properties before we offer a process to our customers."
So what is ahead for 3-D printing in the plastics industry?
"We are starting to see material development really come into its own in terms of providing 3-D parts with the same material properties as injection molded parts," Cretella said.
"I think we will continue to see the process refined to increase not only the speed but the consistency we can produce parts to be able to match injection molding's consistency. Those are the two main things we will see in the next couple of years," he said.
"Improvements in materials and printer speed is happening now. It is not something that will happen in the distant future," he said. "It reduces the break-even point when you compare 3-D printing to injection molding."
Cretella said that as the 3-D printing market continues to grow, manufacturers are developing printers for users who are pushing the boundaries of what 3-D printing can do. "I think we are seeing that now," he said. "In the next five years, we are going to see things come on the market that will be game changers.
Ron Shinn, editor
Contact:
Protolabs Inc.Maple Plain, Minn., 877-479-3680,
Ron Shinn | Editor
Editor Ron Shinn is a co-founder of Plastics Machinery & Manufacturing and has been covering the plastics industry for more than 35 years. He leads the editorial team, directs coverage and sets the editorial calendar. He also writes features, including the Talking Points column and On the Factory Floor, and covers recycling and sustainability for PMM and Plastics Recycling.
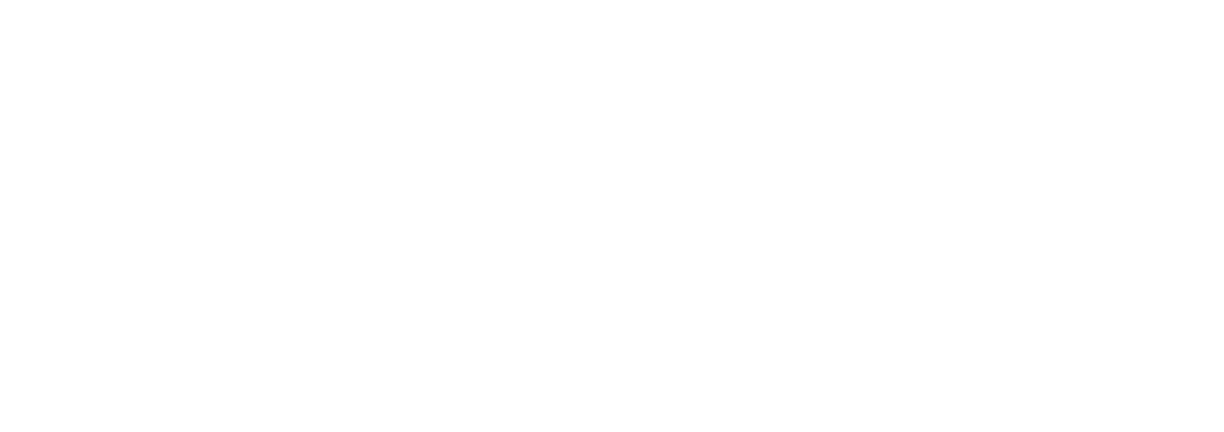