Textile firm Unifi builds capacity to make recycled yarn
The idea was a modest one in the beginning. Unifi wanted to divert waste it generated back into the polyester yarn it manufactured.
That was 2006, and during the next 10 years, the North Carolina-based company built vertically integrated capacity to produce 50 million pounds of recycled synthetic fiber — about one-third of the 150 million pounds of partially oriented yarn (POY) it manufactures each year. Total investment is about $53 million.
Unifi's trademarked Repreve brand of recycled yarn has become a star among Unifi's brands, appearing in well-known labels of premium performance clothing and other products. The Repreve brand has given a boost to a 46-year-old textile company, which suffered from foreign competition that devastated the American textile industry. Unifi is publicly owned and traded on the New York Stock Exchange.
"In 2006, we started to integrate some of our own post-industrial fiber waste back into our products," said Corey Tate, product development manager at Unifi's Repreve Recycling Center in Yadkinville, N.C. "We sent our POY waste out to converters, and they converted it into Repreve chip [flake] for us.
"Then, we started buying bottle flake. But quality is important to our product, and we had to work with our converters to improve filtering of the recycled material so we could better process it during spinning," Tate said.
Finished resin made from recycled material is extruded again through a spinneret to make the tiny filaments — finer than a human hair and difficult to see without a bright light.
The filament is made into a yarn that can be woven or knitted and is textured to make it look and feel more natural. The quality and consistency of the Repreve resin are important to ensure that the fabrics made from Repreve yarn are as good as those made from virgin materials. That means the yarn can be dyed in the same way and not have any variations, and the yarn should run at the same speed on the weaving and knitting equipment.
POY can be stretched to 50 percent more than its original size. The process is done in downstream texturing to orient the polymer to achieve needed evenness, strength, shrinkage and elongation properties.
Unifi made the decision in 2011 to install equipment to start processing its own Repreve resin. A team talked to equipment suppliers and ran numerous tests, with Austrian manufacturer Starlinger winning the first order for two complete lines.
"Starlinger had the best knowledge of polyester," Tate said. "Unifi likes to partner with companies that can look beyond what they already have available and work with us to find customized solutions. From Day 1, we could tell Starlinger was that company."
The first two lines installed in 2011 in the new Repreve Recycling Center were a RecoStar Universal hybrid line and a RecoStar PET line.
The RecoStar Universal line has capacity to process 12 million to 14 million pounds per year of post-consumer or post-industrial material. "Combining flake and fiber had never been done before," Tate said.
Alan DiUmberto, sales manager for the recycling division of American Starlinger-Sahm, said that Unifi wanted the ability to process post-consumer and post-industrial material in the same line because that is what they had.
"We started with a Universal line and modified it to make that possible," he said. He declined to give details on the changes made to the equipment.
The RecoStar PET line, specifically designed to recycle PET, has capacity to process about 28 million pounds per year. The line has a two-step process to filter the material down to 25 microns.
"The recycled material is going back into a first-quality product," DiUmberto said. "Filtering is very important. Every wash line produces a different quality of flake, and Unifi was buying flake from many different recyclers. They had to be able to take all these material strains and turn them into a first-quality finished product."
A third line, a Starlinger RecoStar Dynamic, was added in 2013. Unifi's staff calls it "The Beast" because it can process just about any material and has a yearly capacity of 26 million to 27 million pounds, depending on the material.
Line 3 includes an agglomerator. "We are looking into even finer filtration to improve quality," Tate said.
The third line also uses an infrared dryer from Germany's Kreyenborg to crystalize pellets.
Another RecoStar Universal line is scheduled to go into operation next month, which will give the facility the capacity to process more than 100 million pounds of post-consumer and post-industrial waste a year. The current facility has space to add a fifth line.
In all, Unifi has invested about $25 million in the 135,000-square-foot Repreve Recycling Center since 2011.
A key part of the equipment Unifi uses is a ViscoStar SSP reactor. The solid-state polymerization unit increases the intrinsic viscosity of PET Repreve resin and at the same time decontaminates it so that it can meet food-contact standards. A second SSP, also from Starlinger sister company ViscoTec, will be installed this summer.
Heat from pellets coming out of the SSP is captured and diverted back to an extruder or dryer. This results in up to a 10 percent energy savings for the plant. Starlinger builds much of the auxiliary equipment used in its lines, including underwater pelletizers and screen changers, but the dryers are from Italy's Piovan, represented in the U.S. by Universal Dynamics, and some melt filters are from Kreyenborg. The shredder is from Lindner-Recyclingtech in Austria.
All extruders are equipped with optional Starlinger degassing units.
To further control resin quality and achieve vertical integration of its Repreve line, Unifi invested $28 million to launch its own bottle-washing facility in August 2016. It is in nearby Reidsville, N.C., and can produce about 75 million pounds of recycled bottle flake from 125 million pounds of post-consumer PET a year.
"Our goal is to produce 100 percent of our flake internally," Tate said.
The new, 150,000-square-foot Repreve Bottle Processing Center features front-end separation equipment from Bulk Handling Systems (BHS) and nine optical units with in-flight sorting technology from National Recovery Technologies (NRT), a wholly owned subsidiary of BHS. Optical separation units remove non-PET plastics from the raw material stream and can process 22,000 pounds of per hour.
Italian machinery manufacturer Amut designed, built and installed the PET washing line. A separate Amut process removes shrink-sleeve labels from the bottles.Tomra Autosort Flake equipment sorts the washed and chopped flake a final time to ensure that impurities have been eliminated and color and flake size are consistent. Tomra is represented in the U.S. by Van Dyk Recycling Solutions.
The company expects the washing facility to be able to process 42 million bottles per week by this summer. The cleaned flake is sent to the Repreve Recycling Center where it is turned into pellets and POY fiber. Unifi has an extensive testing laboratory to monitor material quality. In one test, the lab uses a small single-screw extruder from Germany's Dr. Collin to extrude material for 10 minutes through a 5-micron filter. The filter is then checked to determine if the material is contaminated.
Once the recycled material has been processed, the resin goes to Unifi's spinning plant, where some of the 36 extruders from Oerlikon Textile turn it into POY Repreve yarn.
As the Repreve brand has grown, Tate said the company has looked to other raw materials such as post-industrial drawn fibers, which look like cotton, from cut-and-sew manufacturing operations. Film and thermoformed waste are other possibilities.
In late 2013, Unifi started selling some of its Repreve resin to other manufacturers for use in nonwoven, thermoformed and packaging products.
Tate said the Repreve resin Unifi produces is all "first-quality" and performs like virgin material. "For the most part, our goal is to make a drop-in product for our customers — whether that's Repreve chip or fiber."
Last month, Unifi's recycled PET resin received an FDA letter of no objection for food packaging. The letter covers clamshells, trays and baskets used at room temperature or below for fruits, vegetables or eggs.
About 150 people work in the recycling operation, including the washing operation. It runs 24 hours a day, seven days a week.
"In 10 years, we went from producing no recycled fiber to about 70 million pounds today, and it started with an effort to not send waste from the spinning department to the landfill," Tate said. "We have built the Repreve brand on quality, and we are very proud of it."
Ron Shinn, editor
Contact
American Starlinger-Sahm Inc., Fountain Inn, S.C., 864-297-1900, www.starlingersahm.com
Amut North America, Vaughan, Ontario, 905-761-9400, www.amut.it
Bulk Handling Systems (BHS), Eugene, Ore., 541-485-0999, www.bulkhandlingsystems.com
Collin Lab & Pilot Solutions Inc., Norcross, Ga., 678-325-6708, www.drcollin.de/en
Kreyenborg Plant Technology GmbH & Co. KG, Senden, Germany, 49-2597-93997152, www.kreyenborg.com/en
Lindner Resource America LP, Tucker, Ga., 770-349-6319, www.lindner-resource.us
National Recovery Technologies LLC, Nashville, Tenn., 615-734-6400, www.nrtsorters.com
Oerlikon Textile Inc., Charlotte, N.C., 704-916-4268, www.oerlikon.com
Unifi Manufacturing Inc., Greensboro, N.C., 336-294-4410, www.unifi.com
Universal Dynamics Inc., Woodbridge, Va., 703-490-7000, http://unadyn.piovan.com
Van Dyk Recycling Solutions, Stamford, Conn., 203-967-1100, http://vdrs.com
Ron Shinn | Editor
Editor Ron Shinn is a co-founder of Plastics Machinery & Manufacturing and has been covering the plastics industry for more than 35 years. He leads the editorial team, directs coverage and sets the editorial calendar. He also writes features, including the Talking Points column and On the Factory Floor, and covers recycling and sustainability for PMM and Plastics Recycling.
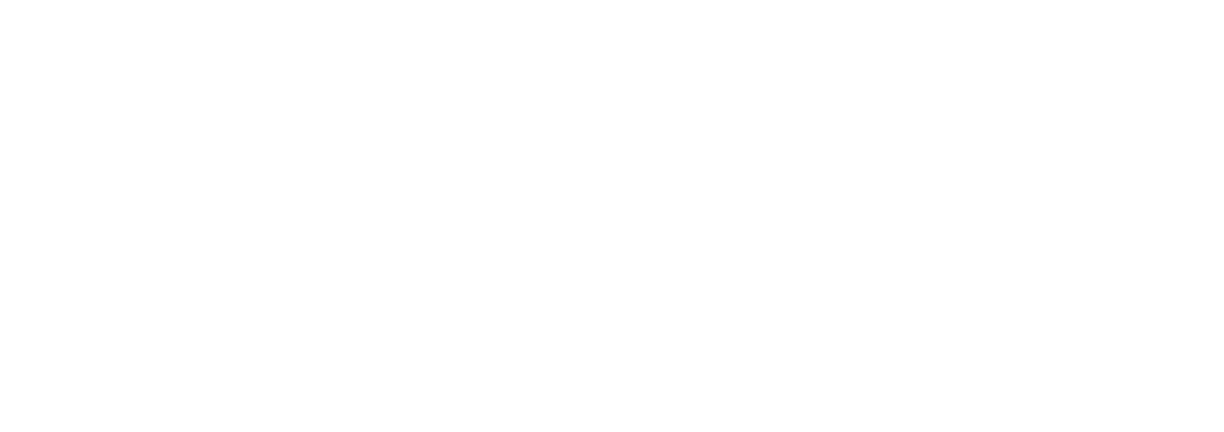