Additive manufacturing machines that can handle bigger runs and engineering-grade materials dominated the K show and formnext, an additive manufacturing show held last November in Frankfurt, Germany.
At formnext, Farsoon Technologies, Changsha, China, introduced its 403P PLS system equipped with a high-temperature build chamber for processing polyamide 6 (PA 6). It developed the plastic laser-sintering machine in cooperation with BASF, Ludwigshafen, Germany, a major global producer of PA 6, which is less expensive than the PA 12 typically used in additive manufacturing.
PA 6 powders require higher and more homogeneous print bed temperatures and a stable nitrogen atmosphere compared to other plastics used in laser-sintering systems.
"BASF is positively impressed by Farsoon taking leadership by reducing costs of plastic part fabrication simultaneously with increasing performance and functionality in laser sintering," said Dirk Simon, 3-D printing business director for BASF New Business GmbH. "Based on improvements with economy of scale, BASF supports this approach for more affordable PA 6 parts fabricated by laser sintering [by] reducing the price of BASF Ultrasint PA 6 powder by up to 20 percent for higher purchase quantities, effective immediately."
Farsoon was founded in 2009 by Xu Xiaoshu, who had previously worked with selective laser sintering (SLS) at DTM Corp., Austin, Texas, and 3D Systems Inc., Rock Hill, S.C., which acquired DTM in 2001. The company's SLS machines are open access, allowing customization by end users. In the U.S., the 403P PLS is available through Prodways Americas, Liberty Hill, Texas.
Simon said in an interview at the K show that Farsoon was the only additive manufacturing equipment supplier that was willing to jointly develop equipment for PA 6.
Arburg GmbH + Co.
Arburg GmbH + Co., Lossburg, Germany, is pursuing an open materials strategy with its Freeformer 3-D printer, which was introduced at K2013 and shown at K2016 with improvements.
One Freeformer at the K show made parts with polyetherimide (PEI), and a second produced a model of a toggle clamp with moving parts. A third Freeformer made luggage tags in Arburg's Industry 4.0 demonstration.
The significance of the first demonstration was the Freeformer's new ability to process high-heat engineering plastics. Use of advanced plastics is one of the holy grails of 3-D printing, which has formerly relied on cheaper resins with lower thermal values, such as polylactic acid (PLA) and ABS.
The second demonstration showed how the Freeformer can make complex functional parts without high unit costs. The part was produced from ABS in continuous operation day and night. A second discharge unit applied the support material required for complex geometries. After the support structure was dissolved, the model had 30 moving joints, just like the toggle clamp of an injection molding machine. It weighed about 1.6 pounds.
The luggage tag demonstration showed the ability of the Freeformer to customize parts.
Stratasys Inc.
Mass production on 3-D printers is a goal at Stratasys Ltd., Eden Prairie, Minn.
Stratasys announced at formnext that its next-generation, high-volume Fortus 900mc printer can use the company's just-developed FDM nylon 6. The fused-deposition-modeling printer addresses three trends seen at the K show and formnext: the need for longer operating runs, faster speeds and more resin options. Stratasys says that FDM nylon 6 is strong enough to be used for prototyping, or in the manufacture of tooling and customized, end-use parts.
With a build size of 36 inches by 24 inches by 36 inches, the platen of the Fortus 900mc can support two build zones. It can produce parts to an accuracy of within 0.0035 inch or within 0.0015 per inch, whichever is greater.
Stratasy is also promoting its Xtend 500 Fortus Plus, a filament package that contains 500 cubic inches of thermoplastic material, five times more than a standard canister. With it, users can achieve longer production runs. And large parts can be printed faster with an optional acceleration kit.
EOS GmbH
At the K show, EOS GmbH, Krailling, Germany, introduced the P 770, a high-throughput, direct-laser-sintering system with two 70-watt lasers used to produce large plastic parts. Parts almost 3.3 feet long can be made on the system.
Bernd Wiedmann, export sales manager at EOS, said in an interview at the company's booth that the machine can make parts from 10 different plastics in 18 combinations of materials and layer thicknesses. EOS is manufacturing air ducts on the P 770 for use in its own equipment, using PA 2200. The parts are installed into the EOS M 290 metal 3-D printer. As many as four of them can be manufactured at one time. Production time is 20 percent shorter than with the previous system, according to Wiedmann.
EnvisionTEC
One year after launching its Vector 3SP, EnvisionTEC, Dearborn, Mich., showed an upgrade — the Vector Hi-Res 3SP — that offers nearly twice the resolution of the original. The 3-D printer, which debuted at formnext, makes use of the company's scan, spin and selective photocuring technology to process a variety of proprietary materials, including ABS resins and a transparent alternative to glass; it can also use E-Tool, which is designed for the manufacture of molds. The printer has a build envelope of 11.8 inches by 6.9 inches by 7.9 inches, and a resolution of within 0.002 inch.
Carima
Carima Co. Ltd., Seoul, Korea, showed its new digital light-processing printer, the DM250, at formnext. With a footprint of about 2 feet by 1.5 feet by almost 5 feet, it has a build size of about 10 inches by 5.5 inches by 10 inches. It can lay down a layer as thick as 1.5 inches per hour and can use a variety of photopolymer resins to perform a wide range of applications, including prototyping.
Dolomite Microfluidics
Dolomite Microfluidics, Norwell, Mass., has developed a 3-D printer that makes microfluidic channels from cyclic olefin copolymers — hard, translucent, biologically compatible polymers. The printer, called Fluidic Factory, can be used to make microfluidic chips, valves and medical devices. Potential applications include research, education, drug development and carbon sequestration. It can print small parts measuring about 0.6 inch by 0.6 inch by 0.08 inch in 20 minutes, or large parts measuring 3.3 inches by 2 inches by 1 inch in 24 hours.
Doug Smock, senior correspondent
Contact:
Arburg Inc., 860-667-6500, www.arburg.com
Carima Co. Ltd., 82-70-4044-3760, www.carima.com
Dolomite Microfluidics, 617-848-1211, www.dolomite-microfluidics.com
EnvisionTEC Inc., 313-436-4300, https://envisiontec.com
EOS of North America Inc., 248-306-0143, www.eos.info
Prodways Americas, 763-568-7966, www.prodways.com
Stratasys Inc., 952-937-3000, www.stratasys.com
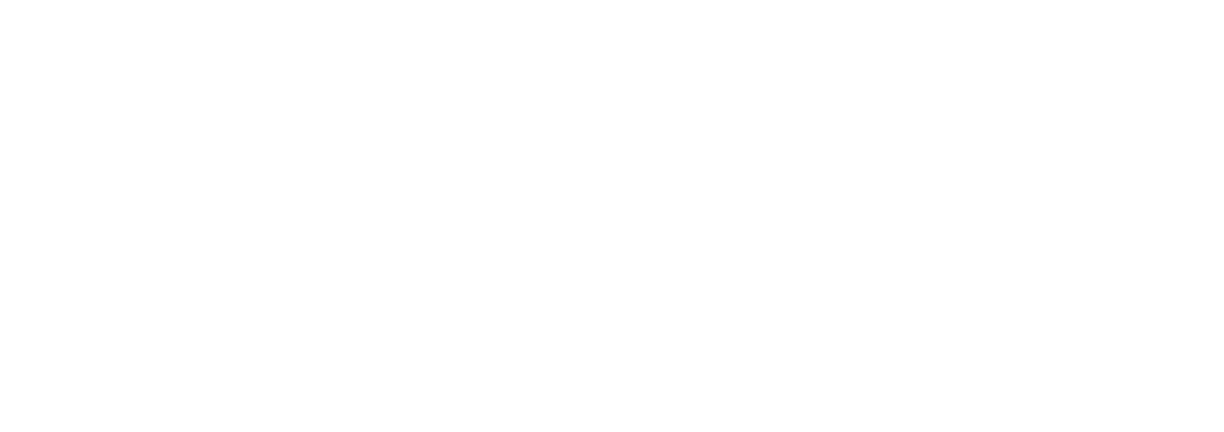