Machinery manufacturers can take several paths when developing new equipment. They can build what they think their customers want (and will buy), they can survey customers formally or informally, or they can collaborate with other machinery manufacturers.
Collaboration between two companies is the path less traveled, but you can argue that two companies that apply their unique expertise to a manufacturing problem can bring a better solution to the marketplace, which, in turn, is better for processors.
Some great examples of collaboration have shown up recently.
Senior Correspondent Doug Smock reports on a collaboration between NGR-Next Generation Recyclingmaschinen GmbH, Feldkirchen, Austria, and Kuhne, Sankt Augustin, Germany, to build an integrated system consisting of a shredder, feeder, extruder and sheet line to make virgin-quality PET sheet from recycled PET. The partnership was announced at the K show.
NGR, which has a U.S. sales office in Norcross, Ga., supplies a wide range of recycling equipment. It is also known for its P:React equipment, which uses liquid-state polycondensation (LSP) technology to improve recycled PET and remove contaminants. Kuhne is a specialist in sheet extrusion equipment.
The ability to produce high-quality PET sheet from low-cost scrap is a significant step forward.
Also at the K show, Erema Engineering Recycling Maschinen und Anlagen GmbH, Ansfelden, Austria, and KraussMaffei Berstorff GmbH, Hannover, Germany, announced they have teamed up on an integrated recycling and re-compounding line.
Erema, with a U.S. office in Ipswich, Mass., is contributing its Intarema recycling technology, which provides filtration, homogenization and degassing of the recycled material. KraussMaffei, which has a U.S. sales office in Florence, Ky., provides the re-compounding extruder.
The process uses two extruders on a single line so the material does not have to be reheated. The system saves energy and improves material quality by minimizing shear.
Erema was also part of a four-organization group at the K show that recycled about 33 tons of plastic waste generated during the event (See PMM December 2016, Page 46). The other partners included resin manufacturer Borealis AG, Vienna; recycling trade group Plastics Recyclers Europe, Brussels; and the European Plastics Converters, Brussels, representing processors.
Erema CEO Manfred Hackl said that every individual member of the value chain has to think one step ahead for the recycling industry as a whole to be successful.
The development of 3-D printing technology also offers opportunities for collaboration.
Check out Smock's story about Farsoon Technologies, Changsha, China, developing a new plastic laser-sintering system for processing polyamide 6 (PA6). The machine was developed with BASF Group, Ludwigshafen, Germany, and announced at the formnext show in Frankfurt in November.
Being able to use PA6 offers significant cost savings in processing large-volume parts. According to BASF, Farsoon was the only additive manufacturing equipment company it could find to tackle the resin.
There are other examples of collaboration by noncompetitive companies; these are just a few recent examples.
Developing new processing equipment is a long and costly process for manufacturers. Two or more companies working together can probably push the technology envelope further and more quickly than a single company working alone.
Processors should congratulate suppliers who find development partners. You are the beneficiary of their successes.
Don't miss the latest Plastics Recycling
You are receiving this year's first issue of Plastics Recycling magazine, published by PMM and Recycling Today magazine. It is worth taking a look.
The issue contains several new features, including technology profiles featuring three different recyclers, an interesting story about compatibilizer additives and an interview with a recycling newsmaker.
There are also product innovations, a report on recent patents for equipment and materials, a market report and a story on KW Plastics, one of the world's biggest plastics recyclers.
Plastics Recycling magazine continues to evolve as a useful tool for plastics processors and recyclers. We plan to publish three issues this year, with the other two coming in June and October.
Reader feedback is valuable to any publication and that is particularly true about a new one like Plastics Recycling. You can email me at the address below if you have thoughts about anything you read in PMM or Plastics Recycling.
Ron Shinn, editor
Ron Shinn | Editor
Editor Ron Shinn is a co-founder of Plastics Machinery & Manufacturing and has been covering the plastics industry for more than 35 years. He leads the editorial team, directs coverage and sets the editorial calendar. He also writes features, including the Talking Points column and On the Factory Floor, and covers recycling and sustainability for PMM and Plastics Recycling.
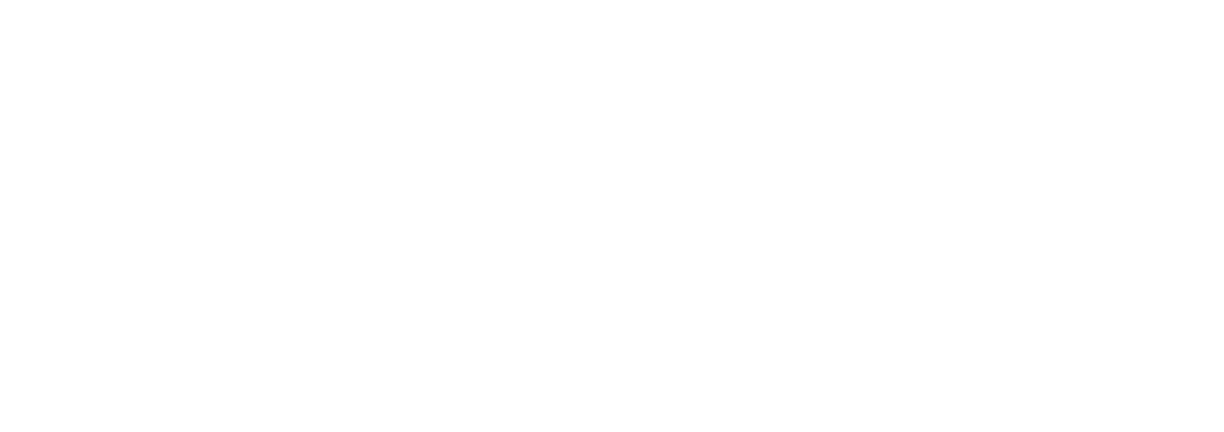