Just as they're expanding capabilities for the processing of plastics, 3-D printers are also creating new possibilities for mold makers who work with metal.
Representatives of 3-D printer manufacturers said the technology offers numerous benefits to tooling makers, as well as users of the molds. Among other advantages, they said 3-D printers provide greater freedom and can reduce production turn-around times. New printers are especially suited for sophisticated markets, such as the medical and automotive industries.
EOS of North America Inc.
"Traditional/conventional manufacturing limits you to the shape and positioning of internal geometry or passages, as you are generally working with end mills or drills," said Everlee DeWall, industrial account manager at EOS of North America Inc., Novi, Mich. "Unlike traditional CNC methods, additive manufacturing (AM) provides freedom of design, lifting the constraints of traditional machining."
EOS released its newest printer, the M 400-4, two months ago at the International Manufacturing Technology Show (IMTS). With a build volume of about 16 inches by 16 inches by 16 inches, the direct metal laser sintering (DMLS) printer can achieve build speeds of about 6 cubic inches an hour. For enhanced productivity, it features four 400-watt lasers.
DeWall said while AM poses space and cost constraints, it also presents possibilities, especially when dealing with complex molds. "There needs to be a value-add to using AM, such as incorporating conformal cooling/heating channels to optimize heat transfer and thus reducing the cycle time of the molding process. Creating hybrid tools is also another advantage which combines the best of CNC and DMLS."
EOS is one of several companies that touts the potential of 3-D printers in the optimization of the placement of conformal cooling channels. "Internal channels for cooling, heating, or both, can be positioned parallel to the corresponding mold surface. This allows for the maximum heat transfer," DeWall said.
In one example cited by the company, a European mold maker realized numerous benefits in a comparison between two molds. Using conformal cooling channels made possible by 3-D printing, the DMLS-manufactured mold required less energy for heating and cooling than a mold made using traditional processes. The energy optimization meant less corrosion and faster cycle times. Also, the mold exhibited greater resistance to wear and required less frequent maintenance.
"Thanks to the cooling channels, integrated in the component with optimum precision, we have resolved the main challenge of the production process, and done so with limited expense," said Luboš Rozkošný, CEO of Innomia a.s., Jaroměř, Czech Republic, which manufactures tooling for an automotive parts supplier.
Fabrisonic LLC
Combining 3-D printing with more traditional approaches also offers benefits. Fabrisonic LLC, a Columbus, Ohio-based startup, offers ultrasonic AM machines that have a 3-D print head and traditional CNC spindle. Unlike DMLS printers, the machines weld materials rather than melt them, so users can combine multiple materials and embed sensors, such as thermocouples and load measuring devices.
"By combining the capabilities of 3-D printing, complex internal channels and dissimilar metals, our process is able to make molds that cannot be manufactured in any other way," President Mark Norfolk said. "For molds, this allows us to mill complex internal channels anywhere in the volume of a metal part. We can combine aluminum, steel and copper all in the same part to facilitate thermal conduction and strength in specific locations around the mold."
Fabrisonic, which offers both machines and mold making services, recently upgraded its biggest machine, the SonicLayer 7200. Known by its nickname, Big Blue, it has a work envelope of 6 feet by 6 feet by 3 feet and a welding power of 9 kilowatts. It combines a five-axis printer, which can weld over curved surfaces, with a three-axis CNC milling machine featuring a 12,000-revolutions-per-minute spindle. Upgrades include modifications to its material feeding system to enable faster build speeds.
Optomec Inc.
Optomec Inc., Albuquerque, N.M., also offers machines with hybrid capabilities. At IMTS, it introduced its new LENS Machine Tool series, which incorporates AM technology into a conventional CNC vertical machining platform from Fryer Machine Systems Inc., Patterson, N.Y. Three standard configurations are offered; the most economical comes with a base price of around $250,000.
"This new product line complements our existing LENS systems and fills specific gaps for low-cost, additive-only and hybrid CNC inert systems," David Ramahi, president and CEO of Optomec, said when the new machines were released.
LENS stands for Laser Engineered Net Shaping. Drawing upon technology used in Optomec's other LENS printers, the Machine Tool series systems use powerful lasers to build structures layer by layer from powdered metals, alloys and composites. The LENS technology can be used for both component repair and tooling manufacturing.
Ken Vartanian, VP of marketing, said the systems are designed with machinists in mind, costing about half as much as other, additive-only machines.
"The subtlety here is the hybrid machine uses the same command language for both additive and subtractive operation — a language already familiar to most machinists. So learning the system becomes easy and intuitive," he said.
The approach provides benefits throughout the supply chain, according to Vartanian. He cited the use of 3-D printing to add wear-resistant coatings to materials that have been machined using traditional methods.
We have customers today who make injection mold equipment that are using 3-D printing [for] coating internal cylinder bores," he said.
Sodick Inc.
Designed especially for mold making, the new OPM250L from Sodick Inc., Schaumburg, Ill., features a 500-watt laser
that allows it to efficiently melt metal powder to create molds with build densities of 99.99 percent. The machine's laser melts the powder, then machining tools shape and finish the workpiece. The machine, which Sodick introduced in the U.S. a few months ago, can create workpieces measuring a maximum of about 10 inches in height, length and width.
Evan Syverson, Sodick's marketing manager, said the build size is typical for the technology and suitable for a number of applications, including the production of mold inserts and medical molds. He calls 3-D printing a "game-changer" for the industry.
Using a 3-D printer, mold makers can spend less time building a mold, but can command higher prices for their product due to its more efficient performance, Syverson said.
The OPM250L presents advantages when dealing with complex molds, he said. By enabling the production of comparatively high-density molds and tools, it allows mold makers to put conformal cooling channels close to the surface, improving the tools' performance during processing.
"One of our OPM customers was actually able to reduce total cycle time by 50 percent for their plastic parts due to conformal cooling," Syverson said.
The machines also help improve production times, he said. He cited one example in which a mold maker cut lead times by 55 percent using a 3-D printer. Using traditional methods, the mold would have required more than 50 components.
"Because 3-D printers can build nearly any shape, and hybrid machines can finish nearly any surface during the build, we actually reduced the design to three components — a one-piece cavity and two-piece core." Overall, the process reduced the number of required machine tools, from 20 conventional machines to just two printers.
While the technology is still evolving, Syverson is excited about its potential.
"If there is talk about reshoring U.S. manufacturing, 3-D printing is almost certainly among the biggest drivers of that for years to come," he said.
Karen Hanna, copy editor
Contact:
EOS of North America Inc., 248-306-0143, www.eos.info/en
Fabrisonic LLC, 614-688-5197, http://fabrisonic.com
Optomec Inc., 505-761-8250, www.optomec.com
Sodick Inc., 847-310-9000, www.sodick.com
Karen Hanna | Senior Staff Reporter
Senior Staff Reporter Karen Hanna covers injection molding, molds and tooling, processors, workforce and other topics, and writes features including In Other Words and Problem Solved for Plastics Machinery & Manufacturing, Plastics Recycling and The Journal of Blow Molding. She has more than 15 years of experience in daily and magazine journalism.
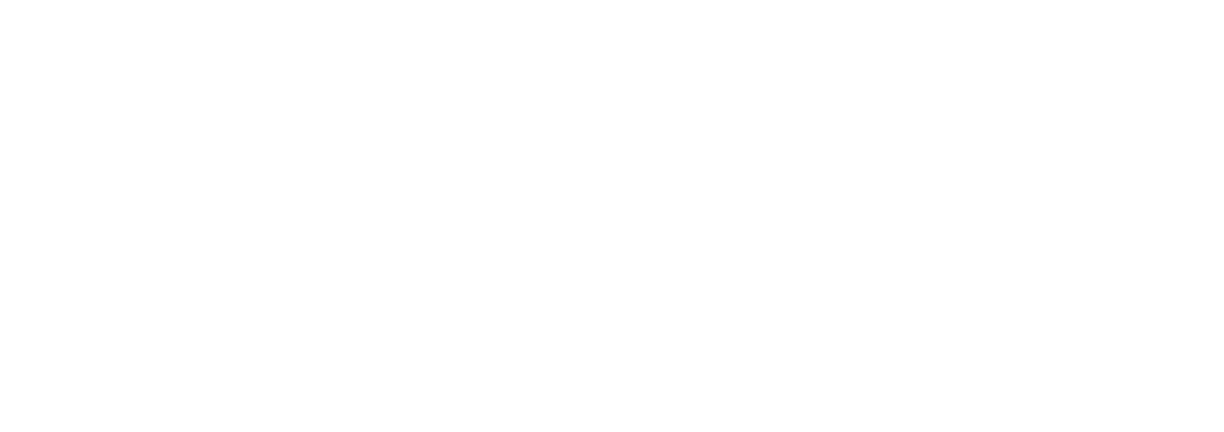