Progressive Components, Wauconda, Ill., is focused on offering more large products geared toward the automotive industry. The company debuted its larger lifter series during Amerimold in June and expanded its line of alignment locks for use on molds weighing as much as 75,000 pounds.
Glenn Starkey, president of Progressive Components, said that the company recognizes that one approach for lifters doesn't fit all applications. "We have seen repair technicians struggle with lifter assembly and maintenance in the automotive market, and we developed this series to perform well with minimal maintenance, and then, make it easier to perform and schedule preventive maintenance," he said.
A lifter is a component that allows for the molding of snap-fit undercuts, and it is designed to move with the ejection stroke. On larger molds, especially those used in producing automotive fascias and bumpers, assembly and fitting can be a two-person job requiring one person on each end of the mold.
Now, one person can load all lifters from the front of the mold and then easily complete the task from the back of the mold, Starkey said. This larger series has an adjusting mechanism so the lifter base centers itself as the mold is running. Progressive Components applied for a patent for the new size of lifters just before Amerimold.
"With these very large molds, you won't have precision movements on the plates like you would on the smaller medical molds, for example," Starkey said. "The mechanism allows for self-adjustment so that it compensates to where the plate location is. The lifter base is centering itself as the mold is running."
Previously, mold technicians or mold makers might have to set the angle in order to have the mold receive the lifter rod, but this is now addressed with the self-centering lifter base unit.
Another feature of the design is the completely secured and protected spiral cooling tubes. "A lot of times, you need cooling lines in lifters," Starkey said. The lines feed water into the lifter and direct it out. "Our design allows the lifter to slide back and forth without tubes getting pinched or leaking," he said.
Progressive Components asks its clients to provide the 3-D CAD geometry of their molds to show how undercuts will be formed. Progressive Components uses the information to make custom lifter bases.
When the Z series of alignment locks was developed, it was intended for small, medium and relatively large molds. The newest addition to the line, however, targets the larger end of the spectrum and can be used for molds as heavy as 75,000 pounds. Alignment locks for molds help protect the cavity and core inserts from damage and reduce part rejects due to flash, the company said. Progressive Components took the same materials and adapted them to the larger style.
The locks address premature wearing of the mold and increase molding precision. The series was designed with particle rings on the male surface to capture contamination and serve as reservoirs for lubricant.
"We have guaranteed lifetime performance of our Z series locks since introducing them in 2012," Starkey said. "For those who build huge molds and have asked, 'What about us?' we have answered that call." The company will display the products at the K show this month in Düsseldorf, Germany.
Angie DeRosa, managing editor
Contact:
Progressive Components, 847-487-1000, www.procomps.com
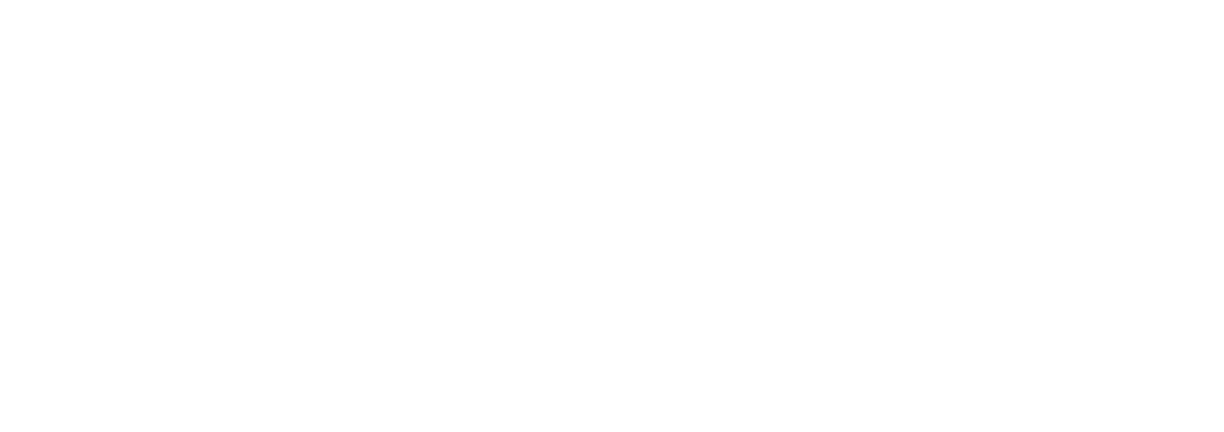