The technology used in 3-D printing for molds and tooling continues to evolve, as was apparent at both Rapid 2016, held in May in Orlando, and Amerimold 2016, held in June near Detroit. The latest updates came from Stratasys Ltd., Eden Prairie, Minn., in partnership with Hasco Hasenclever GmbH & Co. KG, Lüdenscheid, Germany, and Oak Ridge National Laboratory, which is working with Cincinnati Inc.'s Big Area Additive Manufacturing (BAAM) technology, and several industry partners.
At Amerimold, Cory Haas, an application engineer from Stratasys, and Brenda Clark, engineering manager with Hasco, presented the benefits of marrying a Hasco mold system with 3-D printed inserts to allow quick and inexpensive prototypes.
"3-D printing is really assisting us to bridge a gap," Clark said during the presentation. In particular, it allows them to bridge the prototype gap in the product development cycle where 3-D printed injection molds or components can come in handy to conduct full-range tests and do mold verification.
Hasco's K3500 mold system was equipped with 3-D printed inserts to:
• meet the requirements of manufacturing a part by injection molding;
• reduce manufacturing costs and cut delivery time by 60 percent; and
• allow for flexible color changes.
The fastest approach involved constructing a prototype tool with 3-D printed inserts and a K3500 quick-change frame to allow testing and practical trials, and then constructing a working production tool. Hasco's K3500 system was modified to include steel slide carriages, which are more robust for the injection molding process and protect all 3-D printed inserts during mold close and the build up of injection pressure. The product design was optimized for injection molding and modified to reduce mass. Officials forwarded a 3-D design of the slide to Stratasys and inserts were printed within six hours on a Connex 500 system.
Clark said that she was particularly surprised by how easy it was to go from prototype to final mold using many standard items along with the 3-D printed inserts. The other surprising finding was the time savings. Grundfos Pumps Corp., Downers Grove, Ill., is using the technology because it needed production-ready prototypes and a complex mold design with the best surface finish. It saved 50 percent over traditional aluminum prototype tooling and 70 percent in lead time.
Such inserts are best suited for applications involving glass-filled resins and resins with molding temperatures up to 570 degrees Fahrenheit, such as PE, PP, PS, ABS, TPE, polyamide, polyoxymethylene and PC-ABS. The inserts work best with parts measuring up to 10 cubic inches and presses with forces up to 200 tons.
The K3500 with the 3-D printed inserts was fitted at Canto Ing. GmbH in Lüdenscheid, Germany. The mold produced 80 parts. They were made with standard ABS at 464 degrees Fahrenheit with a cycle time of 4 to 5 minutes, which was increased due to cooling. Officials said the inserts needed too much time between cycles to cool down. Cooling still was an issue with final production so 3-D copies of the inserts were made using a technology with a high tungsten deposition. The new inserts had a 3-D filigree network of copper bronze to allow for faster cooling times on thick-walled parts. The cycle time was reduced to 19 seconds by using this new material.
Hasco is supplying quick-change mold frames and standardized components to many mold makers and molders to support this activity. The 3-D printing itself is handled by companies like Stratasys.
At Oak Ridge National Laboratory (ORNL), Oak Ridge, Tenn., researchers have been working with aircraft maker Boeing this year to demonstrate 3-D printed tools. They included tools made of separate compositions: In one case, the material mix was polyphenylene sulfide (PPS) with 50 percent carbon fiber, and in the other case, polyphenylsulfone (PPSU) with 25 percent carbon fiber. The tools were printed on a BAAM machine by Cincinnati Inc., Harrison, Ohio, and were machined on a Thermwood five-axis router.
This is the first time that 100 percent 3-D printed tools were successfully demonstrated in an industrial autoclave, which applies elevated pressures and heat. In April, four of these tools were tested at Boeing's facility in St. Louis. This means that ORNL was able to make thermoplastic molds through additive manufacturing and finish them with very little hand labor. One of the molds was 18 inches by 18 inches by 6.5 inches, but researchers, along with their industry partners, are working on bigger molds.
The cost and time involved in manufacturing composite tooling is a major obstacle, according to one official. Comparatively, each tool was printed in two hours and machined in 4 hours. The machined surface performed within the specs that ORNL was given by its industry partners on the project.
"These requirements on the material were much higher," said Vlastimil Kunc, group leader for polymer materials development at the Manufacturing Demonstration Facility of ORNL. "We had to design a new material that would be printable and would withstand the autoclave cycle. Overall, it surprised me how well the printed tools behaved through the process."
Researchers had to vacuum bag the tools in a plate because the loading conditions were quite severe. The vacuum technique helped to remove voids from within the composite structure of the tools. Voids can be detrimental to the
performance of the composite structure.
"The deformations [within the tools] we measured were very small," Kunc said. Post-autoclave laser scans of the tool's dimensions showed surface deformations measured only 0.004 inch. "To me, that was unexpected because we used thermoplastic materials under significant pressure. The material was capable of withstanding 350 degrees Fahrenheit with very small deformations." The autoclave cycle was 90 pounds per square inch.
In addition, the composite part had a good surface finish and was very easy to demold. "We didn't have to coat the tool," Kunc said. Boeing's technical staff tested the 3-D printed tools in their facility.
At the time of this writing, officials at ORNL were gearing up for another trial at another production facility, which will take place this month. The tools for this trial are significantly larger — 50 inches by 40 inches by 30 inches.
"We have learned things about the process and the requirements that we need to satisfy," Kunc said. "We went back and worked a little more on making sure that what we do can actually be used in production."
In the meantime, ORNL is conducting additional research with a third party industry partner on the chemistry of the polymers and coatings that will allow them to seal the 3-D printed tool's surface. ORNL anticipates that the resulting material will be commercially available once the project is complete.
Angie DeRosa, managing editor
Conact:
Hasco America Inc., 828-650-2600, www.hasco.com
Oak Ridge National Laboratory, 865-576-7658, www.ornl.gov
Stratasys Inc., 800-801-6491, www.stratasys.com Stratasys also has released a free guide, "3D Printing for Composite Tooling," which is available for download at www.stratasys.com/landing/composite-tooling.
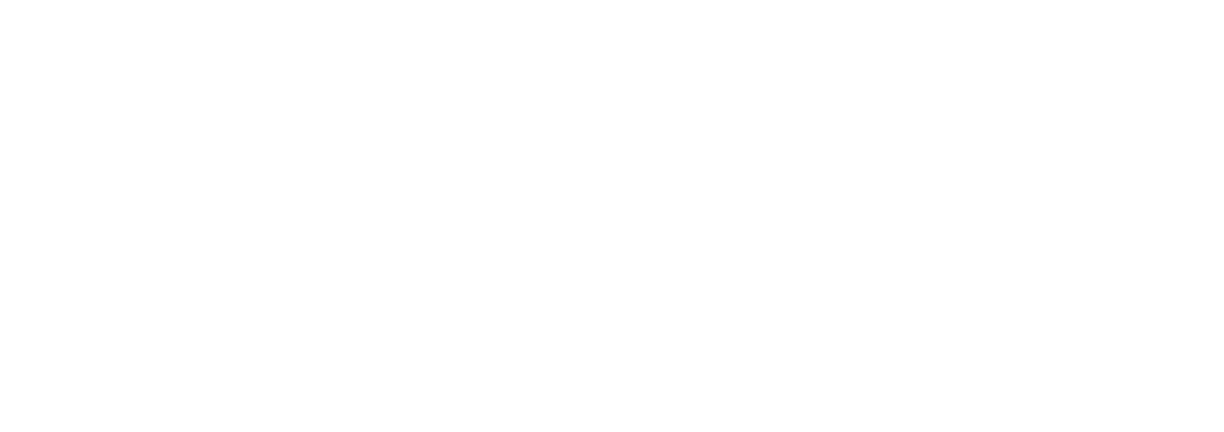