Printer maker's latest product minimizes post-processing
A 3-D printer maker has set its sights on overcoming one of the oft-cited complaints of the burgeoning technology: post-process cleanup and part preparation.
Based on its patented Augmented Polymer Deposition process, Rize, Woburn, Mass., has launched a new printer that it says requires minimal post-processing. The Rize One cuts costs, improves part strength and eliminates the need for many harmful materials, the company says.
The technology addresses challenges faced by users of other 3-D printers. In general, 3-D printers create parts by building layers of material. This layering requires the use of supports, often made of another material that can be dissolved in a chemical bath.
Imagine using a 3-D printer to make the letter T. "When you have overhangs [e.g., the crossbar of the T], you can't print those in mid-air," Rize CEO Frank Marangell said. "You have to have something that grows with it, like a scaffold." Removing the scaffolding can be a time-consuming, messy, cumbersome process. It could require that the part be sanded, filed or dipped for hours in a noxious chemical bath, depending on the composition of the support structure.
Under normal circumstances, "the removal of the scaffold takes as long as the printing," Marangell said.
By contrast, parts printed with the Rize One can be processed almost immediately, using just bare hands. "It takes 25 seconds — pop off the supports and the process is done," he said.
Two proprietary materials make this possible. Rizium One is Rize's engineering- and medical- grade thermoplastic; Release One is a repelling ink that is applied between printed parts and their support structures to weaken their bonds.
An additional advantage is that the process produces very little waste or toxic byproducts. All the plastic used in the support structure is recyclable, and many hazardous materials like those used in the chemical bathing process have been eliminated.
To further explain the company's innovation, Marangell compared the 3-D process to baking and decorating a cake. Once a baker takes the cake out of the oven, he or she must let it cool before frosting and decorating it. If 3-D printing could be applied to that cake, "with our machine, you could take the cake out fully decorated," he said.
"Companies are using it today mostly for design prototypes and marketing," he said. For example, when a company will be exhibiting at a trade show prior to production or wants to send a prototype to a store for merchandising, it can do so quickly using 3-D printing.
The Rize One technology presents additional advantages compared to other printers, according to Rize. "We [developed] a plastic that creates a strength that is almost isotropic," Marangell said. That is, it has almost equal physical properties along all axes, losing only 10 percent of its strength across the layers.
Through a direct CAD-to-printer system, the technology provides pre-process benefits and time savings, as well. Rather than designing a part in CAD and transferring it to software that a printer can read, Rize One users can eliminate the interim step because the CAD-compatible software is integrated directly into the printer. "We make the CAD file easy to print," Marangell said.
Increasing the speed at which a 3-D part can be developed also enables design improvements, Marangell said, because the more quickly and accurately users can print a prototype, the faster it can be functionally tested, improved, reprinted and retested. This is particularly critical for high-value items such as cell phones, he said.
"You can iterate more often and get a better design quicker," he said. "You know how important design is in cell phones," which need to look good and feel good in the user's hand, in addition to functioning properly. "The higher the value of the end part, the more you will prototype."
Rize One has a build size of 12 inches by 8 inches by 6 inches, weighs 135 pounds and produces layer thicknesses of 250 microns.
Rize is now performing beta testing of the Rize One with key customers. The company expects to make the printer commercially available later this year.
Lisa Jo Lupo, correspondent
Contact:
Rize Inc., 978-699-3085, www.rize3d.com
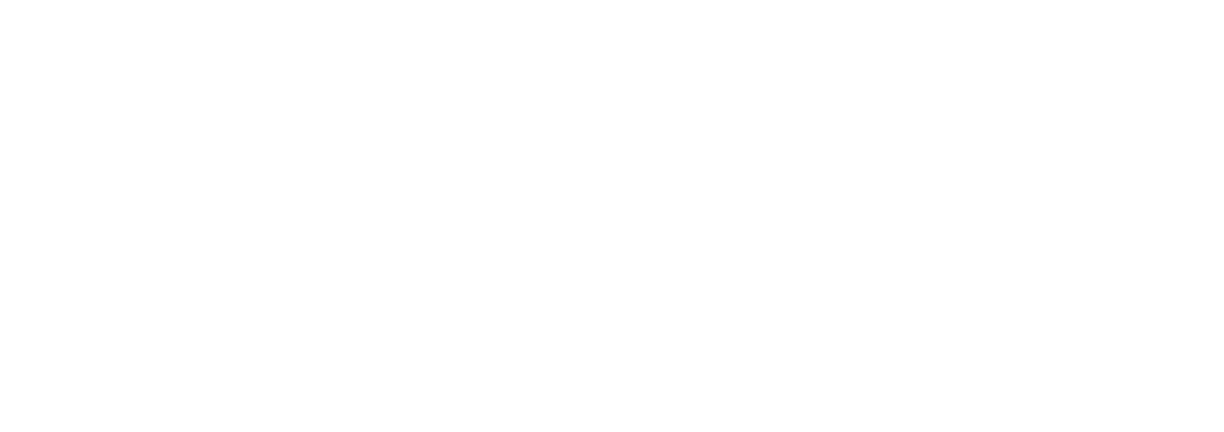