An invention from PSI-Polymer Systems Inc. of Conover, N.C., targets problems with leakage of low-viscosity plastics in screen changers.
According to the patent, leakage is often a problem on bolt-type continuous screen changers if the material's viscosity is insufficient to create a seal in the close-tolerance gaps between the screen changer housing and cross bolts.
In the new approach, a U-shaped ring seal (called a "U-Seal") is designed to move across a bore in a piston as the piston is moving, reducing the potential for tearing and leakage.
Don Macnamara, GM of PSI-Polymer Systems commented: "Material leaksfor adhesives and low-viscosity polymers are the No. 1 problem processors have when using screen changers for these applications. PSI's new seal design provides a way to prevent that from happening and offers our customers the assurance that their screen changer will perform as advertised without creating undue housekeeping and related safety issues."
One of the plastics targeted is PP with a high melt-flow index. The company said that the technology is effective for materials with viscosity as low as 1 centipoise.
The newly patented seal technology will be used on the company's continuous and discontinuous screen changers.
Patent 9,309,974; issued April 12
Other patent news:
Thermoforming. OMV Machinery srl, Verona, Italy, received a patent for a new type of thermoforming machine that it said can operate at up to 57 cycles per minute with a closed mold time of 450 milliseconds. In the concept, a pair of female molds are rotated on a support base.
Patent 9,242,403; issued Jan. 26
Compounding. A patent application was published in June for a single-screw plastication process that allows compounding in the barrel of an injection molding machine.
The patent application states: "It has now been discovered that axial fluted extensional mixing elements can be incorporated into the plastication screw of an injection molding machine in order to compound and fabricate articles in a one-step, novel injection molding process."
The patent application is assigned to Rutgers, the State University of New Jersey, New Brunswick, N.J. The inventors are Thomas Nosker, assistant research professor, Rutgers; Rutgers research associate Jennifer Lynch and Keith Luker, president of Randcastle Extrusion Systems Inc., Cedar Grove, N.J.
The concept is not all new. In 2005, Randcastle received a patent for a method for mixing plastic materials in an injection machine barrel using an elongated screw. The company has shipped close to 100 of the screws.
The idea is gaining a foothold among injection molders, overcoming the belief that only twin-screw extruders can adequately mix fillers, colorants and other additives in plastic resin.
Luker said that the technology increases mixing performance while keeping key advantages of the single screw. He said there is no sacrifice in output.
Patent application 20160167253; published June 16
Gas counter pressure molding. A Japanese invention simplifies mechanical designs for release of gas following injection of foamable resin. A gas-releasing mechanism replaces a pipe in a patent recently awarded to Sumitomo Heavy Industries Ltd., Tokyo.
Patent 9,346,204; issued May 24
Rapid tooling. Stratasys Ltd. of Rehovot, Israel, and Eden Prairie, Minn., is developing new 3-D printed molds with improved wear properties. In one recent patent application, thermoset or UV-cured plastics with different glass transition temperatures are combined. The goal is to improve the ability of the mold to endure the heat and stresses involved in injection molding while maintaining dimensional accuracy.
Patent application 20160039120; published Feb. 11
Doug Smock, senior correspondent
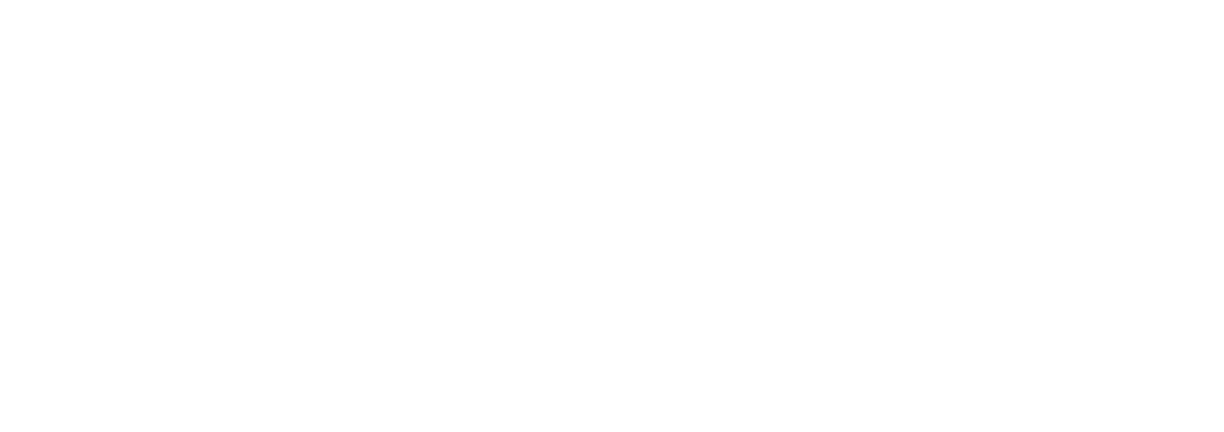