What does it take to keep the equipment in a plastics processing plant operating effectively and organized for efficiency? The question and this issue of Plastics Machinery Magazine are intended to get processors thinking about the ways in which they perform preventive maintenance, if they do.
For the topics included in this issue, we sifted through a lot of suggestions. We conducted an informal survey of officials who run factories every day. The processing plants varied in size, scope and capabilities, and the input we received was just as varied. But help for shaping the content that appears on these pages came directly from the industry. There is no shortage of topics, ranging from the biggest ticket items to the smallest. One official even suggested we might want to devote one story per month to an issue involving maintenance, repairs and operations (MRO).
Indeed, there is that much to cover and more if you consider those companies either introducing new products in this sector or even entire business units dedicated to MRO. Take, for example, Emerson Bearing Boston, which at the end of 2015 announced the formation of a special division just to cater to plastics processing. Even robust bearings can fail due to wear. Enhanced ultrasonic cleaning techniques are being used in bearings and molds and mold components. Companies like UltraSonic LLC, Cincinnati, are touting faster cleaning. Turn to Page 28 to read more about the latest mold maintenance technologies. In one example, Sidel, whose equipment includes blow molding machines, has announced new preventive maintenance services to help its customers worldwide avoid long, costly shutdowns.
On the training side, A. Routsis Associates Inc., Dracut, Mass., recently announced a program of five new online courses called The 5S System (Steps One through Five). The system is a method that describes how to manage a workspace for efficiency and effectiveness. The steps are Sorting, Straightening, Sweeping, Standardizing and Sustaining. Each area is covered in detail to ensure that work environments are clean, organized, consistent, properly maintained and up-to-date. The goal is for participants to learn the daily habits of the world's most efficient molders to establish and preserve workplace organization, according to Routsis.
"In order to be competitive in general, you need to be efficient and effective," said Dan Stephens, senior plastics engineer and a trainer with Routsis.
As technology evolves, maintenance requirements and plant organization evolve, as well. If you are an injection molder that runs electric presses, how do your repair costs compare to hydraulic technology? The same can be asked of operators of blow molding machines as they make a transition to all-electric.
Primary machinery technology aside, do you make use of purging compounds for maintaining screws and barrels?
In this computing era, let's consider how far technology can be taken when applied to predictive maintenance. There are myriad suppliers finessing technologies that will identify potential problems in production lines, before those problems occur.
MRO is getting more attention as the plastics industry overall becomes more focused on lean manufacturing practices. Part of what we do at PMM is to get inside factories — both processing facilities and those factories that are involved in making the equipment used by processors. A common theme so far has been the quest for lean and efficient operations, including environmental efficiency. Having a proactive vs. reactive maintenance approach saves money and time when companies take a long-term view, but the approach also ensures that equipment performs at a peak level.
Officials also seem to be seeking best practices from each other. People who contacted us showed special interest in temperature controllers and vacuum loaders. When it comes to equipment that requires maintenance and repair, what are the most common issues and best practices?
Does your company have a maintenance schedule that it follows? Do you view it as a priority? Any schedule for maintenance will depend on many factors, including the complexity of your operations, and the availability of skilled workers to perform that maintenance. MRO issues seem to be getting more attention, but we know that these activities can take a back seat to day-to-day production, sometimes resulting in costly machine failures.
From our perspective, this is an issue that needs more focus, which is why the timing is nice for a trade show to tackle it.
SPI will have its first MRO Expo June 8-9 at the Donald E. Stephens Convention Center in Rosemont, Ill.
We're always interested in hearing from readers about any topic, but we're especially interested in hearing about how you approach MRO. Please feel free to drop us a line at [email protected].
Angie DeRosa, managing editor
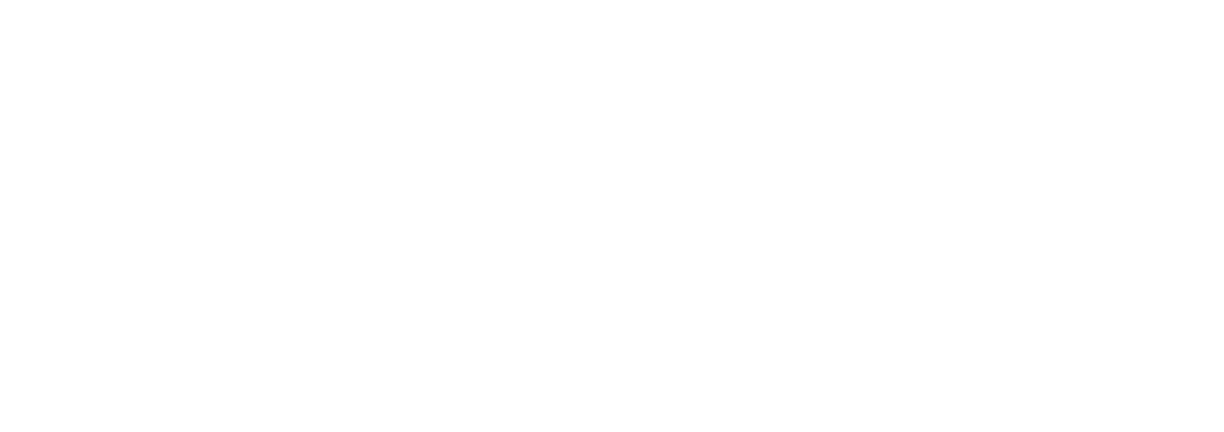