3-D: Is additive manufacturing a threat or a complement to injection molding?
If companies like HP Inc. , Palo Alto, Calif., have their way, 3-D printing technologies will become more competitive with injection molding. HP is attempting to leverage its knowledge of 2-D printing to develop a disruptive 3-D printer based on what it calls Multi Jet Fusion technology.
But if you walk the aisles of almost any major plastics trade show anywhere in the world, you'll notice that many leading companies are seeing the potential for a significant symbiotic — and not competitive — relationship between injection molding and 3-D printing.
At NPE2015, Milacron LLC, Cincinnati, showed a Stratasys Connex2 3-D printer producing ABS mold inserts. At Fakuma, Boy Machines Inc., Exton, Pa., demonstrated the production of short-run tooling on a 3-D printer from Stratasys, Eden Prairie, Minn. Arburg Inc., Rocky Hill, Conn., says it will show a Freeformer manufacturing medical parts from PC at Chinaplas this month.
The idea of using a machine to make 3-D parts from CAD files one layer at a time was first developed by 3D Systems Corp., Rock Hill, S.C., in the 1980s with a stereolithographic process that used a laser working on a photopolymer bath.
The concept morphed into much less-expensive 3-D printing when the layers were created by an inkjet nozzle that deposited tiny layers of plastic. Some pundits believe that 3-D printing will revolutionize global manufacturing, displacing processes like injection molding. That has not happened yet because 3-D printing is very slow (hours compared to seconds for molding); the plastics used are more expensive than production plastics used by molders; and the parts made by 3-D printers do not possess the mechanical properties of molded parts.
New models, such as HP's, tackle those and other problems, but the speed gap remains significant. The technologies are improving enough that many in the plastics processing industry are intrigued by the opportunities offered by 3-D printers.
One believer is Boy Machines President Marko Koorneef. "Instead of viewing 3-D printing as a threat, plastics molders should view 3-D printing as a potentially very significant value-add," he said.
According to Koorneef, 3-D-printed plastic molds can be produced overnight with 75 percent less expense than similar molds made from aluminum, which is also used for short-run pro-jects. Parts made with the molds can be used for prototyping and testing since parts are made from standard pellets in the actual machine that may be used to make production parts.
Koorneef believes such tools could be used to make up to 500 parts. The technology is a good fit for users of Boy machines, Koorneef said, because the company specializes in small injection molding machines. The company just shipped a 22-ton machine to a customer that will use its own 3-D printer to make short-run molds using digital ABS, a material that's very similar to ABS. "The customer can make his own mold slides or use MUD frames," he said.
"The real beauty is that they get parts that are just like the actual parts that will be made in the production tool," says Koorneef. "And if there is a last-minute design change they can quickly make a new 3-D mold." Three Boy customers are now using 3-D printed tools, and Koorneef believes that significant growth is coming.
In a separate example, automaker Opel Group GmbH, Rüsselsheim, Germany, is using Stratasys 3-D printers to reduce costs for assembly tools by up to 90 percent. The assembly tools, which are made in less than 24 hours, are used to attach components to the car, such as the rocker molding and roof spoilers, align lettering on the rear-side window, as well as assemble the glass and retractable roofs.
"Besides the cut in tool production time and considerable cost reductions, customized tools are a third important benefit achieved with 3-D printing. We are now able to produce more complex shapes than we could via conventional manufacturing. This crucially allows us to adapt the tool to the worker and the specific car," said Sascha Holl, virtual simulation engineer – tool design at Opel.
Arburg is so convinced of the utility of 3-D printing that it developed its own technology, the Freeformer, which debuted at K2013 in Düsseldorf, Germany.
One major advantage of the Arburg Plastic Freeforming process (APF) is its use of standard plastic resins. Many 3-D printers use expensive, proprietary materials. Some machines use regular plastics, but they are priced significantly higher when sold in cartridges for 3-D printers and marketed as digital plastic. Engineers at Arburg are working to expand the palette of plastics available for the Freeformer.
"In recent months, a number of materials and material combinations have been presented that can only be processed in this form using the Freeformer," says Eberhard Duffner, head of development at Arburg. One example is a PC-ABS blend with flame-proofing and another is a two-component planetary roller screw drive made from thermoplastic urethane and biodegradable PHA (Arboblend).
At Arburg Technology Days, from March 16-19 , three applications with new materials that are also used in injection molding on view: a two-component clip made from high-performance TPE and PP; a nutcracker made from polyamide; and an implant made from resorbable polylactic acid that dissolves inside the body after a set period.
The Freeformer now features an optimized build chamber with improved air and temperature control. "As an option, a material dryer is also available, which is integrated into the machine control system," Duffner said. Process automation is also an important goal.
Arburg believes the Freeformer will be an ideal supplement to the injection molding business.
"When a company brings a large number of new products to market every year with the need for high-quality prototypes, the potential for additive manufacturing is enormous," Duffner said. "As well as producing purely visual samples, the Freeformer can also quickly manufacture functional parts using the original materials at short notice without requiring a mold — for example, for installation trials and functional tests." This means it might be possible for a molder to dispense with expensive, aluminum injection molds.
HP launched a major research effort to overcome what it considers the most serious limitation of existing 3-D printing technology: lack of speed. Meg Whitman, president and CEO of HP sister company Hewlett Packard Enterprise, Palo Alto, Calif., once famously said that watching 3-D printing is "like watching ice melt."
HP's Multi Jet Fusion technology, which is still under development, uses a dual-carriage system that separates writing the code for the part from the function of coating/fusing the part in an effort to boost speed. The company says that its proprietary synchronous architecture is capable of printing more than 30 million drops per second across each inch of working area. The goal is a tenfold improvement in printing speed compared to currently available 3-D printers. HP says its technology can use standard thermoplastic materials.
It's not known when HP will make its 3-D printer commercially available.
Another 3-D printer company targeting injection molding is a Northbrook, Ill.-based startup called Impossible Objects LLC, which has developed a process to produce carbon fiber-reinforced plastic parts.
In the Impossible Objects process, sheets of carbon or other fiber are first fed into an inkjet printer. A layer shape is then printed on each fiber sheet with a fluid wetting agent. Plastic powder is then deposited on the sheets; the wet plastic sticks and the dry powder is removed. The sheets are then stacked and heated to the glass transition temperature of the plastic. The stack is then compressed to the final part height. Unbonded portions of the fiber stack are then removed to create the final part.
The Holy Grail for the process is manufacturing automotive parts from carbon fiber. Impossible Objects' printer is not yet commercially available.
Stratasys is the largest producer of 3-D printers and believes strongly in its application to manufacturing.
A Stratasys survey on the future of 3-D printing in manufacturing said, "The majority of respondents — both current and future users over the next three years — strongly believe that more end-use parts will be designed specifically for additive manufacturing in the future."
To encourage the use of 3-D printers, Stratasys has been supplying promotional equipment to companies like Boy at trade shows and building alliances with software giants such as PTC Inc., Needham, Mass., and Adobe Systems Inc., San Jose, Calif.
One result is the newly developed Stratasys Creative Colors Software, which is powered by the Adobe 3D Color Print Engine, for use with the Stratasys Objet Connex3 3-D printers. The software combines advanced color management with a simplified workflow from design to print.
Meanwhile, additive manufacturing is moving in new directions that also have important implications for direct manufacturing.
Massivit 3D Printing Technologies Ltd., Lod, Israel, is commercializing a technology to print large structures using a polymer gel that cures when exposed to ultraviolet light.
The machine, which costs about $400,000, has a build envelope of over 100 cubic feet. Up to about 38 square feet of object surface can be built per hour.
According to Massivit CEO Avner Israeli, the key to the technology is a gel-based dispersion approach. "Our system is much faster than filament-based 3-D printing because we are converting solids to solids," he said.
The target market is large objects used for graphic arts and advertising, as well as in theme parks. Two machines have been sold, including one recently to a company called Carisma Large Format Printing Ltd. in Brooklyn, N.Y., that specializes in large-format printing for vehicle graphics. In the U.S., Massivit is represented by Prisco Digital, Newark, N.J.
Massivit was founded in 2013 and recently got a boost with an investment from Stratasys.
Oak Ridge National Laboratory in Tennessee and Cincinnati Inc., Harrison, Ohio, are also working on large-format 3-D printing with a process called Big Area Additive Manufacturing or BAAM. In this approach, plastic filaments are cured with a UV laser to create parts that are roughly 10 times larger than those that are possible with most other 3-D printing approaches. BAAM is a hybrid technology of 3-D printing and CNC routing.
"BAAM is commercial and a true machine tool and is for sale," said Matt Garbarino, marketing manager, Cincinnati Inc.
Although 3-D printing began primarily as a rapid prototyping tool, the technology is now emerging as a significant supplement to plastics injection molding and other manufacturing processes.
A Note on Terminology
The term 3-D printing refers to the process of producing an object from a 3-D digital model by laying down many successive thin layers of plastic or other material via an inkjet-type nozzle. Additive manufacturing refers to the broader idea of creating 3-D objects from a CAD model through a variety of techniques, such as using a UV laser to harden a photopolymer bath. The term 3-D printing is often incorrectly used synonymously with additive manufacturing. A clear, definitive source is ASTM 52900, "Standard Terminology for Additive Manufacturing."
Doug Smock, senior correspondent
Contact:
3D Systems Corp.,
803-326-3900, www.3dsystems.com
Adobe Systems Inc.,
408-536-6000, www.adobe.com
Arburg Inc.,
860-667-6500, www.arburg.com
Boy Machines Inc.,
610-363-9121, www.boymachines.com
Cincinnati Inc.,
513-367-7100, www.e-ci.com
HP Inc.
650-857-1501, www.hp.com
Impossible Objects LLC
847-400-9582, www.impossible-objects.com
Oak Ridge National Laboratory,
865-576-1946, www.ornl.gov
Prisco Digital,
973-589-7800, www.prisco.com
PTC,
781-370-5000, www.ptc.com
Stratasys Ltd.,
952-937-3000, www.stratasys.com
Sidebar: Molders can get 3-D training
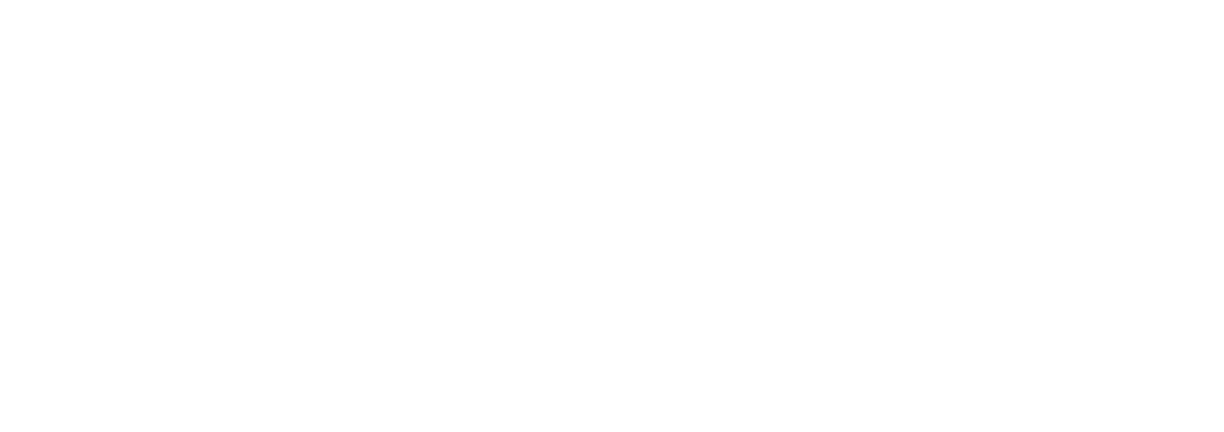