Would you buy a resin dryer without a control panel? How about a blender? Gravimetric feeder?
Before automatically dismissing the idea, consider some of the forward thinking that experts at Conair are doing. This is probably a case where you should never say never!
Chuck Morgan, training manager at Conair, gave a thought-provoking presentation at the Extrusion 2015 conference about machine controls in the 21st century. Much of his presentation was based on work done by Bob Criswell, manager of electrical engineering at the Conair Group, Cranberry Township, Pa.
Consider these points:
• When equipment is operating normally, most human-machine interfaces (HMI) are idle.
• Many machine control panels are only needed at start-up, when tending to an alarm or at shutdown.
So is there a better solution than hanging a control panel on every machine?
Most of today's machines are designed for Ethernet connectivity and therefore they can communicate with almost any computerized device.
Web-enabled machine control means equipment with an Ethernet connection can connect to a plant network and to the outside world via the Internet. This is the now-familiar arrangement that lets users control the machine from anywhere and with any device. It also helps collect and consolidate data.
Machines can also talk directly to each other. One machine can automatically make adjustments using feedback from another machine. Machine-to-machine control makes possible unattended, automated operation, faster start-up and optimized output.
Factorywide control systems take remote access to a higher level by providing a global view of nearly all the equipment in a plant. Equipment is graphically displayed to show interconnection and system dependencies.
Morgan says all of this connectivity gives plant operators information about factors such as time, as well as data and sequence logging of critical components. In a more advanced stage, this connectivity can monitor critical components' status for such things as cycle times, amperage levels, output levels and service notifications.
So if they can be controlled from almost anywhere through networks, why do machines all need separate conventional control panels?
Morgan says eliminating the "local" control panel would solve unauthorized tampering issues; provide advanced network analysis of faults; facilitate higher-functioning, system-related operations; and push processors to adopt smart services.
If there is no control panel, an operator cannot make spur-of-the-moment, unauthorized adjustments in an effort to solve a problem.
Without conventional HMIs, machines would be operated, as needed, only through the network or a portable control interface that an authorized operator or technician carries with him or her. Think about a technician walking up to a dryer connected to a tablet via a plant network. Control is married to the operator, not the device.
The technician would also have access to all the other machines in the plant, if needed. Access to machine instructions, tech notes, connection to smart services support via chat and even instructional videos could be available.
Equipment would still need the PLC or control system inside the machine, but taking away the external control panel reduces machine cost and control-panel maintenance issues.
"A processor could potentially save a lot of money," Criswell says. "Some of these HMI control panels are very expensive."
"A molder who has to make frequent changes probably needs the control panel on every piece of equipment, but an operation that is set up to run for long periods could benefit," Criswell says.
Criswell says Conair expects to start providing equipment without control panels to selected customers in the first half of 2016 and that there will be a period of collecting feedback and evaluating the strategy. Dryers will likely be first, but the principle applies to any piece of equipment with an operator interface.
"I have to think this will take off," Criswell says.
Criswell also says molders who are uncomfortable with going screen-less could take the intermediate step of using a simple, low-cost control screen with reduced functionality.
So what's next with machine controls and HMI? Criswell doesn't say, but he says that Conair is already working on future machine control strategies.
You may not be interested in checking on the status of molding machine No. 11 with your smartphone while watching the evening news, but it is nice to know that there is an operator monitoring every piece of equipment running in the plant and that an alarm will be transmitted if something runs out of spec. Someday, that operator might even monitor your machine without any "local" control panel at all.
Ron Shinn, editor
Ron Shinn | Editor
Editor Ron Shinn is a co-founder of Plastics Machinery & Manufacturing and has been covering the plastics industry for more than 35 years. He leads the editorial team, directs coverage and sets the editorial calendar. He also writes features, including the Talking Points column and On the Factory Floor, and covers recycling and sustainability for PMM and Plastics Recycling.
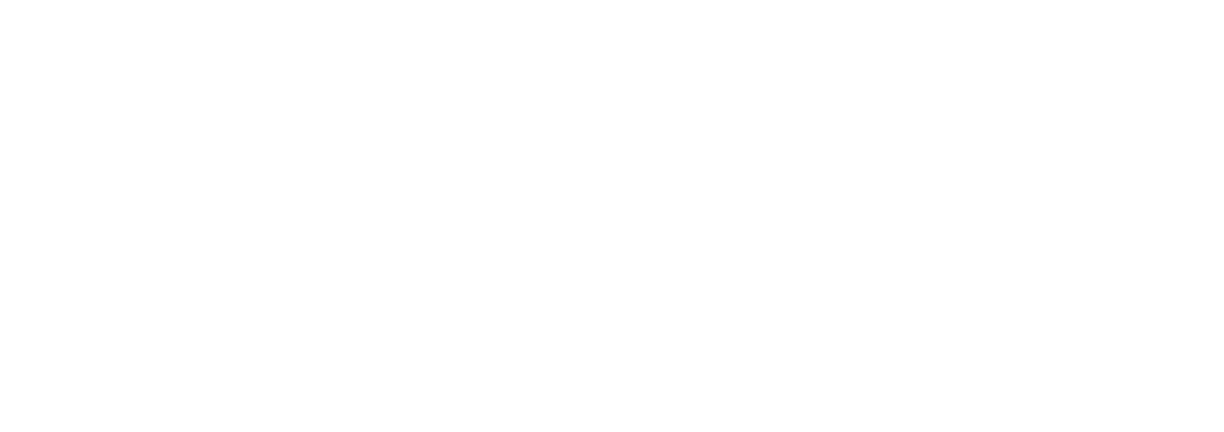