A broad German manufacturing sustainability initiative that has been visible at various shows over the last two years had no role at Fakuma last month. But it's not going away.
"Blue Competence will again have an important part to play at K 2016," says Ina Vettkötter, the initiative's project manager.
One of the most interesting things about Blue Competence is that the VDMA, the 3,000-member association of German manufacturers, launched it. In North America, sustainability has been associated more with resin makers and recycling efforts.
Approximately 400 VDMA member companies, including 55 plastics and rubber machinery companies, have signed on to the Blue Competence network. Companies pay dues to belong to VDMA and Blue Competence alliance members pay a small additional fee to fund activities, such as trade shows, education and outreach and promotional efforts.
Blue Competence has two major thrusts for machinery makers: How efficiently they run their own manufacturing operations, particularly in terms of power usage, and how efficiently they design their products so that processors can operate in a more sustainable manner.
Blue Competence's goals include shaping the world with technology, achieving more with fewer resources and being a responsible role model.
The German machinery makers recognize a key point: Sustainability and profitability are not mutually exclusive. Energy- and resource-efficient technologies, combined with responsible, long-term business strategies, are the best route to lasting economic success, Vettkötter says.
So what does that mean to makers of extruders, shredders and the like? Consider these three examples from Blue Competence partners:
Engel GmbH showed a lightweight brake pedal at NPE. Engel says the integrated process used in making the part significantly reduced the number of individual processing steps, consumed less energy and saved on handling, transportation and storage of intermediate parts. The one-step manufacturing cell also has a smaller footprint.
Vecoplan AG this year introduced its HydroDyn system that combines shredding, washing and drying of many different materials in a water-based, closed-loop process. It saves energy, eliminates the use of chemicals and includes integrated wastewater treatment. Friction created by centrifugal force in the water generates heat, which creates a hot wash system without additional power usage. Operating costs are 25 percent lower, according to Vecoplan.
Kautex Maschinenbau GmbH designed its new KBB blow molding machines for extremely short dry-cycle times and energy savings. Dry-cycle times are reduced by 25 percent, and the use of lighter materials in moving parts provides significant energy savings.
All of these examples show innovations driven by the goals of efficiency and profitability. "The goal is to explain how our member companies are attacking sustainability issues," said VDMA Managing Director Thorsten Kühmann at NPE.
But what about machinery manufacturers in the U.S.? A couple U.S.-based companies (Milacron and Nordson Corp.) that belong to VDMA because they have a presence in Germany participate in Blue Competence.
Plastics processors in North America buy plenty of primary and auxiliary equipment from German makers and thereby benefit from Blue Competence initiatives.
You could argue that U.S. equipment manufacturers already do most of the same things that their European counterparts do to build efficient and more sustainable products. They just don't have a club to formalize and promote their efforts.
But maybe they need one. Machinery makers want to be competitive in the world marketplace. They want to look like good corporate citizens of the world. They want plastics manufacturing to be a profession that grabs the attention of the best and brightest young people.
The German machinery makers are doing a better job of promoting those goals to customers and society. Blue Competence plays a big part.
Today, I doubt any processor buys a new machine solely because it is more sustainable than the old model. However, the option of using significantly less power helps drive that buying decision. For processors who have to account for every step in a long sustainability trail, energy-savings alone might not be enough, though.
"Blue Competence shows we are sustainable in energy efficiency and much more than that," says Vettkötter. "Nowadays it is not possible to look at only your plant. You have to look at every part of the chain."
There is a lot of buzz now about Industry 4.0 – the systems that will connect manufacturing components and make truly smart manufacturing plants possible. Blue Competence initiatives are likely to be closely aligned with Industry 4.0 and could speed the industry into technologies we haven't even thought of yet.
Ron Shinn, editor
Ron Shinn | Editor
Editor Ron Shinn is a co-founder of Plastics Machinery & Manufacturing and has been covering the plastics industry for more than 35 years. He leads the editorial team, directs coverage and sets the editorial calendar. He also writes features, including the Talking Points column and On the Factory Floor, and covers recycling and sustainability for PMM and Plastics Recycling.
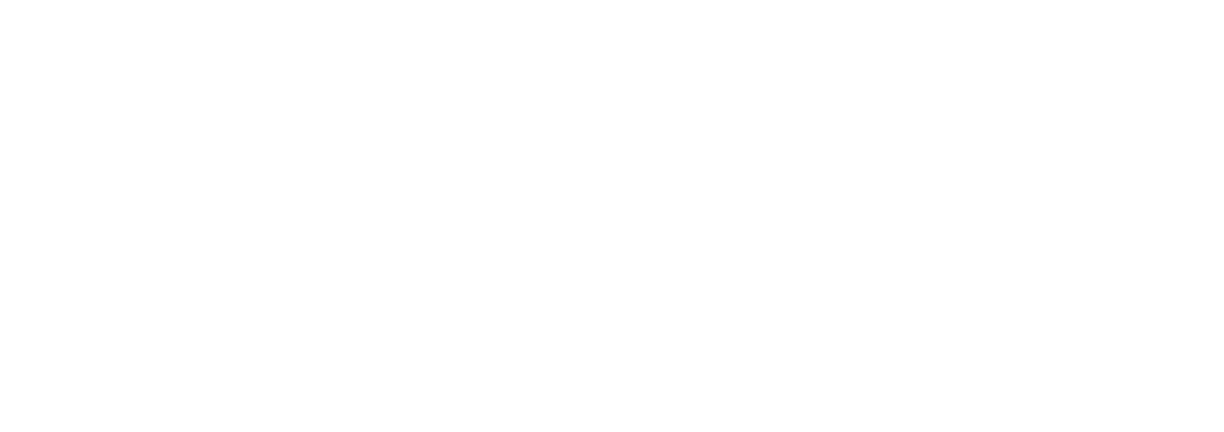