For 3-D printing at NPE, the most ostentatious display of this technology may have been in the West Hall of the Orange County Convention Center. That is where Arburg had two Freeformers, the company's North American debut of the system that requires no molds to create fully functional components and uses standard resins.
If you were at NPE and heard a saxophone in the West Hall, that music was coming from the Arburg booth. This was the accompaniment to the Freeformer presentations and it drew crowds. It wasn't the acrobatic fanfare of K 2013 but it was spectacular in its own right. Arburg wanted to draw attention and it did.
The Freeformer represents a major plastics machinery manufacturer getting into the 3-D printing business and that is game-changing. For plastics machinery aficionados, this machine is intriguing. The two machines at NPE were equipped with a part carrier that moves along three axes and two stationary discharge units. The resin is first melted in a plasticizing cylinder similar to injection molding, says Arburg. The tiny plastic droplets are built up layer by layer via special nozzles to form the finished part. At the show, one of the machines produced a fully functional bellows from TPU combined with water-soluble supporting structures. The second machine produced a key fob with an articulated joint.
But what else is being done in the world of 3-D printing across the plastics industry? Walking around the halls of the convention center, it seems that companies are gearing up to support this very robust market. The Wohlers Report 2015, released just after NPE, documents the growth of 3-D printing and additive manufacturing. The worldwide market grew at a compound annual rate of 35.2 percent to $4.1 billion. The industry expanded by more than $1 billion in 2014.
"3-D printing is taking off right now," says Chris Weinrich, general manager of downstream extrusion for auxiliary equipment maker Conair Group, Cranberry Township, Pa. Officials at the company are seeing the growth in demand for plastic rod or filament that feeds the printers.
During NPE, Conair Group showcased an extrusion line in partnership with Davis-Standard LLC, Pawcatuck, Conn. This is what made up the production line: ABS resin was dried in a Conair dryer. The model MDCW 100 conveying system loaded the resin into the extruder hopper. A 2-inch Davis-Standard Super Blue extruder fed the Conair GRH-1.0 extrusion die that was designed specifically for filament/rod production. Once that extrudate exited the die, it went into a Conair HTMP multi-pass cooling and sizing tank. The tank, pictured below, combines vacuum sizing and cooling. The filament made three passes through the tank before it went on to a precision belt puller and a Conair servo-driven automatic cut-and-transfer coiler. A Zumbach Electronics Corp. laser gauge is located at the cooling tank and puller so that diameter and ovality constantly are monitored, Conair says. This system was fully operating in the Davis-Standard booth and Conair showed a live video feed of the operating line in its exhibit.
Weinrich says that diameter and ovality are critical.
"Tight tolerances are critical for filament used on high-end printers," he says. "If diameter and ovality are off too much, the printer can misfeed."
This line has achieved throughput rates of 400 to 600 feet per minute and Conair has recorded 0.0005 inch variation on diameter and less than 0.001 inch on ovality of the filament.
The Stratasys booth, located in the South Hall, maintained heavy traffic. Attendees were milling about, taking in all the possibilities such as the Mojo Desktop 3D Printer. For $5,999, attendees could have the Mojo 3D Print Pack, which included the printer, a start-up supply of materials and bases, the Mojo Print Wizard and control panel software and the WaveWash 55 support removal system.
This model relies upon the company's Fused Deposition Modeling (FDM) technology and uses ABSplus resin, which is offered in nine colors. Many processors are using this type of technology, including Plastic Molding Technology Inc. of El Paso, Texas. The company invested in its first desktop 3-D printer last fall and uses FDM technology to make fixtures and sample prototypes.
By Tuesday of the show, Stratasys had added to its booth an injection molding machine from Boy Machines Inc. This was a maximum 11-ton press that was running at a clamping force of 1 ton to demonstrate 3-D printed molds, mold inserts, bases and ejector boxes for rapid tooling and prototyping.
The goal, said Stratasys officials, is to get a prototype tool in hand very, very quickly. A mold insert would take just a few hours to print, for example. It was printed from digital ABS. According to Stratasys, digital ABS is fabricated inside the 3-D printer and is designed to simulate standard ABS by combining high-temperature resistance with toughness.
Toshiba Machine Co. America, Elk Grove Village, Ill., also installed Polyjet injection molds into its molding machines to run prototypes at NPE. On an all-electric EC85SX (85 tons of clamping force), Toshiba had a multi-cavity tool that was aluminum, explains Steve Cunningham, sales manager for the U.S. and Canada. One side of that tool had a highly polished aluminum cavity.
"The second (side) was replaceable where we would insert a 3-D molded cavity," he says. It was an ABS composite cavity. Phoenix Proto Technologies, Centreville, Mich., supplied the entire mold and the replaceable cavities. Toshiba came prepared with 20 cavities.
"We got over 100 shots in the cavity before we had to replace it," he says. "We wanted to show several things. We wanted to show that you could 3-D mold a cavity, place it in an existing tool and have an injection molded prototype in hours.
"The important thing is to know that if you needed an injection molded part and maybe multiple parts, you would be able to do that in 3-4 hours. You could insert that cavity in an existing tool and get at least 50-100 parts depending on the life of the cavity," he says. "It's a little different take on 3-D printing. It allows you not to just print one at a time but actually have a workable prototype of your product."
The press was complemented by a Toshiba 6-axis robot that was inverted. It would pick up the mold cavity, place it into the mold, lock it in place and the machine would begin to shoot that cavity.
"This was something in our machine that we had not demonstrated before," he says, "being able to toggle back and forth from one cavity to another and the machine made all the adjustments."
Back in the South Hall and a few aisles away from Stratasys, Brandon Bell was excited to show off his iExtruder benchtop extruder, designed specifically for extruding sample filament. Bell is with B3D, a unit of Automated Manufacturing Systems, West Palm Beach, Fla., which specializes in troubleshooting and rebuilding used extrusion equipment.
"We really love 3-D printing so we wanted to find a way to essentially create a niche for ourselves," he says. "We know extrusion and we love the industry."
This machine is intended for R&D and educational use. It also would be perfect in university settings, says Bell, a mechanical engineer by training. He designed the machine. It sells for roughly $10,495 and will ship via UPS.
"The market created a need for it," he says.
The machine's features include 1.75mm and 3mm 3-D printer filaments in standard or custom colors. It will operate with ABS and polylactic acid and all engineering resins. It has precision die tips, a pulling station and a winding station. It has dual temperature controllers and a temperature capability to 475 degrees Fahrenheit. It is powered by 110 VAC and consumes 5 amps or less.
Angie DeRosa, managing editor
Contact:
Arburg Inc., 860-667-6500, www.arburg.usB3D, 561-557-8531, www.iextruder.comConair Group, 724-584-5500, www.conairgroup.comDavis-Standard LLC, 860-599-1010, www.davis-standard.comPhoenix Proto Technologies LLC269-467-8300, www.phoenixproto.comStratasys Ltd., 877-489-9449, www.stratasys.comToshiba Machine Co. America, 888-593-1616 www.toshiba-machine.com
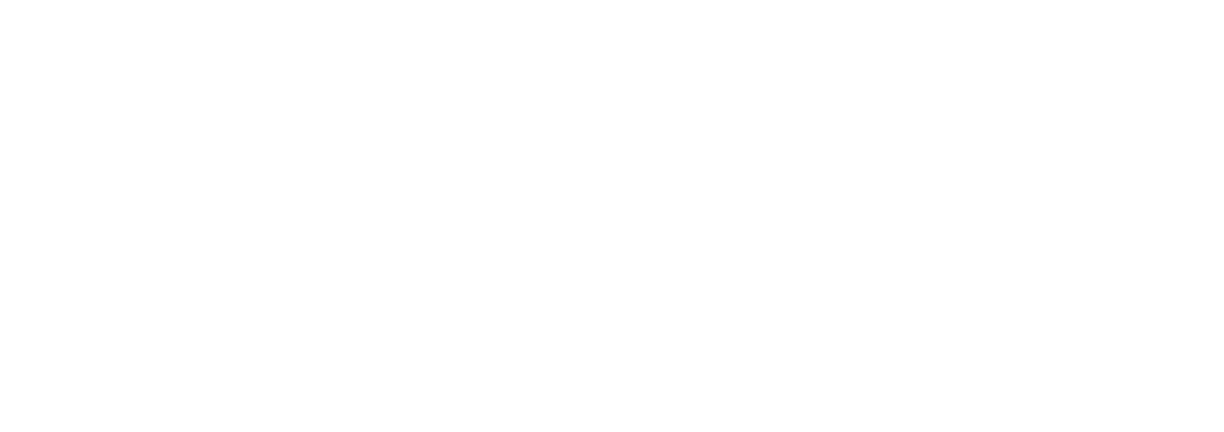