Plastics Machinery Magazine this month begins its coverage of NPE. No matter what or how you count, NPE2015 adds up to a blockbuster event that more than satisfied attendees and exhibitors. There was energy at the Orlando show that had been missing during recent, recession-burdened NPE shows.There was plenty of shiny new hardware — as well as software and gee-whiz technology such as the Start-up Garage and 3-D printing exhibits — and technical seminars.
But as I visited exhibits, I was struck by the level of sophistication that machinery and equipment suppliers have achieved.There are people in the industry who remember when injection molding machine controls consisted of two knobs. Now molding machines — along with much of the work cell's auxiliary equipment — are run via efficient touch-screen panels that are simpler to use but pack in more features.
Machinery manufacturers are now thinking about processing machines as parts of fully integrated work cells. These work cells, almost always equipped with really cool and efficient robots, were certainly evident at NPE.
Good general-purpose molding machines were not the stars of NPE2015. Machines and work cells specifically tailored for end markets created the buzz.
The PMM editorial staff collectively has 42 NPE shows under its belt, with one writer attending 11 and another attending his first show in 1973. Here are their impressions of NPE2015:
Angie DeRosa, managing editor: 3-D printing is growing up and the industry is finding out where and how to use this technology. In the West Hall, attendees were seduced by the sounds of a saxophone to stop by Arburg's booth where the Freeformer was front and center. This was the Freeformer's introduction to the North American market.
What intrigues me are the undercurrents, which could be found mainly in the South Hall. What is coming up? Stratasys kept a packed booth, for good reason. People are mesmerized by the technology and what can be accomplished with it. Stratasys had a Boy 11-ton injection molding machine on which a technician was sampling 3-D-printed molds and mold inserts. Stratasys is working with Boy; Toshiba Machine Co. is working with Phoenix Proto Technologies on these technologies. I suspect it's only the beginning for such relationships.
Rob Neilley, senior correspondent: Full disclosure — I enjoy plastics trade shows, the bigger the better. That said, I was uncertain about Orlando replacing Chicago when NPE2012 opened. I like Chicago a lot. But even before NPE2012 opened, during setup, it was clear things were going well, better than Chicago, and that continued as the show rolled on. Attendees and exhibitors both were happy. No surprise then that they spread the good word that led to a record-breaking NPE2015.
It's not just about the 2015 show stats, impressive as they are. It was the energy level — very high — and the attitude —professionally positive. It helped that the economy has been improving, especially in our manufacturing sector. It helps even more that the show had plenty of new and improved technology to see and talk about. OK, no one showed a new technology that changed how pellets are melted in half the time using half the energy and with zero material degradation. But that just might happen at NPE2018 ... in Orlando.
Mikell Knights, senior correspondent: Gee-whiz machinery and processes abounded at NPE 2015, my sixth NPE — yet the first in six years. I was impressed by Arburg, Engel and KraussMaffei's use of composite sheet and thermoplastic molding to replace steel in automotive applications, and Sumitomo's high-speed production of 1.2 gram non-carbonated water 29/25 HDPE caps in a 96-cavity mold with a 1.9-second cycle time.
You can't overlook Arburg's Freeformer building complex parts without a mold, Milacron's Klear Can and Husky's self-cleaning mold. I covered injection molding and there was plenty to impress.
Merle Snyder, senior correspondent: The dominant trend in the recycling equipment was recycling with systems, not just a machine. Even the sellers of discrete pieces of equipment, granulators for example, are getting on board with the systems approach by developing relationships with the system suppliers. Some of the "system integrators" don't even build machinery themselves, nor do they need to. If you just want a shredder, you can get it. But if you really need an entire system, you will never again have to cobble it together yourself.
The blow molding arena is characterized by suppliers eager to push the technology forward, one inch at a time if necessary, to get this year's machine to do better than last year's. Unless or until the hot-fill technology comes to fruition, the progress will not be revolutionary, but it will be real. Electric and hybrid machines, modular molds, ease of operation, and training with simulators are pushing the productivity of blow molding beyond anything heretofore seen.
Ron Shinn, editor[email protected]
Ron Shinn | Editor
Editor Ron Shinn is a co-founder of Plastics Machinery & Manufacturing and has been covering the plastics industry for more than 35 years. He leads the editorial team, directs coverage and sets the editorial calendar. He also writes features, including the Talking Points column and On the Factory Floor, and covers recycling and sustainability for PMM and Plastics Recycling.
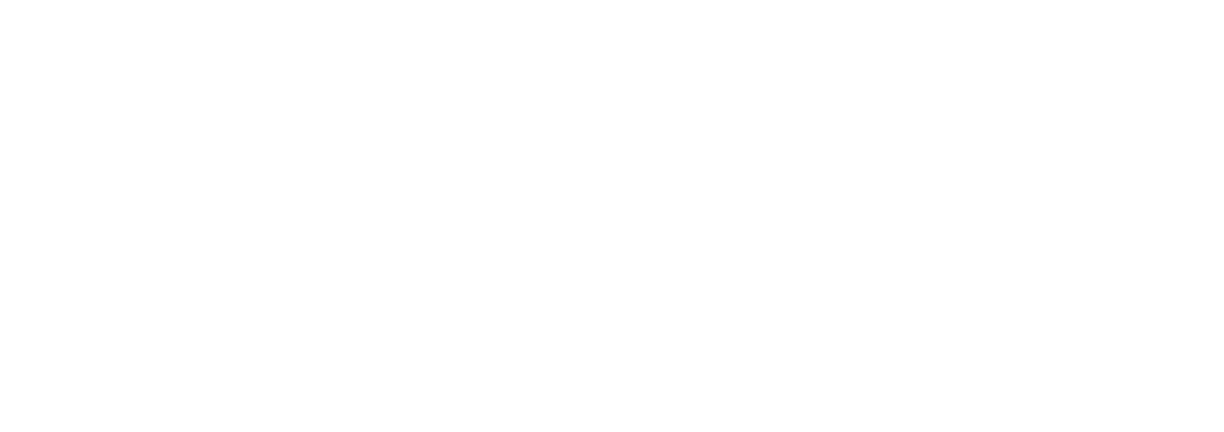