NPE is entering new territory with NPE3D, an 18-exhibitor pavilion devoted to 3-D printing technology and seven 3-D printing educational sessions on March 24. Forecasts point to exponential growth in the next 10 years for 3-D printing, which has transformed prototyping of new plastics products, making it radically faster and more efficient.
Additive manufacturing not new but ready for takeoff
Terry Wohlers started his consultancy, Wohlers Associates Inc., Fort Collins, Colorado, in 1985 and says he stumbled across the technology in 1987. First commercialized in 1988, Wohlers has been working on it ever since. The Wohlers Report is an annual report on the 3-D printing/additive manufacturing (AM) industry. Wohlers is still tabulating 2014 numbers, but the market in 2013 grew 34.9 percent over 2012 to almost $3.1 billion, which includes all products and services worldwide. From 2011 through 2013, the compound annual growth averaged 32.3 percent and 27 percent for the 25 years up to 2013.
"It's been a very strong industry in terms of growth, and though it was small for most of that time, once you get into the billions it starts to multiply quickly," he says. "We expect it to be well over $4 billion for 2014 and to triple in size over the next four years given the volume of investment we're seeing at all levels, from startups to some of the largest corporations and brands, governments, universities and more."
The markets Wohlers tracks include machines and materials, the two largest components; after-market items such as lasers and software; and the service providers performing AM for other companies that include prototypes, some tooling and, increasingly, parts for end products. About a third of the $3.1 billion in 2013 was tied to parts going into final products.
Injection molding or 3-D printing?
Multiple factors need to be considered when deciding between injection molding and AM. The size limit for most 3-D printers is about 1 meter in any direction, and parts that big take more time to make. Complexity is a strong suit of 3-D printing, as is parts consolidation.
Materials for 3-D printing are expensive, as much as 50 to 150 times the cost of comparable plastic pellets, enough to derail a conversion. However, changes during product development are much easier and faster with 3-D printing. Production volume, part complexity, material and tool costs, design and engineering changes, and more make this decision a matrix.
Wohlers sees growth opportunities continuing in aerospace and medical markets because additive manufacturing has only penetrated those sectors slightly. Jewelry could be an opportunity area, with the added benefit of being unregulated. Automotive has been a major AM user for more than 20 years for design validation; prototyping; and form, fit and function testing. End-use parts are already installed on several luxury low-volume cars, and higher volume manufacturing is in the offing, just waiting for costs, including materials, to come down. Both machine and material suppliers are working on that.
"If I were in the plastics processing sector," says Wohlers, "I could see this as a threat, or I could embrace it and say, hey, we know as much about processing plastics as anybody so maybe we should at least take a look at 3-D printing to understand what works and what doesn't."
Consumer 3-D catchy but manufacturing delivers the goods
Bruce Bradshaw, vice president of marketing at leading 3-D printer and materials supplier Stratasys Ltd., Minneapolis, points to another forecast of 3-D printing's growth. The McKinsey Global Institute estimates that by 2025 the economic impact of 3-D printing could be $230 billion to $550 billion per year.
McKinsey says the three largest 3-D printing application areas are consumer uses at $100 billion to $300 billion, followed by direct product manufacturing at $100 billion to $200 billion, and making tools and molds at $30 billion to $50 billion.
Stratasys is targeting four segments: prototyping and product development; consumer; augmented manufacturing; and end-use parts.
Prototyping and product development is not a new market, Bradshaw says, but is by no means mature. The time-to-market advantage from rapid prototypes and short production runs of realistic parts is a very real edge.
In consumer markets, 3-D printers from MakerBot Industries LLC, Brooklyn, N.Y., and others that burst on the scene in the past five years have made 3-D printing an everyday item. That awareness helps it move into the educational and commercial sectors.
In the augmented manufacturing segment, Bradshaw says that when an automaker designs a new model it also designs its production process. Numerous brackets, clamps, jigs, fixtures and other components have to be made; making them in-house makes sense.
Bradshaw notes that 3-D printing of commercial production volumes will take improvements in speeds, cycle times and materials, but those are opportunities. 3-D printing of end-use parts is not new. Boeing has put 3-D-printed ducts and brackets in its planes, commercial and military, for more than 10 years. There are about 200 of them in each modern Boeing airliner. About 60,000 people enjoy 3-D-printed titanium hip replacements.
Bradshaw says some thermoformers use 3-D-printed parts as forming tools, and Stratasys printers also are making soluble cores for carbon fiber layups that dissolve away when the job's done.
At NPE in Orlando, Fla., Stratasys will be in the NPE3D space and in its own booth (S34001). Bradshaw says a big focus will be mold verification. Many molders and mold makers already know the value of being able to 3-D print realistic prototypes in-house, but some are going further — 3-D printing a prototype mold, then molding parts in the production material. Stratasys will have an injection molding machine at NPE to show how it works. Besides having production-level parts for evaluation, changes can be made in the mold design and a new mold printed and run in a couple of days.
Engineering and design changes that would require expensive, time-consuming modifications to the mold can be made before any metal is cut. This becomes a value-added service for the designer or mold maker, and the customer saves money and goes to market quicker with a better product.
Arburg's materially different additive manufacturing
Injection molding machine maker Arburg Inc., Newington, Conn., will be presenting its Freeformer additive manufacturing system for the first time in North America at NPE (Booth W3729). The unique Freeformer was a big success when it debuted at K 2013 in Düsseldorf, Germany. Development units went to customers in Europe during 2014.
In the Freeformer, Arburg has created a patented industrial AM process that uses standard plastic pellets. Heinz Gaub, Arburg managing director of technology and engineering, says the company realized a while ago that the plastics processing market was changing. Short product life cycles, greater model diversity and a demand for customized products were creating the need to make high-quality parts in small batches or as one-off items.
Gaub says Arburg began thinking about how to make plastic parts without molds in 2004 and the idea of "free-flowing plastic droplets" led to designs and trials that yielded the patented Arburg Plastic Freeforming (AKF) process. He emphasizes that the Freeformer is designed for industrial production, for continuous use and precision, and that Arburg's initial target group is plastics processors that want to increase their flexibility and have AM in their portfolios.
Acknowledging that the Freeformer will also interest those wanting to produce prototypes and individual functional samples, Gaub adds, "I believe that we will also tap into applications and markets that we are completely unaware of today." Indeed, much of the impetus for AM growth is coming from brand owners and manufacturers, industrial designers and others who learn about it and see that it could help them.
John Ward, Arburg VP of sales and marketing, was at K 2013 in Germany for the launch of the Freeformer. "Within a half-hour of the product's release," he says, "I was getting emails from companies in the U.S." He was asked very specific questions about potential applications. For example, could a specific engineering material be used in the Freeformer?
Arburg will have two Freeformers at NPE, along with new injection molding technology. The Freeformer's benefits include zero dust and emissions and easy-to-use controls through a multi-touch interface. In addition, the machine has two discharge units, not only to make parts with two materials but to create a support structure for a complex single-material part.
How big can AM go? For now, a small car
Anyone who attended the International Manufacturing Technology Show (IMTS) in September in Chicago, or the Detroit Auto Show in January could watch as the chassis, frame and four fenders for the Strati, a new car from Local Motors, Phoenix, were made by a large, new AM system.
At the end of both shows attendees could watch the assembled car being driven away. The Strati received a lot of well-deserved media attention, but the Big Area Additive Manufacturing (BAAM) machine and its interesting backstory were under-reported. Just six months before IMTS, a partnership was formed to develop a large-scale AM system that could print polymer components up to 10 times larger than what was then possible at speeds 200 to 500 times faster than existing AM systems. The partners are the Department of Energy's (DOE) Oak Ridge National Laboratory (ORNL) and machine tool supplier Cincinnati Inc. (CI), Harrison, Ohio, in business since 1898.
ORNL received funding from the DOE to take AM to industrial scale. It knew it could develop an extruder that would deliver the layers of material. It did not, however, have a rugged, industrial-strength platform that could move the extruder head with the required precision. CI had the right skill set, being the first maker of laser-cutting systems to develop and use high-speed linear-motor axis drives with head positioning speeds up to 10,000 inches per minute.
CI CEO Andrew Jamison said, "We have the largest installed base of high-speed laser cutting systems, so this machine platform has been field tested and proven to be virtually trouble free."
Matt Garbarino, CI's marketing manager, said the BAAM system at IMTS was an alpha, and it worked perfectly. Even so, both CI and ORNL quickly went to work on improvements. The 38-pound-per-hour extrusion feed took 44 hours to make the car parts, and their size meant the parts could not be done together but rather sequentially. ORNL is aiming now for 100 pounds per hour and CI has a larger machine so more parts can be made from a single setup. It's also increasing the Z-axis to allow taller parts and adjusting the speed to turn corners better.
CI has sold three BAAM systems. One went to Sabic Innovative Plastics, which supplied the carbon-fiber-reinforced material used in the show demonstrations. Another went to Local Motors and the third was sold to an aerospace company whose engineering staff saw it work at IMTS.
Garbarino says the improved systems will be in production this year, so big things will be coming.
Rob Neilley, senior correspondent
Contact:
Wohlers Associates,
970-225-0086, www.wohlersassociates.com
Arburg Inc.,
860-667-6500, www.arburg.com/us
Stratasys Ltd.,
952-937-3000, www.stratasys.com
McKinsey Global Institute,
312-551-3500, www.mckinsey.com
Oak Ridge National Laboratory,
865-576-7658, www.ornl.gov
Local Motors,
480-371-6797, www.localmotors.com
Cincinnati Inc.,
513-367-7100, www.e-ci.com
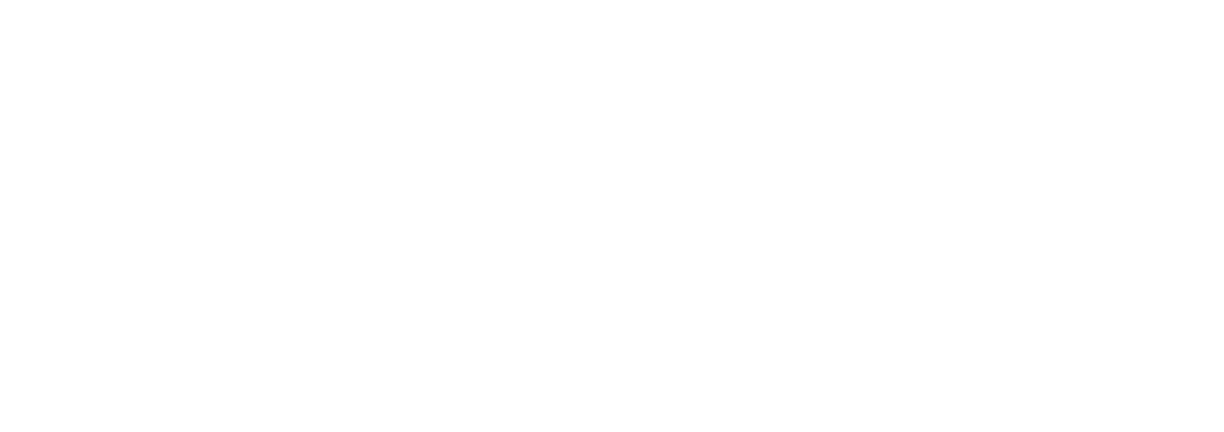