Until about a year ago, I thought reshoring was something we talked about mostly to make ourselves feel good. Sure, there were occasional anecdotes about production coming back from Asia to North America, but hadn't that always happened?
Eventually there were enough of those stories to convince this skeptic. I haven't seen statistics that track reshoring for the plastics industry, but I have seen lots of stories that indicate the trend continues strong.
So what part do machinery innovation and advances in technology play? I took a very unscientific poll of a few industry leaders who should know. They had different opinions as to the reasons for reshoring, but they all agreed that technology — and particularly processors' investments in new technology — has played a part.
"We do hear from customers looking for reshoring their molds and molding to the USA," said David Preusse, president of Wittmann Battenfeld USA, Torrington, Conn. "New innovations in plastics manufacturing equipment and energy efficiencies and use of robots and automation have greatly reduced the waste or labor requirements that once drove molding away from the USA."
Conrad Bessemer, president and CEO of Novatec Inc., Baltimore, said the mass exodus of plastic parts five to 10 years ago to Asia was often "a pendulum swing over-reaction made in many cases by financial analysts, not product managers."
But unforeseen quality and supply issues added costs. "Once this experience was known in reality rather than the over-enthusiastic estimates of financial analysts, it opened the door for NAFTA-based enterprises to compete effectively with a real price and not just an imaginary one.
"There have been continuing improvements in automation and the like, but this is an underlying issue, not a main cause of reshoring," Bessemer said.
Glenn Frohring, president of Absolute Haitian Corp., Worcester, Mass., said the energy efficiency of new equipment has been huge for U.S. processors. Rising labor costs in Asia and logistics plagued by congestion at ports have been important as well.
"Savings in energy costs is so good now that it makes it easy for processors to invest in new equipment," Frohring said. "That also gives them more precision."
What about investment in automation? "We do see it," he said. "To eliminate labor costs makes molders more competitive."
Frohring has another reason to like reshoring: "Haitian has a huge market share in China. I get calls from molders saying they know the molds they are bringing back to the U.S. ran well on Haitian machines over there, so we have a shot at selling them Haitians in the U.S."
Wal-Mart has boosted reshoring by its campaign to purchase more products made in the U.S. A Wal-Mart official recently noted that additional automation and lower energy costs have made U.S. manufacturers more competitive.
So how long will reshoring continue? We hope a long time. But a recent A.T. Kearney research report said the overall manufacturing reshoring trend actually reversed in 2013. A couple days later I saw a press release from robot maker Sepro Group that said North American sales were up 26 percent over 2013. Continued investment in automation is a very good sign!
•
In about six weeks, many of your colleagues will be at the NPE show in Orlando, March 23-27. In addition to more than 2,000 companies exhibiting their best products — including a significant amount in operation on the show floor — the SPI has organized conferences and side events that are alone worth the trip. SPI President and CEO Bill Carteaux's column on Page 71 of this issue provides a good summary of what's happening at NPE.
If you have not yet made up your mind about attending NPE, now is the time to make the decision to go. The North American plastics industry is surging ahead right now, and your plant will need new equipment and new expertise to keep it from being left behind.
Ron Shinn, editor
Ron Shinn | Editor
Editor Ron Shinn is a co-founder of Plastics Machinery & Manufacturing and has been covering the plastics industry for more than 35 years. He leads the editorial team, directs coverage and sets the editorial calendar. He also writes features, including the Talking Points column and On the Factory Floor, and covers recycling and sustainability for PMM and Plastics Recycling.
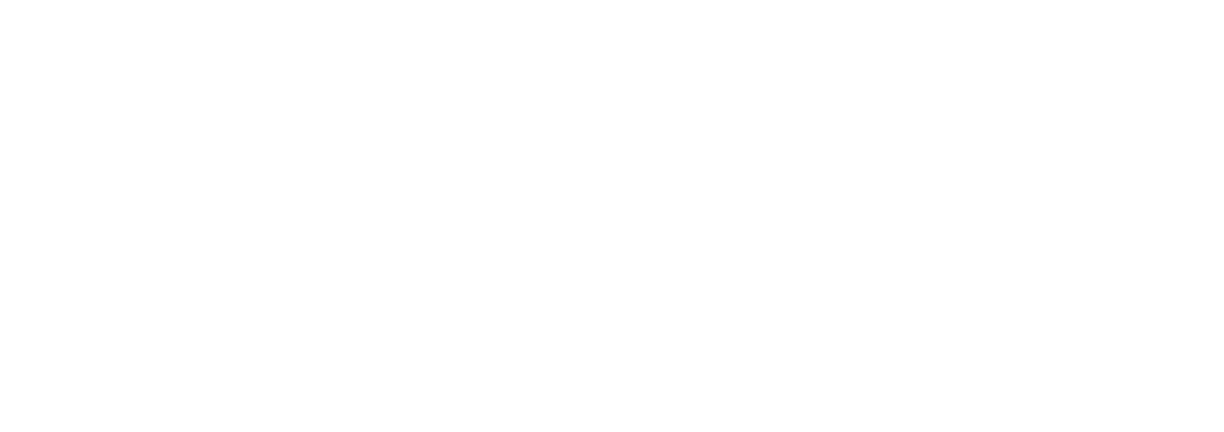