By Karen Hanna
Fifty-some years ago, two officers met on a U.S. Army base in Germany. One would eventually become my boss, retired Col. Ron Shinn. The other took a deep dive into thermoplastic polyolefin (TPO). It’s a small world.
Jay Waddell, who’s been a thermoforming consultant with Plastic Concepts & Innovations LLC since 1999, reflected on the path that led him from the Citadel to plastics plants around the world. Along the way, he’s been an administrator at a particularly unusual — and haunted — college campus, and, with his wife, met exotic animals and invented a blow molded pet product called the Skamper-Ramp. He reflected on the journey in a recent interview with Plastics Machinery & Manufacturing.
How did you get into the plastics industry?
Waddell: Back in 1982, my first wife’s family had a thermoforming business in Charleston, S.C., still in existence, Curd Enterprises. Her father was one of the pioneers in thermoforming in the early ’60s. I was in the Army, teaching ROTC at the Citadel, and decided I’d like to do something. We were a contract thermoformer, which meant that we went out and solicited jobs from all industries, different types of products. That’s where I cut my teeth. I learned a lot of things by watching how plastic heated and how it formed. It gave me a great background in how to do things and how not to do things.
How did the military academy environment of the Citadel prepare you for work in the industry, and for the rest of your life?
Waddell: It prepared me for a lot of things. My father was a graduate of the Citadel, and I was following in his footsteps. I think the military education helped shape me a little bit, and the discipline side; it taught me how to deal with unusual situations and stressful situations. I was in the Army for 23 years, 10 years on active duty and 13 years in the South Carolina Army National Guard.
PMM Editor Ron Shinn served with you in Germany. What did you do during your time in the Army?
Waddell: He was my nemesis at times, but that’s OK. He was in a higher headquarters, and he used to inspect me every now and then. It was an interesting love-hate relationship.
I was a military police officer, and I did a lot of different things. I was a security officer for a weapons-storage site in Germany, and then I ran a U.S. confinement facility, and then I ran troops. I did a lot of things in the Army and ended up teaching at the Citadel, which is what I wanted. I retired as a lieutenant colonel.
What do you do now?
Waddell: I’m a thermoforming consultant.
I partnered up with a gentleman who’s still in the consulting business, a guy named Ed Bearse out of Clare, Mich. He and I basically helped develop what’s known as TPO. I had another guy, Bob Smart, who was out of Dow; he was our extrusion guru. The three of us put together a company, and we went out and attacked the market to see if we could do something with TPO, which was used in injection molding but wasn’t used in thermoforming, because people didn't know how to extrude it. Bob figured out ways of getting it extruded. We did a lot of stuff with Solvay to develop that market in the late ’90s, early 2000s.
TPO was definitely an interesting moment. It’s basically polypropylene with a little pixie dust thrown on it to make it do stuff. That was a great thing, and we’ve developed that market.
It’s a lot of fun trying to come up with things. We’re really proud of it. We did experimental work on forming a paint film and a TPO, which are two really incompatible products; paint film doesn’t like to be formed.
We ran classes and taught thermoforming techniques, extrusion techniques and materials. Bob retired, and Ed and I decided to go our separate ways.
What are the advantages of TPO?
Waddell: It was an automotive-driven series of things. Polypropylene has been around for a long time. It’s a standard material, and a lot of products are injection molded. We kind of started a movement for getting it into being thermoformed.
We use it primarily as a substitute for ABS. A lot of parts, like on RVs, for example, are made of ABS, [which has] lots of cracking problems and that sort of stuff. We also looked at it because the automotive industry was already using it in injection molded things. We looked at how we could convert it into thermoforming, mainly because the tooling costs are a lot less. Part cost is a little more, but it’s offset by tooling costs, and we’re able to ramp up into production quicker than you could with injection molding at less cost.
And now you find it out there a lot in a lot of different industries. The heavy truck industry, side skirts, for example, on cabs and stuff, are TPO modifications.
Would you say that opened more of the automotive market to thermoformers?
Waddell: Absolutely. It’s opened up the markets for the RV industry and the trucking industry and automotive industry.
What’s changed since you started in the industry?
Waddell: Material advances have gotten better, and equipment has gotten far better. Polyethylene was a very strange beast that people were somewhat afraid of. The material suppliers did a really good job working on their materials and, in the polyolefins especially, becoming more proficient in extruding material and meeting specs.
The machinery and machine control are far more sophisticated. We didn’t have all the measuring devices we have now. Heat control is better, which is a key element in any forming operation. The measurement of heat is far better. Rather than trying to do a hand-hold and just eyeballing a machine to look at if it’s right, it’s all based on instrumentation.
The bathtub industry [has] machines that will form the tub and then bend down in the front of the tub with what we call articulating frames. The sophistication is based upon the machines.
I’ve seen a lot of interesting things. We were doing a bumper for a big automotive company. It was a large piece, and we had to use articulated frames to bend the material around the mold at the same time, we were putting a plug assist into it, and it was paint films. It was very sophisticated.
The controls are very important to it, because we use different techniques to form things. We blow bubbles; we pull material up into a bubble — pre-stretch is what it’s called. We use air pressure; to do that, you have to have the machinery, the ability to control the process correctly.
As people become more familiar with AI and look at its possibilities, I think it’s going to be integrated more into the heavy-gauge thermoforming process. It’s already there to certain degree, I think, in the inline process now, where you’re doing fast-moving parts. The thermoforming side, the heavy-gauge cut sheet, is standing on the edge of the cliff, to step off into the AI world.
While immersed in the technical world of plastics, you took a decade-long foray into a far more artisanal environment, as COO for administration at the American College of the Building Arts. Tell me about that.
Waddell: A classmate of mine from the Citadel had a small college down here called the American College of the Building Arts, a great institution that teaches traditional building skills, as well as awarding a four-year degree. Through sheer stubbornness, [we] resurrected the college. The college was not doing well when I arrived. ... How did we manage to pull the rabbit out of the hat? Good fiscal management. We cut a lot of spending. We minded our pennies and nickels. My second wife, Ginna, was very much involved with me.
It was interesting running a college, from a manufacturing background, and looking at what the craftsmen were teaching students. They learn carpentry, timber framing, stonework, plaster; it’s just a conglomeration of great classical trades.
After about 10 years, you reach a point where you say, “Time to change out a little bit.” My wife and I retired from the college at the beginning of COVID.
What comes next?
Waddell: I’m still doing consulting and enjoying that, so life is good. I’m trying to retire; I haven't made it yet.
Do you see some of the same problems from plant to plant?
Waddell: Training is one of those areas right now. There’s been some attempts to put together, basically, an automated form to teach, but mostly companies do a lot of in-house teaching. A college like the American College for Building Arts can’t teach you everything you need to know about a particular trade; neither can I in giving thermoforming lectures.
It’s pretty amazing, because, in the evolution of companies and personnel, the older body of knowledge retires, and the younger body of knowledge doesn’t necessarily have the same bandwidth to understand it. Understanding the processes is a never-ending thing in the thermoforming industry, teaching people how material should be heated, how it should be formed, how it should be cooled. This will be an ongoing thing.
Heat transfer is one of the major issues in heavy-gauge thermoforming, and that’s one of those areas I think will need some more attention. I’ve found a lot of interesting ways of people doing things because “it worked, so, therefore, if it works, it’s got to be the right way.” And it’s not necessarily the most efficient way, but they did it out of necessity. Young engineers are using more data-driven analysis of how to read the thermoforming process, and I think that’s a good thing.
What challenges do you see for the industry?
Waddell: I’m a director and treasurer of the Society of Plastics Engineers (SPE). I deal on a large-scale basis on the technical side of plastics, and one of our big concerns is looking at anti-plastic lobbying. Some [plastics uses] should be changed; quite frankly, they are harmful to the environment, but they’re necessary. How do we work to take our stakeholders and let them see what they’re doing and what they can change and help mitigate? I don’t think you’ll ever get rid of plastics.
We dispose of plastics in a very careless manner globally. Until we get some kind of global strategy to work on recycling and containment of plastic pollution, [plastics pollution is] going to continue, and it keeps increasing.
I think in the United States, the industry is doing enough. I think Europe is working hard.
I’ll give you an example: You get a plastic bottle with a plastic cap. In the United States, when you unscrew the cap, the cap comes off the bottle; now, you’ve got two pieces. What happens to them? Well, the cap may go in the garbage and the bottle goes into recycling, or the cap gets thrown someplace else. In Europe, the caps stay with the bottle. That’s a significant amount of plastics that is kept together.
You go to Third World countries, it’s, “Let’s make it as fast and cheap as we can.” We used to ship all our computers to China by the container-load, and they would burn the ABS and salvage stuff out. That’s pretty well calmed down. But it is no different than taking a barge-load of trash from New York and shipping it to Mississippi. That’s what’s happening globally: Third World countries are being inundated with that, and they’ve got tremendous problems, and I’m not sure how they’re going to get addressed. I don't think the plastics industry globally is prepared to spend the money to start fixing these things. They’re making some inroads, but it’s a slow march.
Bioplastics has somewhat of a future. A lot of work is being done on taking plastic and breaking it down and then reusing those components to manufacture more plastic. That’s got a long ways to go, but it’s promising.
We have to be careful about what we call biodegradable because there are things out there called biodegradable plastics that aren’t.
Where do the solutions have to come from?
Waddell: It comes from consumer demand and trickles up to governments. Everybody talks about recycling. Well, great. And what’s the market for recycled plastic? It can cost more to recycle it than you can buy it new.
Why is being on the SPE board important to you?
Waddell: I joined the SPE thermoforming board back in the late ’80s for networking and meeting other people and learning about different folks in different industries. As a net result, they elected me to be a counselor. That exposed me to the more national, more global network of things. I just thought it was important to get involved in a higher level, more strategic level of the industry. I’m working with major plastic chemical companies. I get satisfaction out of being able to work with great people and trying to come up with the strategies to make the plastics industry better.
We look at things at the society level, looking at a lot of policy. We try to provide the best technical information to the industry. Our journals are unmatched in their technical ability. Between the chapters and divisions and the national headquarters, we put on a lot of webinars and things.
What do you like to do in your free time?
Waddell: I’ve got a boat. I was a consultant; you’ve got to play golf. And I like music concerts. I do a lot of traveling with my wife. We probably have three or four major trips a year around the world. In August, we’re going to do a circumnavigation of Iceland on a cruise, and then in November, I go to the opposite end of the world, to Antarctica.
I kind of want to do the North Pole and South Pole. I can’t get to the North Pole. I can't really get to the South Pole, but I can get to where they’re located. We’ve gone to Africa probably six or seven times, and that’s where I see a lot of plastic pollution; it’s pretty bad. I’ve done South America a lot. Asia, I’ve been to China a few times.
Any favorites?
Waddell: Africa, the people and the wildlife, the adventure of getting there. We go out to very remote camps, very small safari camps, where there’s probably only 10 people. I get to see some of the most amazing sights of what Mother Nature has to offer. I don't go to sit at some resort with a fancy pool; I go to experience what’s around me.
What would you like your legacy to be?
Waddell: I’d like to be remembered as an individual who tried to help the plastics industry get better, to improve the overall image and competence of the industry, particularly in thermoforming.
Just the facts
NAME: James M. "Jay" Waddell
WHO IS HE: Founder of Plastic Concepts & Innovations, Mount Pleasant, S.C.; board member and treasurer of the Society of Plastics Engineers (SPE)
AGE: 74
Karen Hanna | Senior Staff Reporter
Senior Staff Reporter Karen Hanna covers injection molding, molds and tooling, processors, workforce and other topics, and writes features including In Other Words and Problem Solved for Plastics Machinery & Manufacturing, Plastics Recycling and The Journal of Blow Molding. She has more than 15 years of experience in daily and magazine journalism.
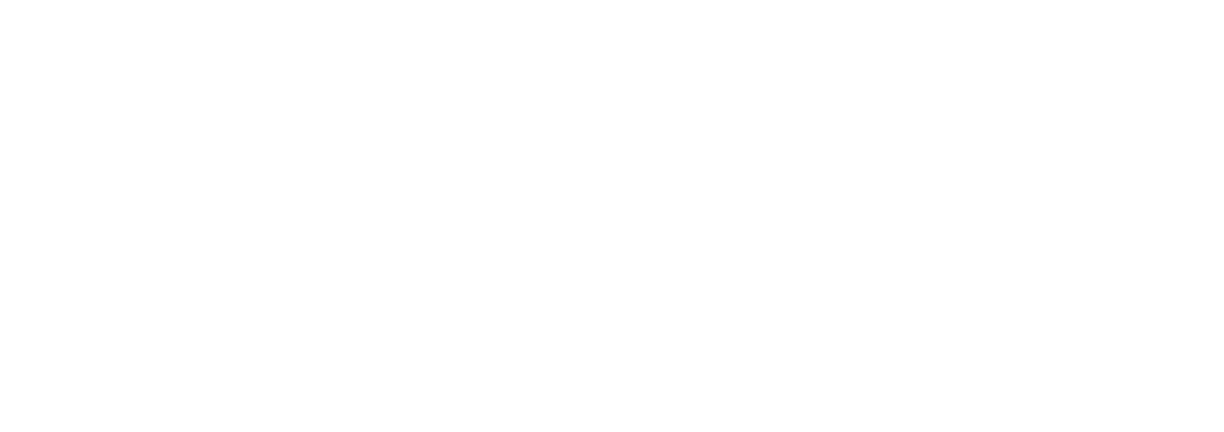