Read more on the labor crunch: https://plasticsmachinerymanufacturing.com/21248002/.
By Karen Hanna
Martin Smith found his way to the plastics industry by chance. A musician, he is looking to better his earning potential while he pursues his passion and works toward his dream job — helping veterans cope with post-traumatic stress disorder through music.
In the meantime, he is learning maintenance skills through an apprenticeship at his company, G&G Industries Inc., Shelby Township, Mich., which molds automotive interiors.
“I decided on the maintenance path, as I’ve worked the line numerous years and couldn’t go any higher as far as that goes, so I went from an operator to a mold setter, then a maintenance tech,” the 37-year-old said.
Employers and workforce development experts outlined a number of paths for workers to enter and grow within the plastics industry, but acknowledged the manufacturing community as a whole must do more to attract and retain employees. Challenges include overcoming perceptions of manufacturing jobs as dirty, dangerous or overly strenuous, as well as reaching out to younger people, even elementary school-aged children.
Pyramid Plastics Group, for example, is always willing to show visitors around its plant floor, where workers use more than two dozen Toshiba, Nissei and LS Mtron presses to make parts for the automotive, fluid-management, consumer-products and medical industries. The company, in Rockford, Ill., also makes molds, including tooling for COVID-19 test kits. To boost the number of manufacturing workers, COO Andrew Peterson advocates a multi-pronged approach — reach out to younger people, and welcome more foreign workers.
The company prides itself on its culture, and it is looking for more people who want to work as a team and do “business the right way,” Peterson said.
“We need to allow more H-1B visas and encourage youth that manufacturing is a path to a good living without a four-year college degree,” he said.
Building a bright future
Experts say the opportunities available to newcomers to the plastics industry can be eye-opening.
Production employees in the plastics industry pulled down an average salary of $40,857 and a median salary of $37,970 in 2018, according to “An Analysis of Workforce Development Issues in the U.S. Plastics Industry,” by Perc Pineda, chief economist of the Plastics Industry Association.
“In the industrial sector, there are no longer white-collar versus blue-collar jobs, but instead, new-collar jobs that don’t require working in a dark, outdated factory, but rather a high-tech factory floor utilizing new technologies including AI [artificial intelligence], factory automation and machine learning. This generation’s manufacturing industry is clean, safe, and modern,” said Tony Uphoff, the president and CEO of Thomas, the parent company of Thomasnet.com, a leading platform for product sourcing and supplier selection for industrial and manufacturing companies.
In a study by digital toolmaker Parsable, Uphoff said 65 percent of Millennials — people between the ages of about 25 and 40 — believe that starting pay for entry-level manufacturing work is lower than the average salary. But that’s not true.
“The fact is that entry-level manufacturing jobs actually start at salaries of $60,000, while Glassdoor says that the average entry-level job in the U.S can start as low as $28,000,” Uphoff said.
Walk-ins wanted
According to the National Center for Education Statistics, about two-thirds of the 3.2 million students who earned a high school diploma or equivalent credential in the first nine months of 2019 — the most recent period for which data exists — enrolled in two- or four-year institutions by October 2019; of them, about two-thirds went on to pursue bachelor’s programs.
Percentages for 2018 were similar, with about 69 percent of students continuing their formal education immediately after earning their diploma. Of those who did not, about 40 percent weren’t in the workforce, either.
But well-paying manufacturing jobs are in reach even for adults without traditional four-year degrees. According to a Deloitte analysis, the fastest-growing manufacturing jobs often require no formal postsecondary education.
“We do a lot of on-job training. A lot of stuff we do is nothing similar to anyone else around us within hundreds of miles, so you won’t find anyone with much experience, so most of it is on-job training,” said Dakota Kieffer, co-owner of Plastics Unlimited, a Preston, Iowa, thermoformer. “Some manager-level-type positions we want to make sure they’ve had management experience. … Most of the jobs we’re looking for are machine operators, more entry-level, so they do not have to have any experience at all. We do on-job training.”
Beefing up the workforce
While the challenges presented by the labor shortage aren’t insurmountable, Jason A. Tyszko, VP of the Center for Education and Workforce at the U.S. Chamber of Commerce Foundation, said employers are going to have do more to develop the workforce. He is an advocate of a proactive, collaborative approach.
“Through collective action, they’re able to actually have a much more sizable impact, in terms of the education and workforce partnerships they can broker in the type of shared benefit and return on investment they could activate on a behalf of a network of companies that have a shared workforce need and shared pain points,” he said.
The foundation has begun implementing a curriculum, called Talent Pipeline Management (TPM), that can help guide businesses and business associations to assess and address issues, such as staffing concerns, that affect them. With TPM, companies can identify the skills they need workers to have and locate where they are likely to find people who can fill those roles. The technique can help companies address myriad HR problems, said Tyszko, who listed lowering onboarding and training costs, and improving diversity as possible projects.
“You can say, do we want to double down on those sources and make sure they have the capacity to meet our need? Or do we need to start looking to activate new sources of talent, and work with them more intentionally, to meet our projected demand?” he said. “We just provide a methodology and build capacity in their associations to be able to deliver this to them.”
As an example, he cited a project the foundation undertook with a collaborative of manufacturing companies in northern Kentucky. Working together, the companies had evaluated a program offered by a local technical college. It wasn’t meeting their needs.
“They were able to rebrand that program. It became an enhanced-operator program. They were able to move it from seat time to competency-based learning. They did something like … they cut it down to less than half the time to complete; they cut the cost down to less than half,” he said. And they were having people getting enrolled and credentialed and getting jobs like never before.”
Using TPM, the U.S. Chamber of Commerce Foundation has trained nearly 500 organizations so far, with plans to scale up to more than 5,000 next year.
Doubling down on apprenticeships
One workforce-development strategy is the path Smith is now traveling — apprenticeships.
“If you can’t buy the skills you need in the marketplace, the only viable alternative is to grow your own; my advice is to just get started,” said Nicholas Wyman, the president of the Institute for Workplace Skills & Innovation (IWSI), an organization that helps manufacturers develop apprenticeships.
Though the rate of young Americans entering apprenticeships over the past decade has increased significantly, Wyman said the U.S. still lags behind Germany and the U.K. He said the COVID-19 pandemic has exposed vulnerabilities in the supply chain, including the scarcity of manufacturing professionals.
“Plastics is an industry that is here to stay — the use of plastics in manufacturing is so widespread, it touches nearly every industry,” Wyman said. “But it’s fair to say the plastics sector (and the manufacturing sector more broadly) has underinvested in workforce development in recent years and is currently facing some challenges in attracting new talent into the industry.”
Both Wyman and Uphoff are evangelists for the learn-by-doing opportunities that apprenticeships offer.
Educational opportunities are among the five most valued benefits among employees, Uphoff said. The others — as identified by Thomas’ Career Advancement for Manufacturing Survey — are health insurance, remote work options, regular performance reviews and a flexible schedule.
By updating and standardizing apprenticeship programs, Wyman believes the entire manufacturing sector could better ensure a pipeline to well-qualified, prepared workers. He pointed to Australia, which, in response to the COVID-19 crisis, is providing wage subsidies of 50 percent — or up to $28,000 a year — for people enrolled in apprenticeship programs.
Wyman believes the investment is worth it.
“Apprenticeships are the perfect model for skills development within manufacturing, as they provide apprentices with a structured program to build their technical skills base and workplace experience, and employers benefit from being able to customize the apprentices’ training program to the needs of their organization/worksite,” he said.
In addition to cultivating a source of talent, employers with apprenticeships can realize other goals as well, he said.
“Apprenticeships can be a source of strategic advantage, unlocking a range of cultural diversity and inclusion benefits, such as innovation, productivity and retention benefits,” Wyman said.
Putting in the work
The workforce-development experts agreed: Employers can’t wait for applicants to show up at their plants; they have to take action on their own.
Creating a skilled, engaged and loyal workforce requires it.
Working together, employers can solve the labor shortage, Tyszko said.
“What’s not going to happen is nobody’s going to just show up and save the day. There’s no easy button here. It does require work and intentionality, but, like I said before, it’s not rocket science,” he said.
Contact:
IWSI, Lexington, Ky., www.iwsiamerica.org, [email protected]
Thomasnet.com, New York City, www.thomasnet.com
U.S. Chamber of Commerce Foundation, Washington, D.C., 202-463-5500, www.uschamberfoundation.org
Karen Hanna | Senior Staff Reporter
Senior Staff Reporter Karen Hanna covers injection molding, molds and tooling, processors, workforce and other topics, and writes features including In Other Words and Problem Solved for Plastics Machinery & Manufacturing, Plastics Recycling and The Journal of Blow Molding. She has more than 15 years of experience in daily and magazine journalism.
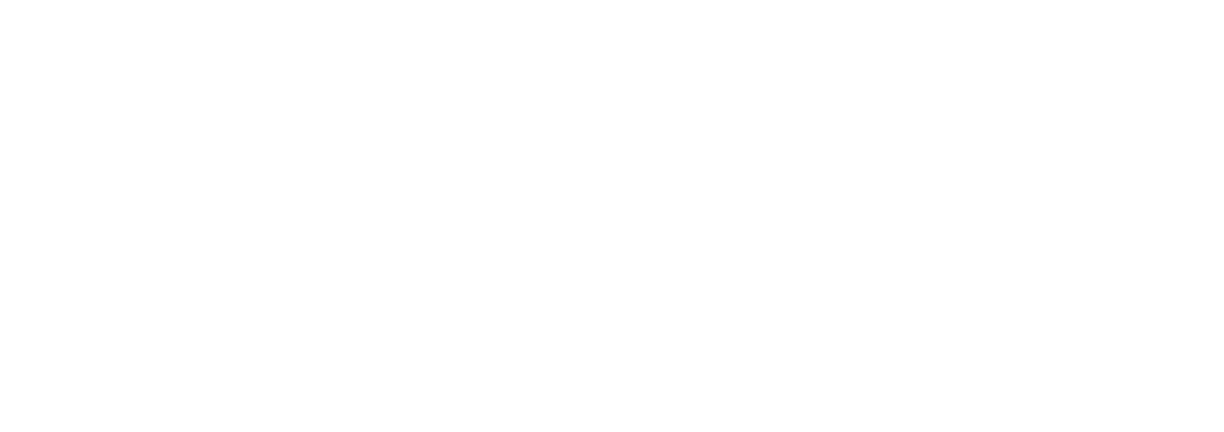