Cannon offers new mixing head for glass-fiber-reinforced PU
Interwet LFI technology Cannon’s Interwet-LFI (Long Fiber Injection) technology lets users produce glass-fiber-reinforced PU (GFR-PU) parts and components that can be used for structural and semi-structural applications. Cannon’s Free Pouring Laminar (FPL) SR L-shaped high-pressure mixing head uses the Interwet-LFI technology, and employs a vacuum to pull dry roving through a fiberglass chopper positioned above the head, with a second vacuum to draw the chopped glass fibers into the mixing chamber. A two-component PU formulation then wets the fibers to create a homogenous blend that is sprayed into a heated mold. The Interwet-LFI technology is automatic and highly flexible, allowing for a wide range of fillers with a fiber volume fraction of up to 50 percent.
What’s new? The FPL 30 Interwet-LFI mixing head, which debuted at the Composites and Advanced Materials Expo in Atlanta in November. Cannon provided an example of an application where the FPL 30 mixing head was used with a three-component dosing machine, with the head mounted to a dedicated robot incorporated into a Cannon turnkey line with multiple presses to produce mechanically reinforced external parts for agricultural machinery.
Benefits Faster, easier production. Interwet-LFI provides an alternative to other production processes that rely on glass mats or chopped glass fiber pre-blended with polyol. Users can optimize part attributes such as tensile strength and fiber loading by adjusting fiber length from 12.5mm to 100mm during the spraying cycle. Deflectors near the spray head’s nozzles control fiber orientation, allowing for more uniform lay-down in shallow and/or deep ribbed thin-walled parts, as well as thicker load-bearing components. To add stiffness, strength and durability, users can spray the reverse side of highly aesthetic thermoformed components, such as external body panels for buses and other vehicles, with a GFR-PU layer. When high surface aesthetics are not required, such as for manhole covers, frames and chambers, the Interwet-LFI process can be used alone. GFR-PU parts are much lighter than their steel counterparts, cutting out the need for heavy installation equipment and saving time, labor and costs.
Cannon USA Inc., Cranberry Township, Pa., 724-772-5600, www.cannonusa.com
David Tillett
Associate Editor David Tillett writes and edits for Plastics Machinery & Manufacturing, Plastics Recycling and The Journal of Blow Molding. He covers new products, industry news, patents and consumer and business equipment. He has more than 20 years of experience in daily newspaper, online and magazine journalism.
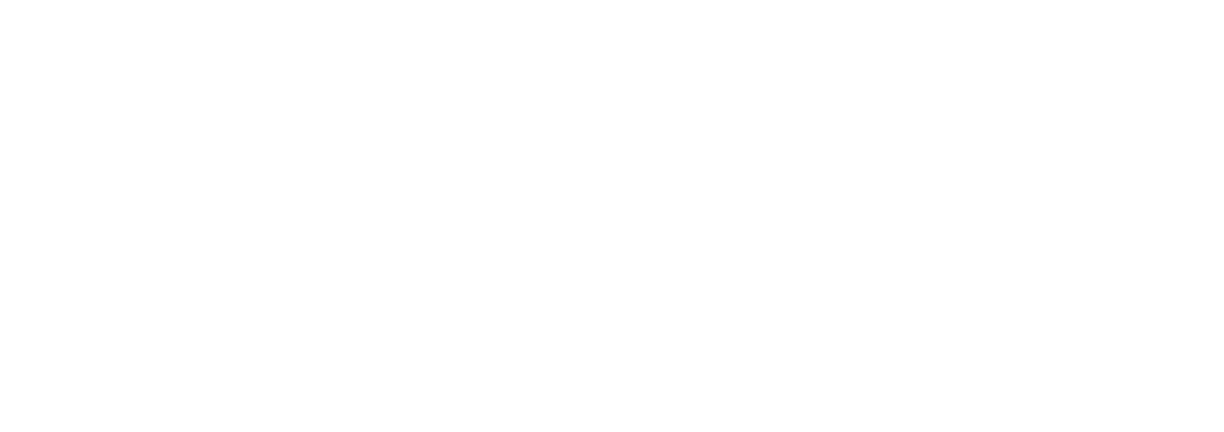